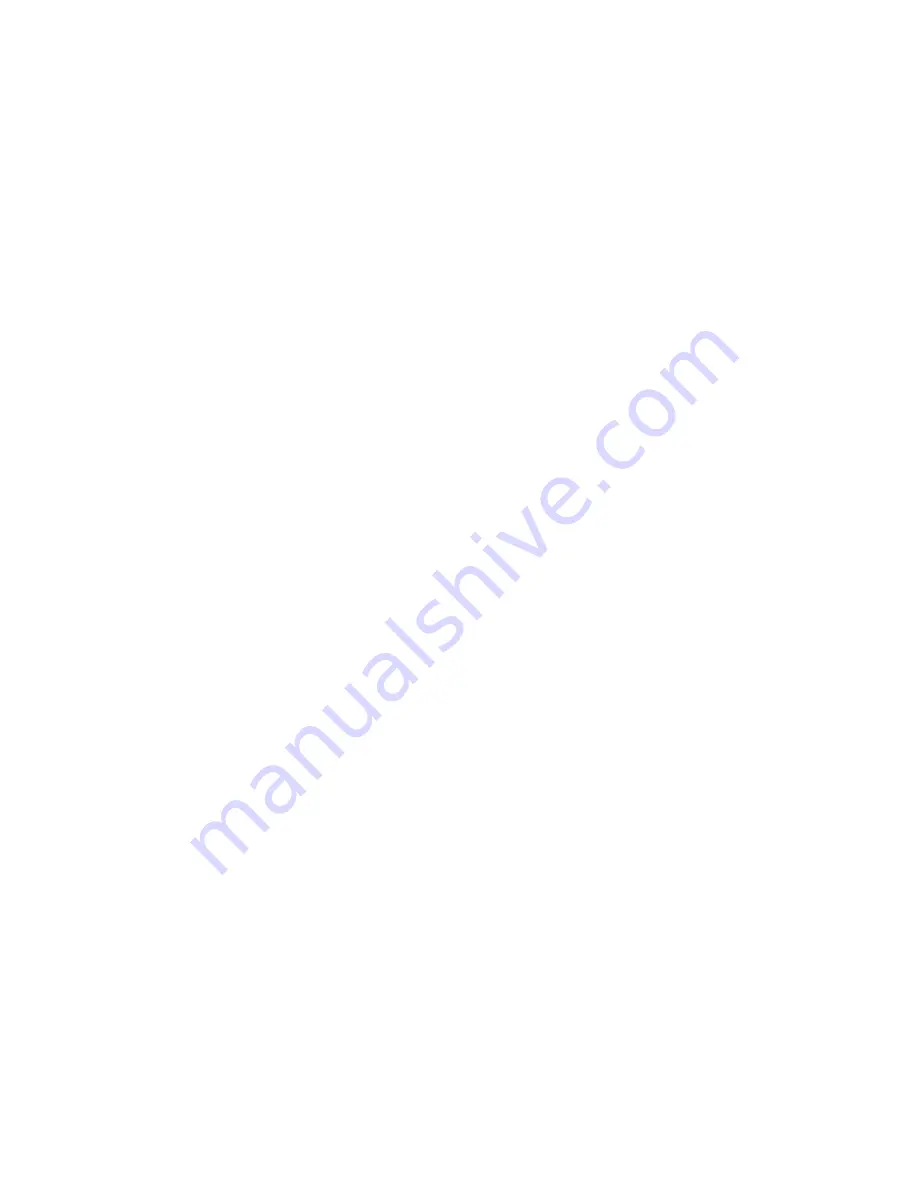
19
RUN STATISTICS
In addition to dynamic readings and recorded
error code details, the IntelliTec control records
rolling averages of run statistics. Following are the
readings available under the RUNSTATS menu:
On Times (sec)
The control records the time of each freezing
cycle and provides a rolling average.
Off Times (sec)
The control records the time between freezing
cycles and provides a rolling average.
Brl. Min (°F)
The lowest average barrel temperature is
recorded.
Brl. Max (°F)
The highest average barrel temperature is
recorded.
Stor Min (°F)
The lowest average cabinet temperature is
recorded.
Stor Max (°F)
The highest average cabinet temperature is
recorded.
Power On (hrs)
This value is a record of the time the machine
has been in service. If power is interrupted, the
timer will reset.
4.6
ADJUSTMENTS (SERVICE PERSONNEL
ONLY)
The following adjustments directly affect product consis-
tency and length of time in “Serve Mode”. The default
settings have been created using a 5% milkfat soft serve
mix and provide optimal product consistency while pro-
longing product life.
CutOut (amps)
It is recommended to set the CutOut value at
initial startup and when changing mix types.
Adjustments to this setting directly affect the length
of the freezing cycle and indirectly change product
consistency. To properly set the CutOut value,
during startup navigate to the “°F” and “amps”
values under the Display menu (Refer to Section
4.4), start the machine and freeze the product to
the desired consistency. Monitor consistency by
taking a 6 ounce sample at each change of the
“amps” display. When the desired consistency has
been reached, record the temperature and amps,
and change the CutOut value to the recorded
amps value.
Cut In T (°F)
After the consistency value has been determined,
the Cut In T value can be adjusted. The Cut In
T is the temperature of the refrigerant gas in the
evaporator at the front of the freezing cylinder.
Changing this setting changes the temperature at
which the freezing cycle starts. This value along
with the CutOut value determines the range of
temperatures (or “temperature window”) of the
product. Decreasing the temperature decreases
the temperature window and, under normal use,
increases the amount of freezing cycles. This
creates a greater chance of product breakdown
by stirring the product often. Increasing the Cut
In T increases the temperature window, which
decreases freezing cycles and increases the
chance of heat shock within the product.
Cycles (count)
This setting determines the number of freezing
cycles during “Serve Mode”. Increasing the value
will increase the total time in “Serve Mode”. Factory
default is 20 cycles, which results in “Serve Mode”
lasting about 2-1/2 hours without the PUSH TO
FREEZE button being pressed or a spigot handle
being pulled. If the PUSH TO FREEZE button is
pressed or the spigot handle is pulled at any time
during “Serve Mode”, the Cycles count will reset.
4.7
OTHER SETTINGS (SERVICE
PERSONNEL ONLY)
Changing any setting on the IntelliTec control will alter
machine operation and affect the product temperature,
consistency, or life. Refer to the IntelliTec Control System
Settings sheet located in the information pouch behind
the header panel of the machine. If any of the following
settings on the IntelliTec control differ from the System
Settings sheet, it is recommended to return those settings
to factory defaults.
Stir On (sec)
Adjustments to this setting affect the amount of
time the auger rotates in the stir cycle. The stir
cycle occurs in “Serve Mode”, “Standby Mode”,
and “Sleep 2 Mode”.
Stir Off (sec)
Adjustments to this setting affect the time between
stir cycles. The stir cycle occurs in “Serve Mode”,
“Standby Mode”, and “Sleep 2 Mode”.
On Time (sec)
Increasing this value will increase the length of the
freezing cycle during “Standby Mode” and result
in a decrease of average product temperature in
the barrel.