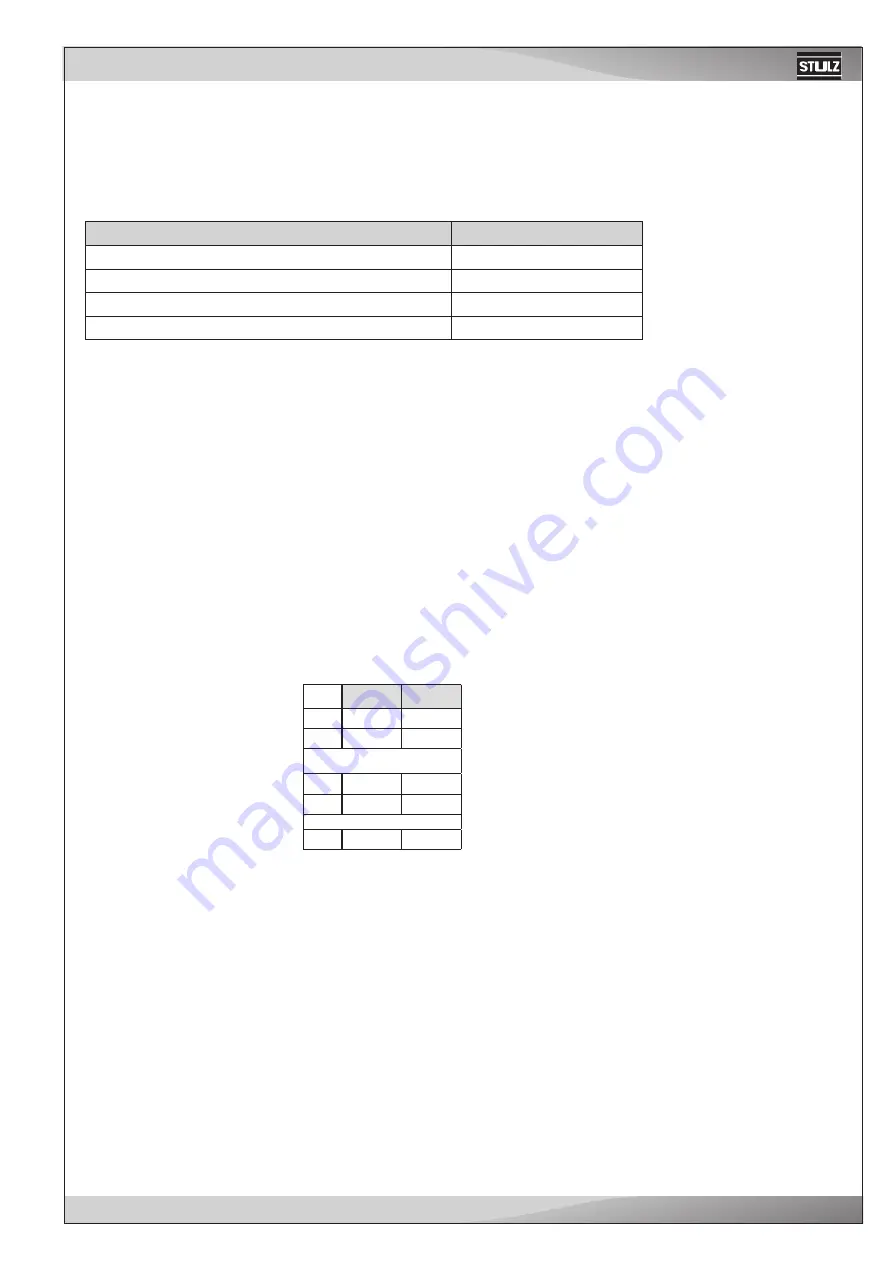
/11.2015/
G17D
11
R134a R410A
bar
0,5
3,0
bar
1,5
6,0
bar
24,5
36,0
bar
18,0
29,0
bar
28
40
EN
Adjustment of the pressure switches:
LP switch:
releases at:
automatic reset at:
HP switch:
releases at:
manual reset possible at:
Safety valve:
Design conditions for A/C units:
Electrical connection:
Return air conditions for evaporator capacity:
with an external static pressure:
400V/3ph/50Hz
33°C, 30% rel. h.
20 Pa
Cooling fluid circuit
GE, GES
Cooling fluid
water, 30% ethylen glycol
Fluid temperature inlet/outlet (summer operation)
34°C/40°C
Water temperature inlet (winter operation)
11°C
Condensation temperature
45°C
The sound pressure levels are valid at a height of 1m and distance of 2m in front of the unit under free field condi-
tions and with nominal data. The values take into account the effects of all installation and design parts contained
in the standard unit.