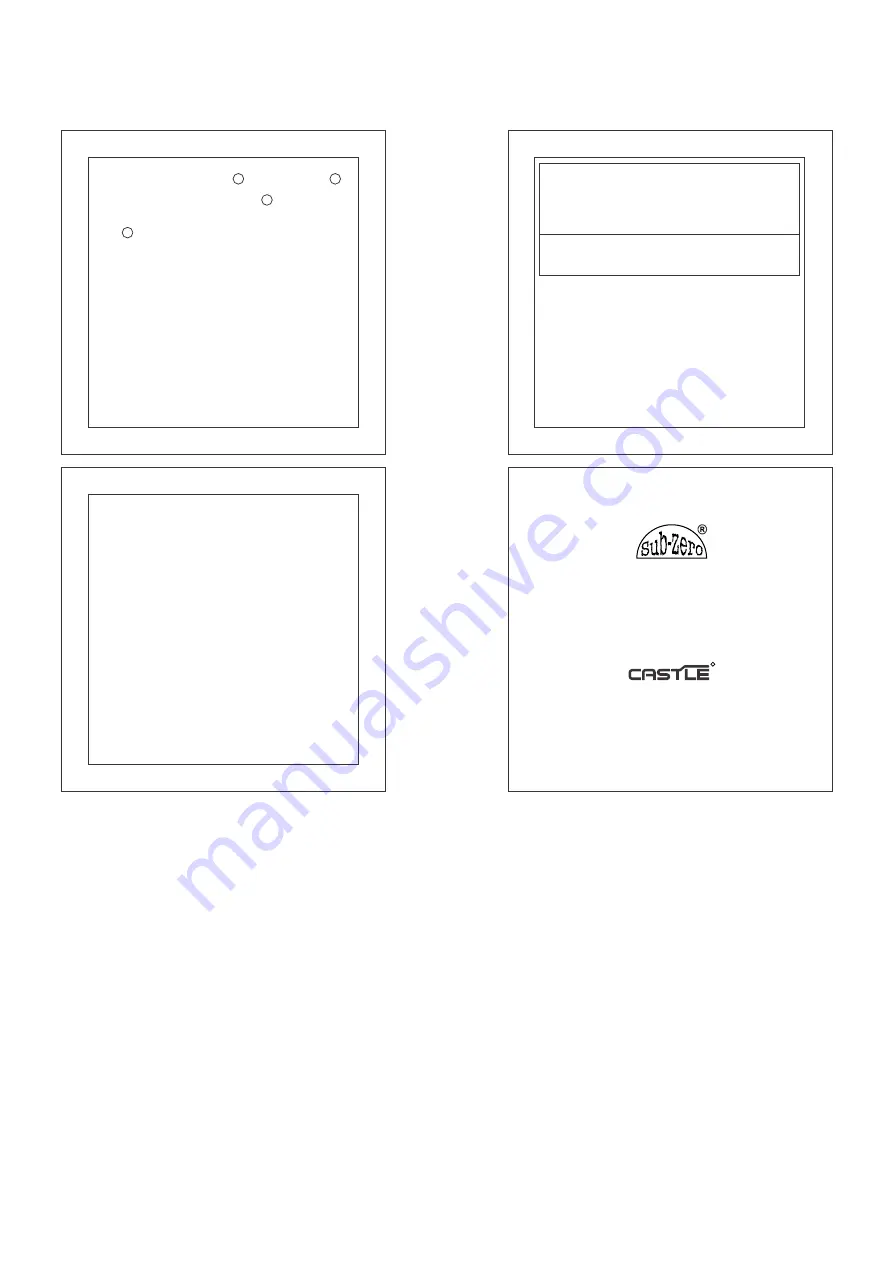
24
Disclaimer:
This manual & its contents remain the sole property
of PVR CONTROLS, India and shall not be reproduced or
distributed without authorization. Although great care has been
taken in the preparation of this document, the company or its
vendors in no event will be liable for direct, indirect, special,
incidental or consequential damage arising out of the use or
inability to use the product or documentation, even if advised of the
possibility of such damages. No part of this manual may be
reproduced or transmitted in any form or by any means without the
prior written permission of the company.
,
reserves the right to make and changes or improvements without
prior notice.
PVR CONTROLS
Warranty:
This product is warranted against defects in
materials and workmanship for a period of one year from
the date of purchase. During the warranty period, product
determined by us to be defective in form or function will be
repaired or, at our option, replaced at no charge. This
warranty does not apply if the product has been damaged
by accident, abuse, and misuse or as a result of service or
modification other than by the company. This warranty is in
lieu of any other warranty expressed or implied. In no event
shall the company be held liable for incidental or
consequential damages, including lost revenue or lost
business opportunity arising from the purchase of this
product..
23
CAUTION
WIRING:
The probe and its corresponding wires should
never
be installed in a conduit next to control or power
supply lines.
The electrical wiring should be done as shown in the diagram.
The power supply circuit should be connected to a protection
switch. The terminals admit wires of upto 2.5sq mm.
WARNING:
Improper wiring may cause irreparable damage
and personal injury. Kindly ensure that wiring
is done by qualified personnel only.
Maintenance:
Cleaning: Clean the surface of the controller
with a soft moist cloth. Do not use abrasive detergents, petrol,
alcohol or solvents.
Notice:
The information in this document is
subject
to
change in order to improve reliability , design or function
without prior notice and does not represent
a commitment
on the part of the company. In no
event will the company
be liable for direct, indirect, special, incidental or
consequential damage arising out of the use or inability to
use the product or documentation, even if advised of the
possibility of such damages. No part of this manual may
be reproduced or transmitted in any form or by any means
without the prior written permission of the company.
INDIA
Ball Valves
Globe Valves
Hand Valves
Flow Switches
Solenoid Valves
OUR OTHER PRODUCTS
Cold Room Controller
Chiller Controller
Two Compressors Controller
Heating Controller
Humidity Controller
Pressure Controller
R
03 / 12.06.17
Installation :
Fixing and dimensions of panel models:
To fix the unit, slide the fastener 1 through the guides 2
as per the position shown in the figure. Move the fastener in
the direction of the arrow, pressing tab 3 it permits to move
the fastener in the opposite direction of the arrow. Once the
controller has been connected, they should be covered with
the lid 4 Silicon sealant should be applied along the
perimeter of the panel cut out or a rubber ‘O’ ring supplied
before the unit is fitted to increase protection against water
seepage.
Controller
:Controller should be installed in a place
protected by vibration, water and corrosive gasses and
where ambient temperature does not exceed the
values specified in the technical data.
Probe :
To give a correct reading, the probe must be
installed in a place protected from thermal influences,
which may affect the temperature to be controlled.