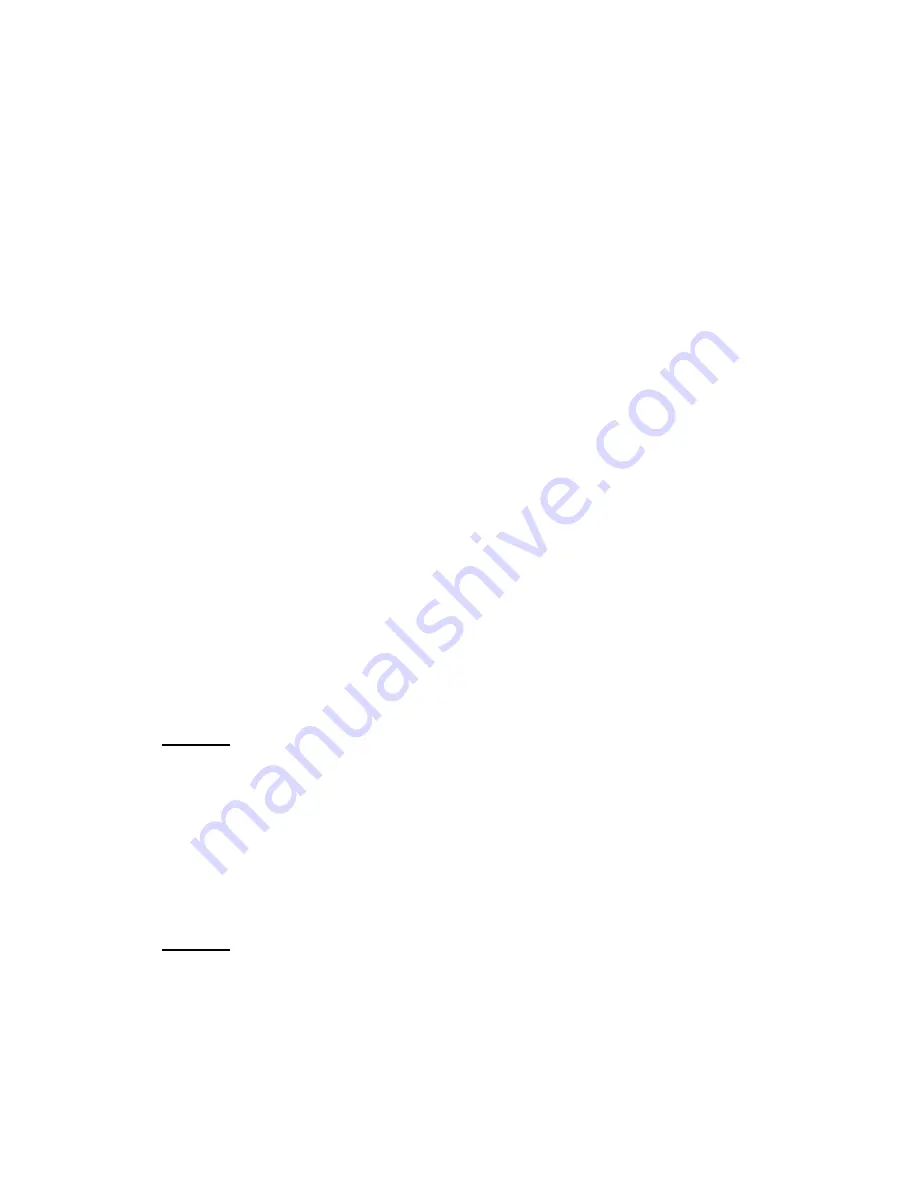
6
Attach all the sections of hose that will be used in the day’s operation together just as they
will be used.
Pump water into the hose until it begins to discharge. Stop the pump and cap the discharge
end securely with a quick coupler cap to fit hose size to be used.
After advising all personnel to stand clear of the hose, operate the pump. Starting in manual
and low for initial break over then up to medium. Allow the hose to pressurize for 30
seconds.
Reverse the pump until 0 PSI pressure indicates on the gauge or the discharge hose becomes
soft.
Remove the cap. Operate the pump until the water has been discharged and then proceed
with the pumping of the slurry.
This field test should be repeated if any damage or accident befalls a section of the hose or if,
for any reason, a section is suspect.
All replacement material hose and fittings should be rated for no less than 600 psi. Such
hoses can be obtained from Strong Manufacturing Company.
Do not use other hoses unless specifically advised by the Strong Manufacturing Company.
Caution:
ALL HOSES SHOULD BE FITTED WITH “FULL FLOW”
CONNECTIONS. Connectors, which reduce the hose i.d., will cause increased pressures
and reduced flows. A material gauge registers pressure at the end of the rotor stator. A
sudden rise in pressure indicates a blockage is about to occur and alerts the operator to
stop pumping, reverse pump and remove blockage. While pumping material the rotor-
stator pump can develop higher pressure than it does while pumping just water. Failure
to stop the pump could cause the hose to rupture or uncouple possibly striking someone
causing severe bodily injury such as cuts, bruises, broken limbs or possibly death.
Caution:
NEVER USE WEATHERED, ROTTEN, DAMAGED HOSES OR HOSES
WITH DAMAGED FITTINGS IN CONJUNCTION WITH PUMPING OPERATIONS.
They represent a hazard to operators, bystanders, and persons handling the hoses. If a
hose or a fitting should burst under pressure, persons could be injured.