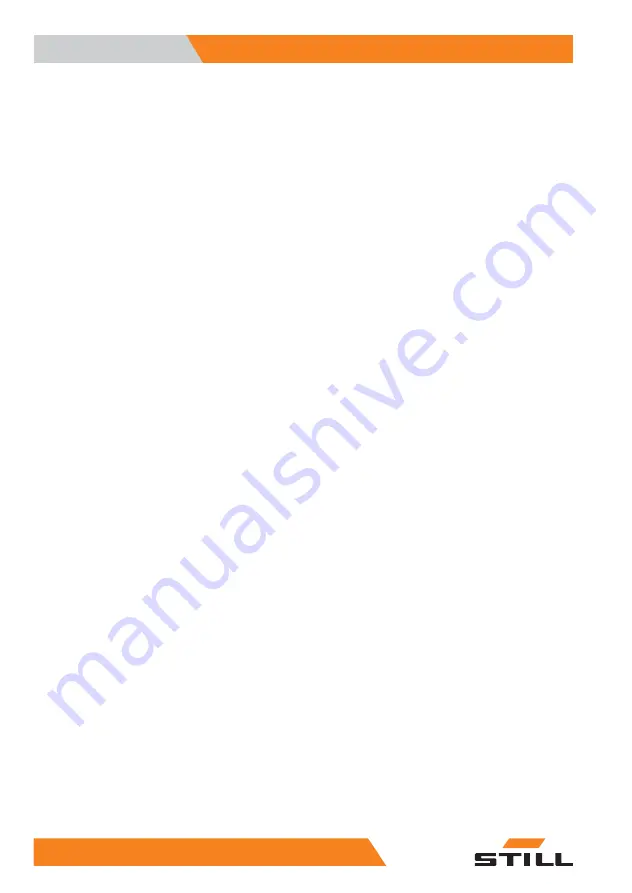
2
Safety
General safety information
General safety information
• People must stay away from the working
area (danger area) of the truck. If a person
does enter the danger area, all movements
of the truck must be stopped immediately
and the person must be directed away from
the area.
• The truck may only be operated from the
operator’s cab.
• When travelling without load, lower fork to
the floor level.
• When driving with a load, the load must be
lifted a few centimetres off the ground (clear
of the ground, max. 500 mm).
• The driver must keep all body parts within
the contours of the driver’s compartment.
The driver must refrain from sticking his
head out to gain a better view and from
reaching into the area of the moving lift
mast, because even doing this is highly
dangerous.
• Aside from the driver, there must be no other
person present on the truck, unless the
truck has additional equipment to enable
operation with two persons.
• If there are marked roadways, the truck is
to be moved only within these markings for
safety reasons.
• It is never permitted for anyone to stand
beneath a raised load or driver’s compart-
ment.
• Basically, it is the driver’s duty to adapt his
driving speed to the local conditions and
the respective situation. When cornering
in particular, attention must be paid to the
overall height and the centre of gravity,
which will be high as a result.
• The condition of the floor surface influences
the braking distance of the truck. The driver
must take account of this in his driving and
braking style.
10
5213 804 2501 EN - 01/2016
Summary of Contents for EK-X
Page 1: ...Original instructions High level order picker EK X 2131 2133 5213 804 2501 EN 01 2016 ...
Page 2: ......
Page 6: ......
Page 7: ...1 Foreword ...
Page 15: ...2 Safety ...
Page 30: ...2 Safety Personal protective equipment 24 5213 804 2501 EN 01 2016 ...
Page 31: ...3 Overview ...
Page 44: ...3 Overview Safety equipment 38 5213 804 2501 EN 01 2016 ...
Page 45: ...4 Operation ...
Page 86: ...4 Operation Emergency operation 80 5213 804 2501 EN 01 2016 ...
Page 87: ...5 Maintenance ...
Page 99: ...6 Technical data ...
Page 101: ...7 Special equipment ...
Page 119: ......