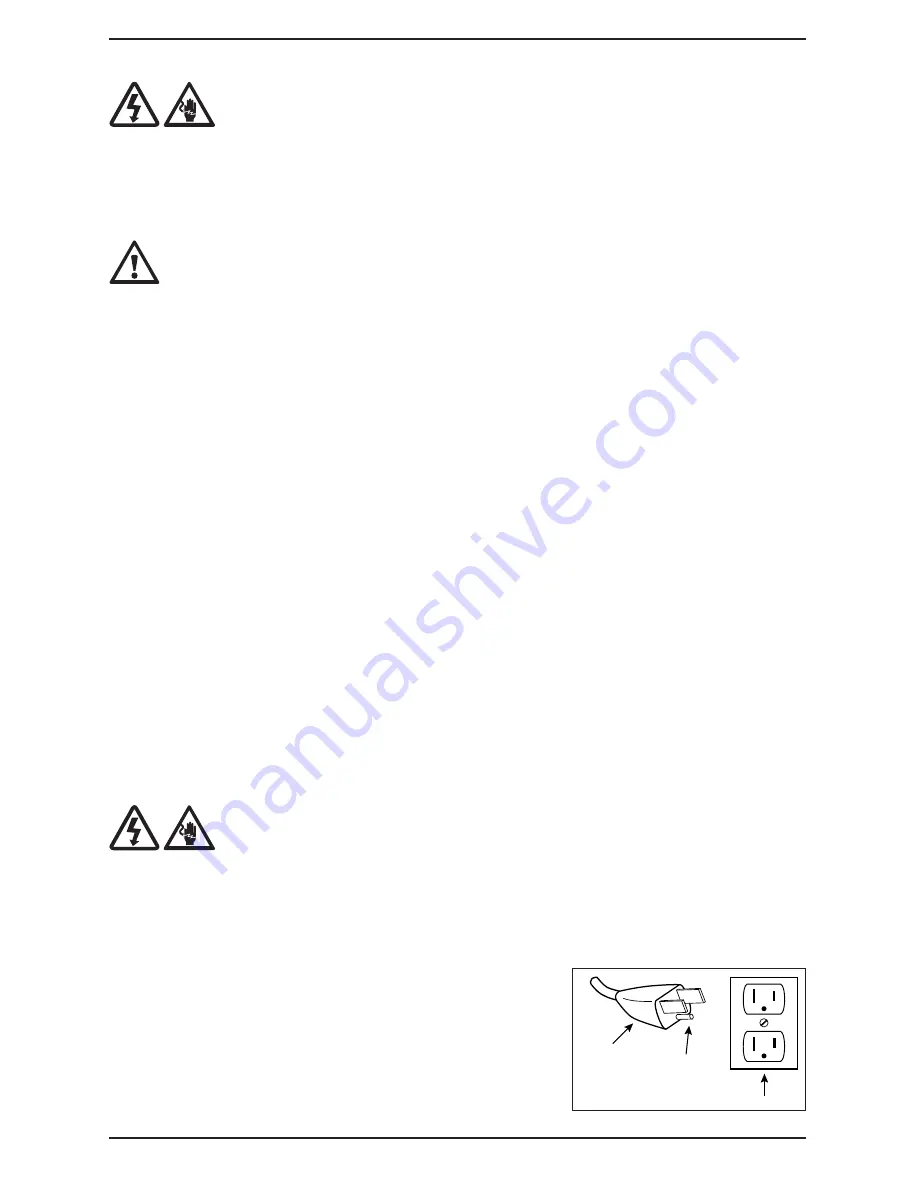
2
INSTALLATION:
WARNING! Electrical Shock Hazard. Disconnect electrical power at the
circuit breaker or fuse box before installing this product. Install this product
where it will not come into contact with water or other liquids. Install this product where it
will be weather protected. Electrically ground this product. Failure to follow these instruc-
tions can result in death, fire or electrical shock.
Correct installation is the responsibility of installer. Make sure of proper installation condi-
tions and that clearances do not block air flow.
WARNING! Blocking air flow over the product in any way can cause product to
overheat.
MOUNTING:
Compressor may be installed in any orientation. Mounting the product to a stable, rigid
operating surface and using shock mounts will reduce noise and vibration.
PLUMBING:
Remove plugs from the IN and OUT ports. Connect with pipe and fittings that are the
same size or larger than threaded ports. Be sure to connect the intake and exhaust
plumbing to the correct inlet and outlet ports. Ports will not support plumbing.
ACCESSORIES:
The compressor’s external intake will provide adequate filtration in most applications.
Check filters periodically and replace when necessary. Install relief valves and gauges at
inlet, outlet or both, to monitor performance. Check valves may be required to prevent
back flow through pump.
MOTOR CONTROL:
It is your responsibility to contact a qualified electrician and assure that the electri-
cal installation is adequate and in conformance with all national and local codes/
ordinances. The metal capacitor must be grounded.
The wiring diagram supplied with the compressor provides required electrical information.
Check that power source is correct to properly operate the dual-voltage motors.
ELECTRICAL:
WARNING! Electrical Shock Hazard. This product must be properly
grounded. Do not modify the plug provided. If it will not fit the outlet, have
the proper outlet installed by a qualified electrician. If repair or replacement of the cord or
plug is necessary, do not connect the grounding wire to either flat blade terminal. Check
the condition of the power supply wiring. Do not permanently connect this product to
wiring that is not in good condition or is inadequate for the requirements of this product.
Failure to follow these instructions can result in death, fire or electrical shock.
Model with a power supply cord: This product must
be grounded. For either 120 volt or 220/240 volt circuits
connect power supply cord grounding plug to a matching
grounded outlet. Do not use adapter. See diagram at right.
In the event of an electrical short circuit, grounding re-
duces the risk of electric shock by providing an escape
wire for the electric current. This compressor may be
Grounded Plug
Grounding Pin
Grounded Outlet
120-volt grounded connectors
shown. 220/240-volt grounded
connectors will differ in shape.