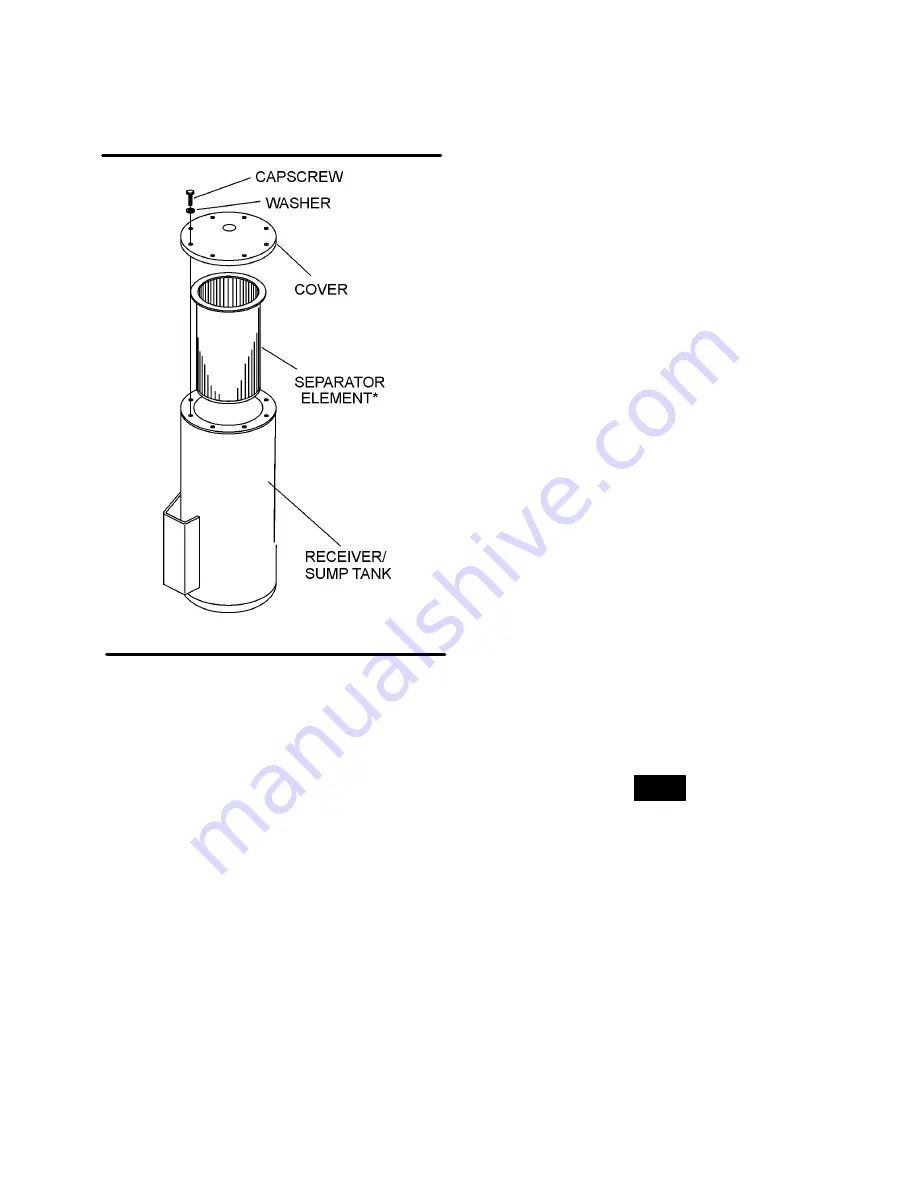
Section 5
MAINTENANCE
29
Figure 5---3 Air/Fluid Separator
*Replacement Separator Kit P/N 02250078---031
shine through the element and disclose any
holes.
2. Inspect all gaskets and gasket contact surfaces
of the housing. Should faulty gaskets be evident,
correct the condition immediately.
3. If the clean element is to be stored for later use, it
must be stored in a clean container.
4. After the element has been installed, inspect and
tighten all air inlet connections prior to resuming
operation.
SEPARATOR ELEMENT REPLACEMENT
Refer to Figure
. When fluid carry over is evident
after the fluid return line strainer and orifice as well
as the blowdown valve seal has been inspected and
found to be in satisfactory condition, separator ele-
ment replacement is necessary. Use separator ele-
ment part number no. 250034---112 and follow the
procedure explained below.
1. Remove all piping connected to the sump cover
to allow removal (return line, service line, etc.).
2. Remove the fluid return line from the fitting in the
cover.
3. Remove the eight (8) cover bolts and washers
and lift the cover from the sump.
4. Remove the separator element.
5. Scrape the old gasket material from the cover and
the flange on the sump. Be sure to keep all
scrapings from falling inside tank.
6. Install the new element.
7. Replace the sump cover and bolts. Run the cover
bolts in finger tight, then gradually tighten in a
crisscross pattern in 4 to 5 steps. Always tighten
the bolts alternately at opposite sides of the
cover. Never tighten bolts adjacent to each other.
Torque bolts to 60 ft.---lbs. (81 Nm).
8. Reconnect all piping. The fluid return line tube
should extend to the bottom of the separator ele-
ment. This will assure the proper fluid return flow.
9. Clean the fluid return line strainer and clear the
orifice prior to restarting the compressor.
10. After 24 hours of operation, tighten sump cover
bolt to torque specification listed in step number
7.
PROCEDURE FOR SETTING SPEED AND
PRESSURE CONTROLS ON PORTABLE COM-
PRESSORS WITH POPPET VALVE
Refer to Figure
. Prior to adjusting the Control
System, it is necessary to determine the rated full
load pressure and the high/low RPM settings for
your particular compressor. This information can be
obtained from the Operator’s Manual (Specifica-
tions Section) or by contacting your local authorized
Sullair Representative. The following explanation
applies to a compressor with 100 psig (6.9 bar)
rated full load pressure.
1. Start the compressor and allow the engine to
warm---up to normal operating temperature with
the service valve closed.
2. With the service valve closed, set the engine low
speed (idle) to its specified setting with the idle
stop screw on the engine injector pump.
NOTE
Operation at speeds below the minimum idle
speeds shown in Section 3 under Specifications
will damage the compressor. Extended operation
below those speeds will induce coupling and/or
compressor failures.
3. Adjust the pressure regulator so that the com-
pressor maintains 115 psig (8 bar).
4. Gradually open the service valve to atmosphere
until the engine comes up in speed and sump
pressure is held at 100 psig (6.9 bar). At this
point, set the engine high speed to its specified
setting by adjusting the high idle threaded rod lo-
cated on the engine speed control (where appli-
cable). To raise or lower the speed, lengthen or
shorten the rod respectively.
5. Open the service valve to 100 psig (6.9 bar) (rated
full load pressure) and recheck top engine
speed and control response. Close the service
Summary of Contents for 185H
Page 6: ......
Page 14: ...8 NOTES...
Page 20: ...Section 2 DESCRIPTION 14 Figure 2 4B Control System with Piping and Instrumentation 260 Models...
Page 23: ...Section 2 DESCRIPTION 17 Figure 2 6 Instrument Panel Group...
Page 24: ...Section 2 DESCRIPTION 18 Figure 2 7 Electrical System JOHN DEERE 02250144 446R05...
Page 25: ...Section 2 DESCRIPTION 19 Figure 2 7A Electrical System CATERPILLAR P02250144 395R04...
Page 26: ...20 NOTES...
Page 30: ...24 NOTES...
Page 36: ...Section 5 MAINTENANCE 30 Figure 5 4 Control System Adjustment 185H 210 MODELS 260 MODELS...
Page 42: ...36 NOTES...
Page 49: ...Section 7 ILLUSTRATIONS AND PARTS LIST 43 NOTES...
Page 90: ...Section 7 ILLUSTRATIONS AND PARTS LIST 84 7 10 ELECTRICAL PARTS ALL MODELS 02250148 897R00...
Page 128: ...Section 7 ILLUSTRATIONS AND PARTS LIST 122 7 20 DECALS...
Page 130: ...Section 7 ILLUSTRATIONS AND PARTS LIST 124 7 20 DECALS...
Page 132: ...Section 7 ILLUSTRATIONS AND PARTS LIST 126 7 20 DECALS...
Page 134: ...Section 7 ILLUSTRATIONS AND PARTS LIST 128 7 20 DECALS...
Page 136: ...Section 7 ILLUSTRATIONS AND PARTS LIST 130 7 20 DECALS...
Page 138: ...Section 7 ILLUSTRATIONS AND PARTS LIST 132 7 21 DECAL LOCATIONS 02250149 633R01...
Page 142: ......
Page 143: ......