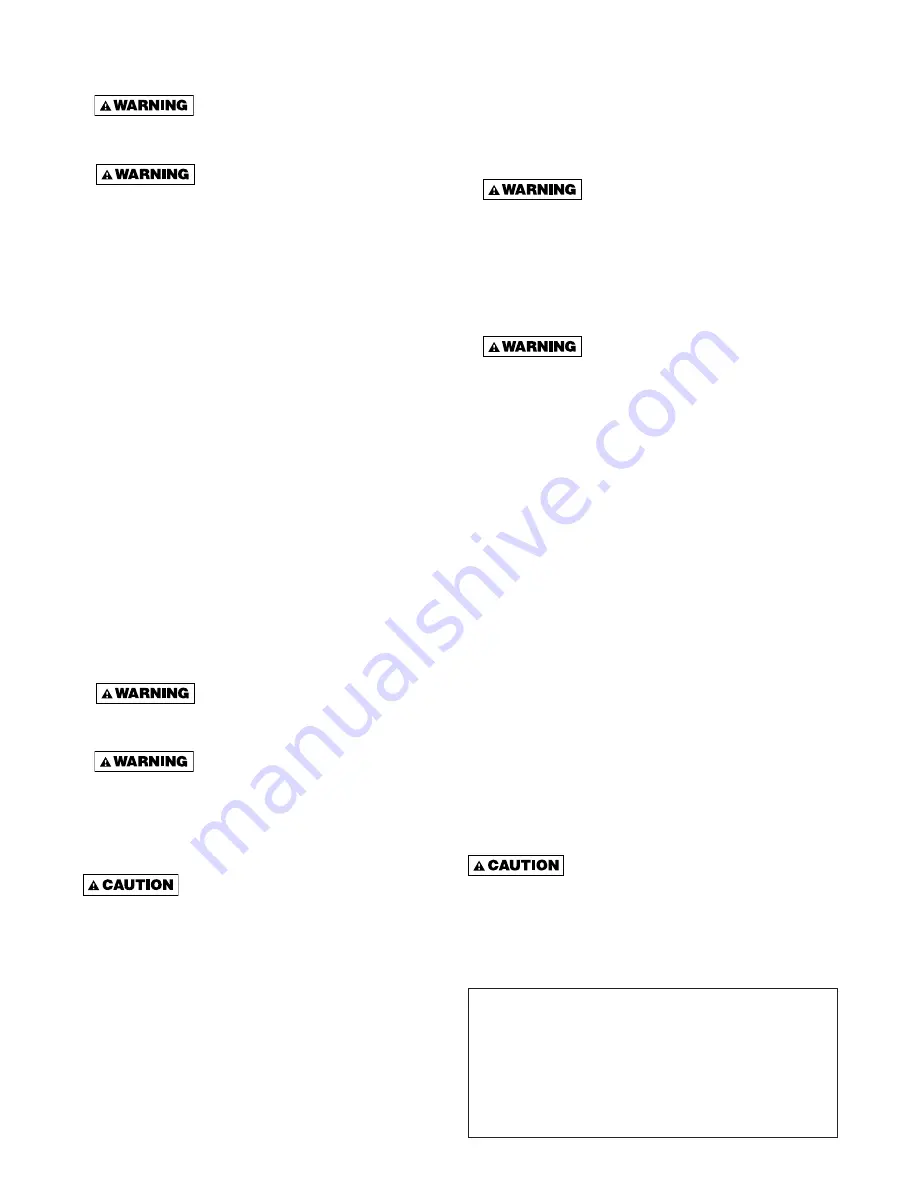
3
GENERAL SAFETY INFORMATION
Failure to comply with the general
safety information may result in extensive
property damage, severe personal injury or death.
This product must be installed by
a licensed plumber or gas fitter when installed
within the Commonwealth of Massachusetts.
Installation must be made in accordance with local
codes, or in absence of local codes, with the latest
edition of ANSI Standard Z223.1 (N.F.P.A. No. 54)
National Fuel Gas Code.
All of the ANSI and NFPA
Standards referred to in these installation instructions are
those that were applicable at the time the design of this
appliance was certified. The ANSI Standards are available
from the CSA Information Services, 1-800-463-6727. The
NFPA Standards are available from the National Fire
Protection Association, Batterymarch Park, Quincy, MA
02269. These duct furnaces are designed for use in
airplane hangars when installed in accordance with
current ANSI/NFPA No. 409 and in public garages when
installed in accordance with current NFPA No. 88A and
NFPA No. 88B.
If installed in Canada, the installation must conform with
local building codes, or in absence of local building
codes, with CGA-B149.1 “Installation Codes for Natural
Gas Burning Appliances and Equipment" or CGA-B149.8
“Installation Codes for Propane Gas Burning Appliances
and Equipment”. These indoor duct furnaces have been
designed and certified to comply with CGA 2.6. Also
see sections on installation in AIRCRAFT HANGARS
and PUBLIC GARAGES.
Do not alter the duct furnace in
any way or damage to the unit and/or severe
personal injury or death may occur!
Disconnect all power and gas
supplies before installing or servicing the heater.
If the power disconnect is out of sight, lock it in
the open position and tag it to prevent unexpected
application of power. Failure to do so could result
in fatal electric shock, or severe personal injury.
Insure that all power sources conform
to
the requirements of the unit heater or damage to
the unit will result!
Follow installation instructions CAREFULLY to avoid
creating unsafe conditions. All wiring should be done
and checked by a qualified electrician, using copper wire
only. All external wiring must conform to applicable local
codes, and to the latest edition of the National Electric
Code ANSI/NFPA No. 70. All gas connections should be
made and leak-tested by a suitably qualified individual,
per instructions in this manual.
Also follow procedures listed on the “Gas Equipment
Start-up” sheet located in this manual.
Use only the fuel for which the heater is designed (see
rating plate). Using LP gas in a heater that requires natural
gas, or vice versa, will create the risk of gas leaks, carbon
monoxide poisoning and explosion.
Do not attempt to convert the
heater for use with a fuel other than the one
intended. Such conversion is dangerous, and
could create unsafe conditions that result in death,
serious personal injury or property damage.
Make certain that the power source conforms to the
electrical requirements of the heater.
Do not depend upon a thermostat
or other switch as sole means of disconnecting
power when installing or servicing heater. Always
disconnect power at main circuit breaker as
described above. Failure to do so could result in
fatal electric shock.
Special attention must be given to any grounding
information pertaining to this heater. To prevent the risk of
electrocution, the heater must be securely and adequately
grounded. This should be accomplished by connecting a
grounded conductor between the service panel and the
heater. To ensure a proper ground, the grounding means
must be tested by a qualified electrician.
Do not insert fingers or foreign objects into the heater or
its air moving device. Do not block or tamper with the
heater in any manner while in operation or just after it has
been turned off, as some parts may be hot enough to
cause injury.
This heater is intended for general heating applications
ONLY. It must NOT be used in potentially dangerous
locations such as flammable, explosive, chemical-laden
or wet atmospheres.
In cases in which property damage may result from
malfunction of the heater, a backup system or a
temperature sensitive alarm should be used.
The open end of piping systems being
purged shall not discharge into areas where there are
sources of ignition or into confined spaces UNLESS
precautions are taken as follows: (1) By ventilation of
the space, (2) control of purging rate, (3) elimination
of all hazardous conditions. All precautions must be
taken to perform this operation in a safe manner!
Unless otherwise specified, the following conversions
may be used for calculating SI unit measurements:
1 foot = 0.305 m
1 inch = 25.4 mm
1 gallon = 3.785 L
1 pound = 0.453 kg
1 psig = 6.894 kPa
1 cubic foot = 0.028 m
3
1000 Btu per hour = 0.293 kW
1 inch water column = 0.249 kPa
1000 Btu/Cu. Ft. = 37.5 MJ/m
3
liter/second = CFM x 0.472
meter/second = FPM
÷
196.8
Summary of Contents for NATURAL INDOOR GAS-FIRED DUCT FURNACE
Page 14: ...14 Figure 12A Figure 12B...
Page 15: ...15 Figure 13A Figure 13B...
Page 34: ...34 NOTES...
Page 36: ......