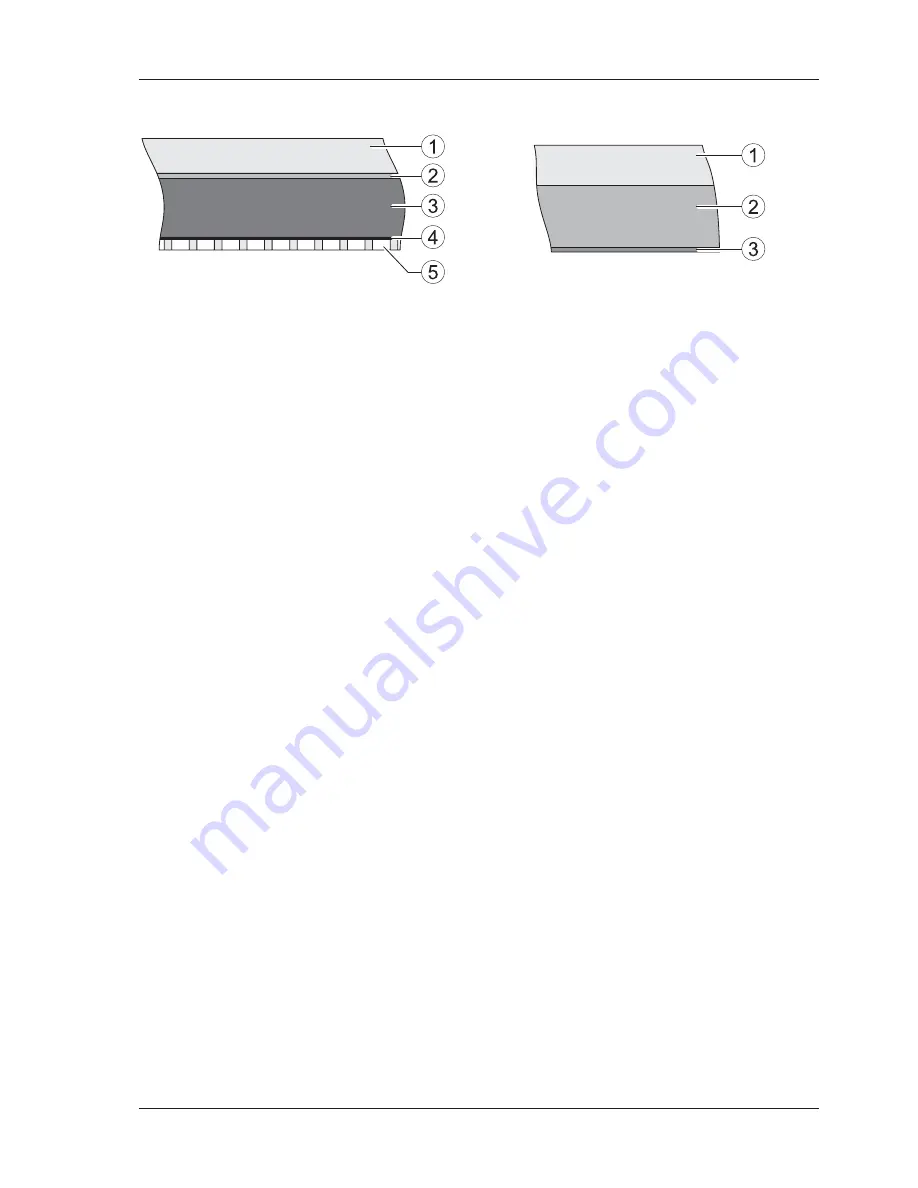
Z001007/0_4_September 2007
Page NOISE ATTENUATION-5
NOISE ATTENUATION
INSTALLATION INSTRUCTION
14. 4. NOISE-ABSORBING MATERIAL
ill. 14/5
noise-absorbing material for engine hood made
of wood (plywood 5/8" / 15 mm) or 1/12"
(2 mm) steel plate
1
engine hood
2
lead sheet, 0,5 line (1 mm)
3
mineral cotton, 2" (50 mm)
4
plastics foil
5
perforated aluminum sheet, 0,5 line
(1mm), perforation 20%
ill. 14/6
noise-absorbing material for engine hood made
of 1/12" (2 mm) steel plate or wood (plywood
5/8" / 15 mm)
1
engine hood
2
flame-proof absorbing mat,
e.g.: "Porolon", "Revertex
Acoustics" or Baryfoil.
3
flame-proof reflecting sound-
absorbing foil (ferruginous PVC,
thickness 1/10" / 2,5 mm)
15% of the engine-sided surface to
be provided with absorbing mat.
Noise-absorbing material on ill. 14/5 shows a construction for extremely high insulation requirements, also
containing a lead sheet layer. This construction is very stable and is also recommended for engine compartments
the walls of which are for different reasons weaker than recommended.
Under the same conditions as shown on ill. 14/5, one single layer of a flame-proof insulating mat, e.g. "Porolon",
"Revertex Acoustics" or "Barifoil" may be glued directly onto the inner side of the engine protection. This noise-
absorbing material will in many cases be sufficient. Use contact glue.
Such material requires little space and is easy to handle. All surfaces to be glued must be completely grease-
and moisture-free, to achieve and maintain good adherence.
Many different noise-absorbing materials are available on the market, but only materials meeting the current
requirements as to fire protection and noise reduction may be used.
Finished noise-absorbing mats with absorbing layers for soundproofing are also available on the market.