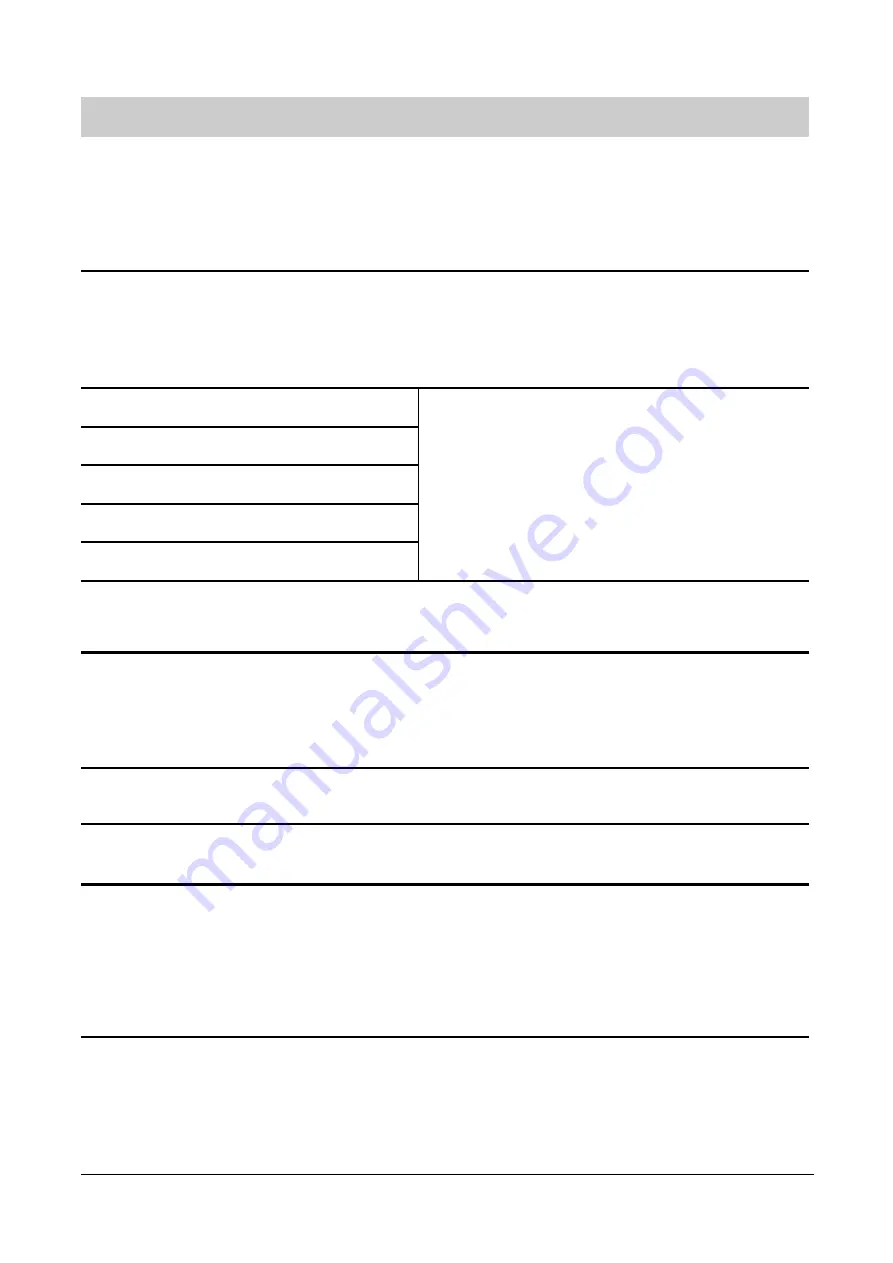
4. Clear Text Display Module & System Parameters
English
© STÖBER plc 1997
23
05.02.01
Parameter Function
Range
[Default]
Description / Notes
P078
••••
Continuous boost (%)
0 - 250
[100]
Operates continuously over the whole frequency range.
For many applications it is necessary to increase low frequency
torque. This parameter sets the start-up voltage at 0 Hz to adjust the
available torque for low frequency operation. 100% setting will
produce rated motor current at low frequencies.
WARNING:
If P078 is set too high, overheating of the motor
and/or an overcurrent trip (F002) can occur.
P079
••••
Starting boost (%)
0 - 250
[0]
For drives which require a high initial starting torque, it is possible to
set an additional current (added to the setting in P078) during
ramping. This is only effective during initial start up and until the
frequency setpoint is reached.
Note:
This increase is in addition to P078, but the total is limited to
250%.
P081
Nominal frequency for motor
(Hz)
0 - 120.00
[
]
P082
Nominal speed for motor (RPM)
0 - 9999
[
]
P083
Nominal current for motor (A)
0.1 - 99.9
[
]
‘These parameters are set in the factory and should not be changed
under normal circumstances.
P084
Nominal voltage for motor (V)
0 - 1000
[
]
P085
Nominal power for motor
(kW/hp)
0 - 100.0
[
]
P086
••••
Motor current limit (%)
0 - 250
[150]
The motor current can be limited with this parameter. If the set value
is exceeded, the output frequency is reduced until the current falls
below this limit. During this process, both LEDs will flash
(see section
3.6)
.
P087
Motor PTC enable
0 - 1
[0]
Change this parameter only when the PTC option is fitted.
0
= Disabled
1
= Motor PTC enabled
Note:
If P087 = 1 and the PTC input goes high then the inverter will
trip (fault code F004). Note that if the internal PTC gets too
hot, the inverter will trip (fault code F005).
P089
••••
Stator resistance (
Ω
)
0.01-
100.00
[
]
Set in the factory.
Do not adjust!
P091
••••
Serial link slave address
0 - 30
[0]
Up to 31
CombiDrive
®
can be connected via the serial link and
controlled by a computer or PLC using the USS protocol. This
parameter sets a unique address for the inverter.
P092
••••
Serial link baud rate
3 - 7
[6]
Sets the baud rate of the RS485 serial interface (USS protocol):
3
= 1200 baud
4
= 2400 baud
5
= 4800 baud
6
= 9600 baud
7
= 19200 baud
Note:
Some RS232 to RS485 converters are not capable of
baud rates higher than 4800.
Summary of Contents for CombiDrive
Page 39: ......