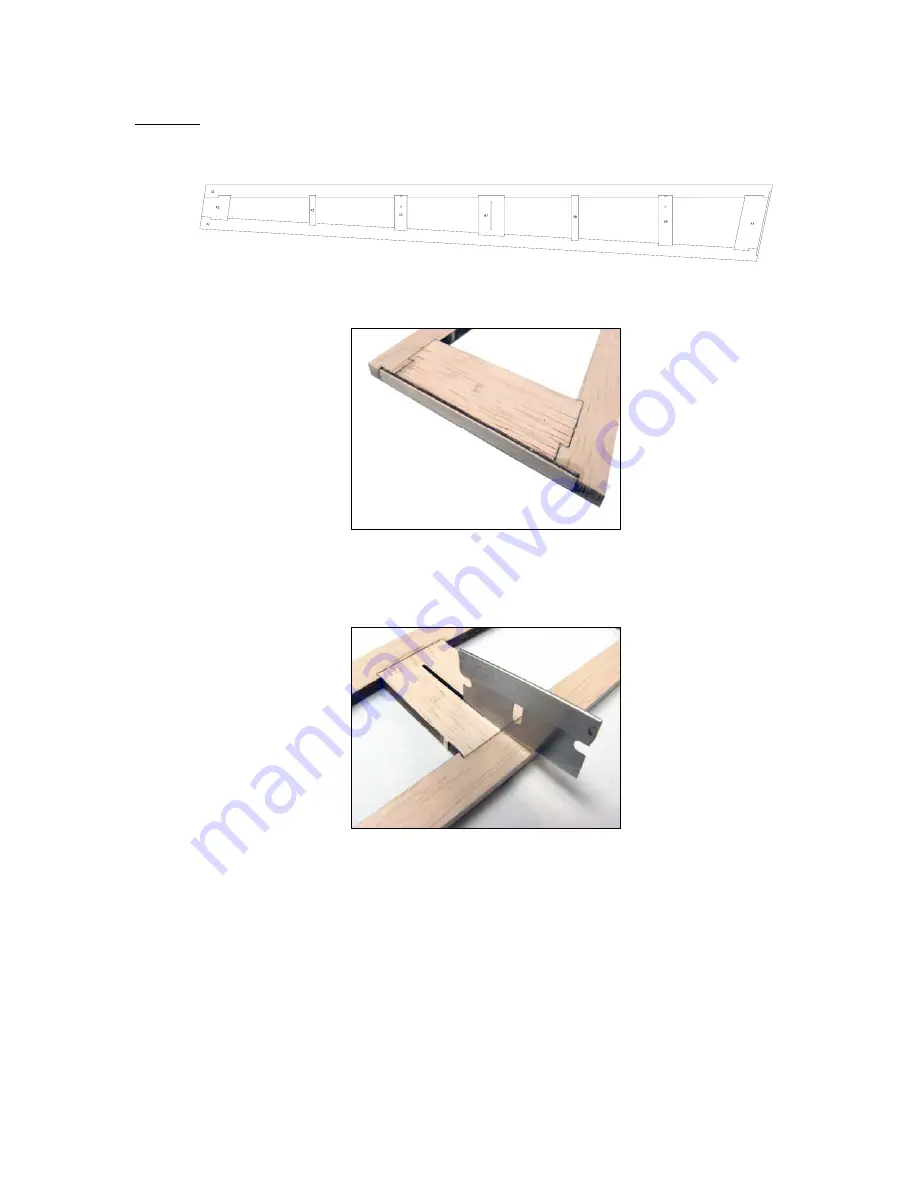
© 2007 Stevens AeroModel.
Page 28 of 35
Ailerons:
1.
Assemble two (2) ailerons as illustrated below from 3/16” balsa parts A1, A2, A3, A4, A5, A6, A7, A8, and A9.
2.
With the balsa ailerons complete locate the 1/16” ply part marked “A10” and install to recessed area of inside
edge of balsa aileron bordering “A4”.
3.
*** OPTIONAL STEP for those wishing to run a split aileron / flap wing system you can cut the ailerons into two
pieces at A7 (A7 is partially pre-cut for this application) and purchase an additional set of DuBro Micro Razor
Control horns DUB936 and Auxiliary BEC device to support the additional servo load. We are simply illustrating
where we have accommodated this requested feature as running split ailerons is an advanced option for
experienced modelers and is beyond the scope of this manual. ***