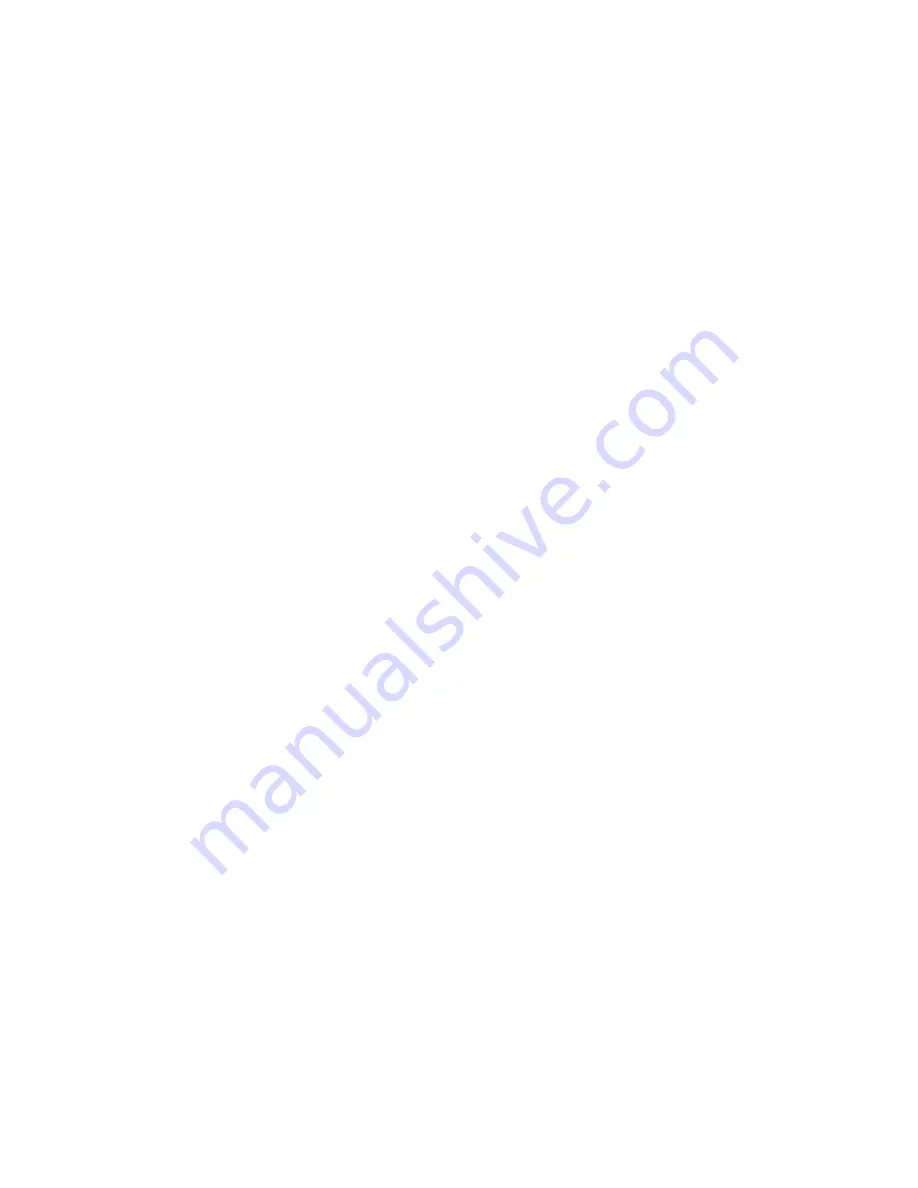
TABLE OF CONTENTS
Section 1
PAGE
SAFETY
1
1.1 GENERAL
1
1.2 PERSONAL PROTECTIVE EQUIPMENT
1
1.3 PRESSURE RELEASE
1
1.4 FIRE AND EXPLOSION
2
1.5 MOVING PARTS
2
1.6 HOT SURFACES, SHARP EDGES AND SHARP CORNERS
2
1.7 TOXIC AND IRRITATING SUBSTANCES
3
1.8 ELECTRICAL SHOCK
3
1.9 LIFTING
4
1.10 ENTRAPMENT
Section 2
DESCRIPTION
5
2.1 INTRODUCTION
5
2.2 DESCRIPTION OF COMPONENTS
5
2.3 SULLAIR COMPRESSOR UNIT,
FUNCTIONAL DESCRIPTION
6
2.4 COMPRESSOR COOLING AND LUBRICATION
SYSTEM, FUNCTIONAL DESCRIPTION
9
2.5 COMPRESSOR DISCHARGE SYSTEM,
FUNCTIONAL DESCRIPTION
9
2.6 CONTROL SYSTEM, FUNCTIONAL DESCRIPTION
11
2.7 AIR INLET SYSTEM, FUNCTIONAL DESCRIPTION
11
2.8 INSTRUMENT PANEL GROUP, FUNCTIONAL
DESCRIPTION
Section 3
SPECIFICATIONS
13
SULLAIR SERIES 10B SPECIFICATIONS
14
LUBRICATION GUIDE--- STANDARD COMPRESSORS
14
LUBRICATION GUIDE--- 24KT COMPRESSORS
15
APPLICATION GUIDE
Section 4
INSTALLATION
17
4.1 MOUNTING OF COMPRESSOR
17
4.2 VENTILATION AND COOLING
17
4.3 SERVICE AIR PIPING
17
4.4 COUPLING ALIGNMENT CHECK
17
4.5 FLUID LEVEL CHECK
19
4.6 MOTOR ROTATION DIRECTION CHECK
19
4.7 ELECTRICAL PREPARATION
Summary of Contents for 10B 25HP
Page 2: ...NOTE For Additional Information on 24KT Units See Inside Back Cover...
Page 4: ...NOTES...
Page 22: ...16 NOTES...
Page 24: ...Section 4 INSTALLATION 18 Figure 4 1 Piping and Instruments...
Page 26: ...20 NOTES...
Page 42: ...36 NOTES...
Page 44: ...NOTES...
Page 45: ......