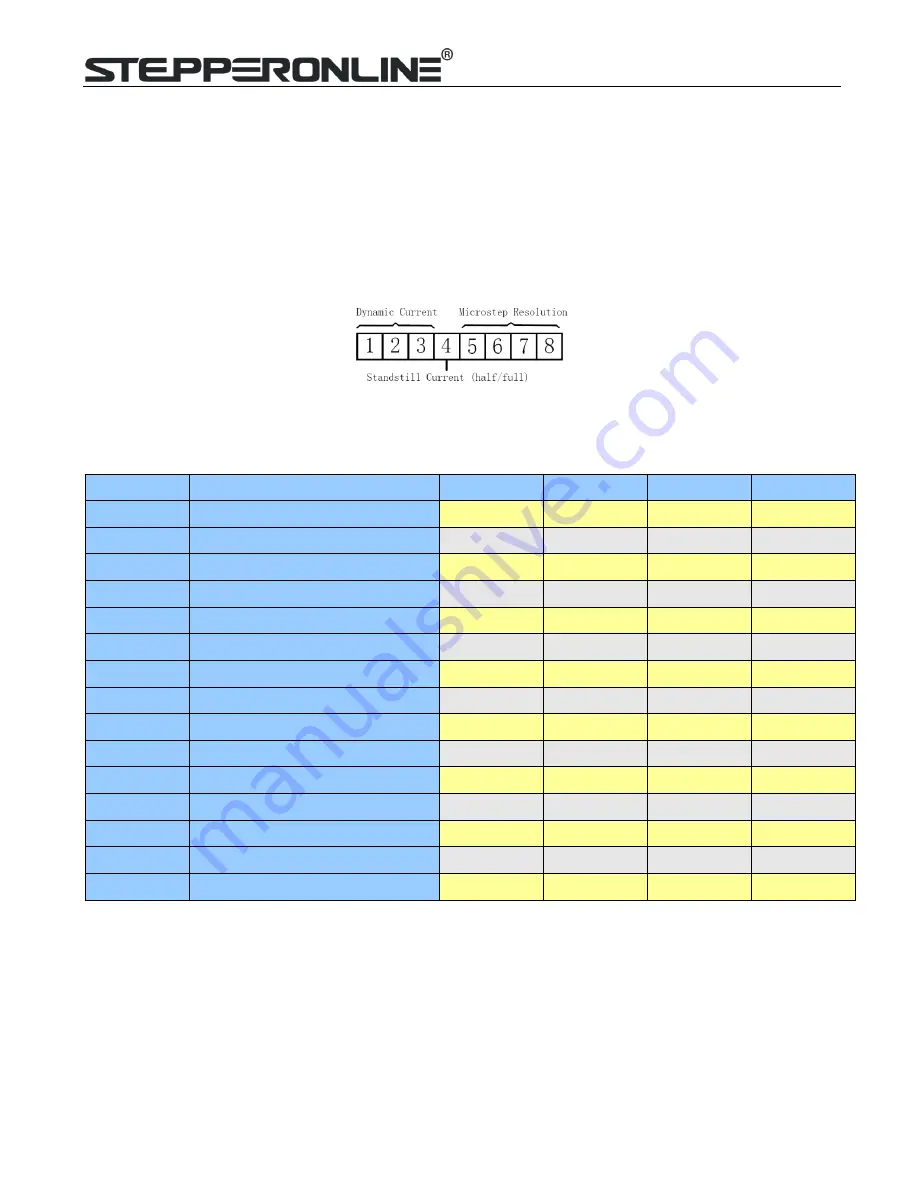
DM556T Digital Stepper Drive User Manual
8
of +24 - +48 VDC, leaving room for power line voltage fluctuation and back-EMF.
Higher supply voltage can increase motor torque at higher speeds, thus helpful for avoiding losing steps. However,
higher voltage may cause bigger motor vibration at lower speed, and it may also cause over-voltage protection or
even drive damage. Therefore, it is suggested to choose only sufficiently high supply voltage for intended applications.
7. DIP Switch Configurations
This drive uses an 8-bit DIP switch to set microstep resolution, and motor operating current, as shown below:
7.1 Microstep Resolution Configurations
Microstep resolution is set by SW5, 6, 7, 8 of the DIP switches
as shown in the following table:
Microstep
Steps/rev.(for 1.8°motor)
SW5
SW6
SW7
SW8
2
400
OFF
ON
ON
ON
4
800
ON
OFF
ON
ON
8
1600
OFF
OFF
ON
ON
16
3200
ON
ON
OFF
ON
32
6400
OFF
ON
OFF
ON
64
12800
ON
OFF
OFF
ON
128
25600
OFF
OFF
OFF
ON
5
1000
ON
ON
ON
OFF
10
2000
OFF
ON
ON
OFF
20
4000
ON
OFF
ON
OFF
25
5000
OFF
OFF
ON
OFF
40
8000
ON
ON
OFF
OFF
50
10000
OFF
ON
OFF
OFF
100
20000
ON
OFF
OFF
OFF
125
25000
OFF
OFF
OFF
OFF
7.2 Current Configurations
For a given motor, higher drive current will make the motor to output more torque, but at the same time causes more
heating in the motor and drive. Therefore, output current is generally set to be such that the motor will not overheat
for long time operation. Since parallel and serial connections of motor coils will significantly change resulting
inductance and resistance, it is therefore important to set drive output current depending on motor phase current,
motor leads and connection methods. Phase current rating supplied by motor manufacturer is important in selecting
drive current, however the selection also depends on leads and connections.
The first three bits (SW1, 2, 3) of the DIP switch are used to set the dynamic current. Select a setting closest to your