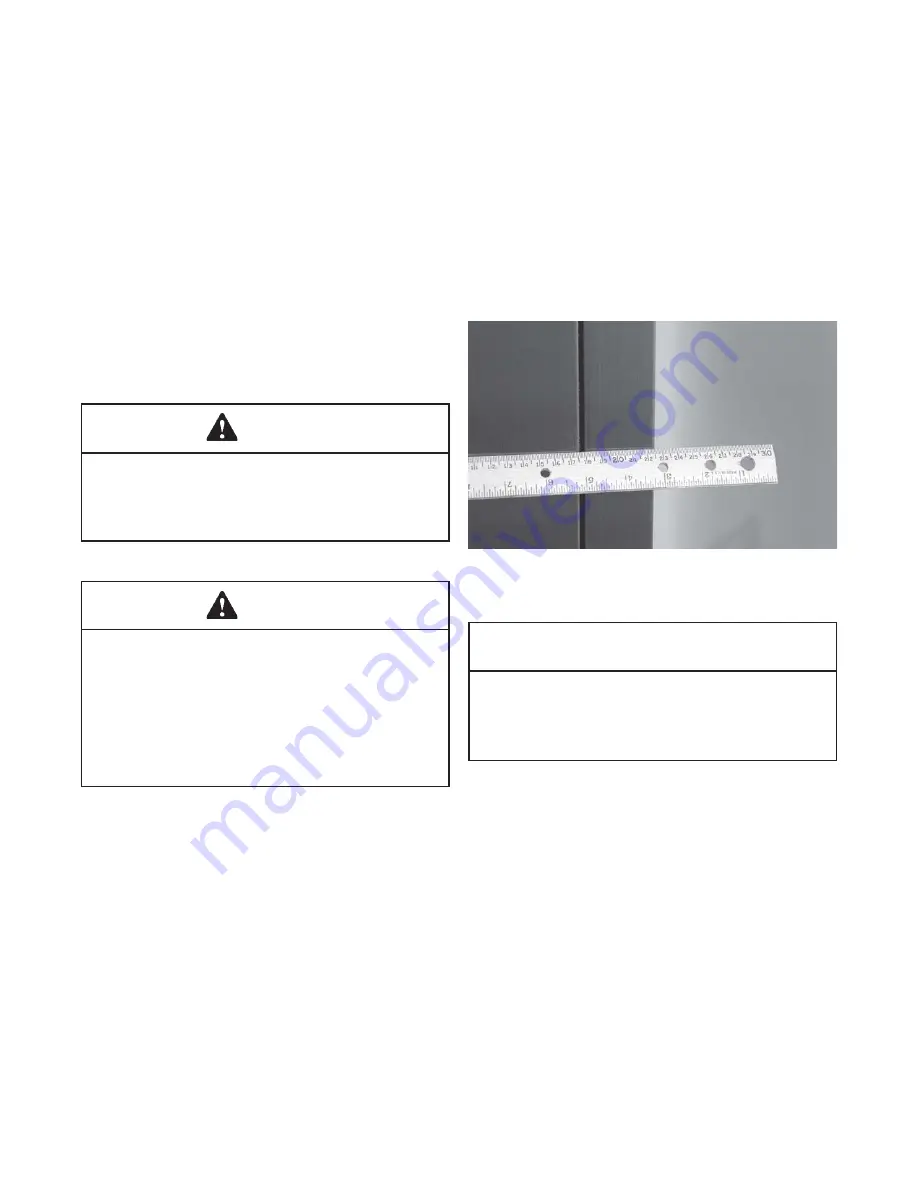
4
2.2 SHIPMENT AND TRANSIT
The freezer has been assembled, operated and inspected
at the factory. Upon arrival at the final destination, the
complete freezer must be checked for any damage which
may have occurred during transit.
With the method of packaging used, the freezer should
arrive in excellent condition. THE CARRIER IS RESPON-
SIBLE FOR ALL DAMAGE IN TRANSIT, WHETHER
VISIBLE OR CONCEALED.
Do not
pay the freight bill until
the freezer has been checked for damage. Have the carrier
note any visible damage on the freight bill. If concealed
damage and/or shortage is found later, advise the carrier
within 10 days and request inspection. The customer must
place claim for damages and/or shortages in shipment
with the carrier.
Stoelting, LLC. cannot make any
claims against the carrier.
2.3 FREEZER INSTALLATION
WARNING
Installation must be performed by a qualified electri-
cian/refrigeration specialist. Incorrect installation may
cause personal injury, severe damage to the machine
and will void factory warranties.
WARNING
Lifting hazard
Do not attempt to lift freezer manually. Use proper lift-
ing equipment such as a forklift, lift table, or pallet
jack, with lifting device positioned beneath the freezer’s
base. Ensure that personnel remain clear of suspended
load. Failure to do so may result in personal injury
and/or damage to the freezer that will void any factory
warranties.
Installation of the freezer involves moving the freezer close
to its permanent location, removing all crating, setting in
place, assembling parts, and cleaning.
A.
Uncrate the freezer.
B.
Accurate leveling is necessary for correct drainage of
freezer barrel and to insure correct overrun. Place a
spirit level on top of the freezer at each corner to
check for level condition. If adjustment is necessary,
level the freezer by turning the bottom part of each leg
in or out. Then separate freezer base gasket and
install with seam to the back and angle to the top.
Figure 3. Space and Ventilation Requirements
CAUTION
Risk of product damage
Air cooled condenser requires proper ventilation. Fail-
ure to provide adequate ventilation will void factory
warranties.
C. The freezer is equipped with an air cooled condenser
and requires correct ventilation. The front of the
freezer is the air intake and the back discharge. Both
front and back must have a minimum of 3" of
clearance. (6" in high ambient temperature conditions)
(Fig. 3).
D. Place the OFF-ON switch in the OFF position.