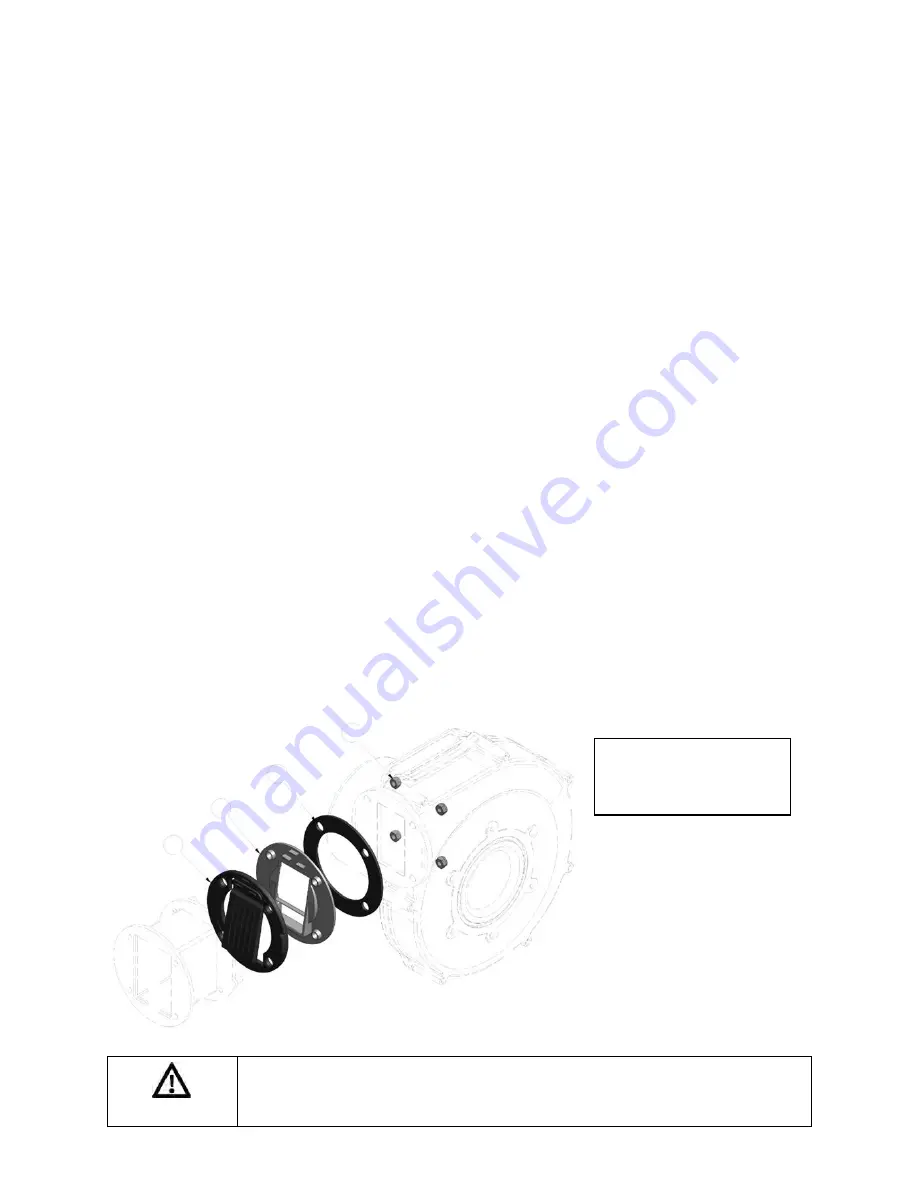
114
Water leakage
The water pressure of the heating installation should be more than 1.0 bar (21 psi) and at a maximum of 6.0 bar
(87 psi) in normal operation. When the water pressure drops below the minimum occasionally, there might be a
water leak. Check the boiler and the complete heating installation for any water leakages and have these repaired.
higher water pressures are allowed with the use of a different relief valve and a pressure switch kit
Flue gas & air supply
The flue gas pipes and the air supply pipes must be checked for gas tightness. Also check if the mounting of these
pipes is correct, safe and not damaged. Check the top side of the boiler housing for signs of water leakage and
traces of water coming from the air supply pipe, the air vent or any condensate coming from the flue gas pipes.
Check to ensure the flow there are no obstructions for the exhaust venting or the intake combustion air venting.
Check that all intake and exhaust venting has been properly reassemble and sealed before leaving the job site
Gas supply & safeties
The gas pipes must be checked for gas tightness. Also check if the mounting of these pipes is correct, safe and
not damaged. Any built-in safeties should be checked for a correct functioning. Any gas pipe or fitting that have
been opened or adjusted should be checked for leaks.
Remove complete burner unit
The complete boiler unit consists of the fan, venturi, gas valve, the burner plate and the internal burner. To make
more space to dismantle the complete burner unit pull down the burner controller unit.
To remove this part for an internal heat exchanger check: remove the six M6 nuts, the ignition cable and the
thermal fuse cables. Close the gas tap under the boiler and loosen the gas coupling by untighten the swivel joint
under the gas valve. Remove the air intake pipe from the venturi.
After this, take out the complete burner unit by moving it forward out of the boiler housing. NOTICE: Watch out not
to damage the burner plate insulation during this operation.
While removing the complete burner unplug both of the electrical and controlling cables of the fan. After all this
dismantle the venturi on the suction side of the fan and check the blade wheel of the fan.
Checking Non-return Valve (NRV)
The non-return valve is placed directly after the fan and has to be replaced every year during maintenance.
Replace the non-return valve by removing the 4 nuts that are holding the fan. All the parts included in the NRV
maintenance kit must be replaced the gaskets, NRV seat, lock nuts, and non-return valve, do not reuse any of
the old parts.
Reassemble the Non-return valve to the burner unit be sure that the nuts are tightened again so no air/gas mixture
is leaking into the cabinet. Check during start-up of the boiler to ensure no gas mixture is leaking on these gaskets
near the non-return valve.
Replace parts 1 to 4 of the check valve once a year.
Needed tools: Wrench 55 (pipe wrench), 10 and 8 mm, Hex key 5 mm
Always check gaskets on non-return valve for air/gas leakage!!
4
2
1
3
1 = Seat check valve small
2 = Lock nut M5 Din985
3 = Gasket gas air mixing
4 = Check valve small
WARNING
Summary of Contents for S-CBX 105
Page 2: ......
Page 40: ...40 9 10 Flue Terminal Positioning ...
Page 42: ...42 9 11 1 FIGURE 12 LINE G ...
Page 55: ...55 11 5 Ladder Logic Diagram ...
Page 56: ...56 11 6 Electrical schematics ...
Page 57: ...57 ...
Page 137: ......