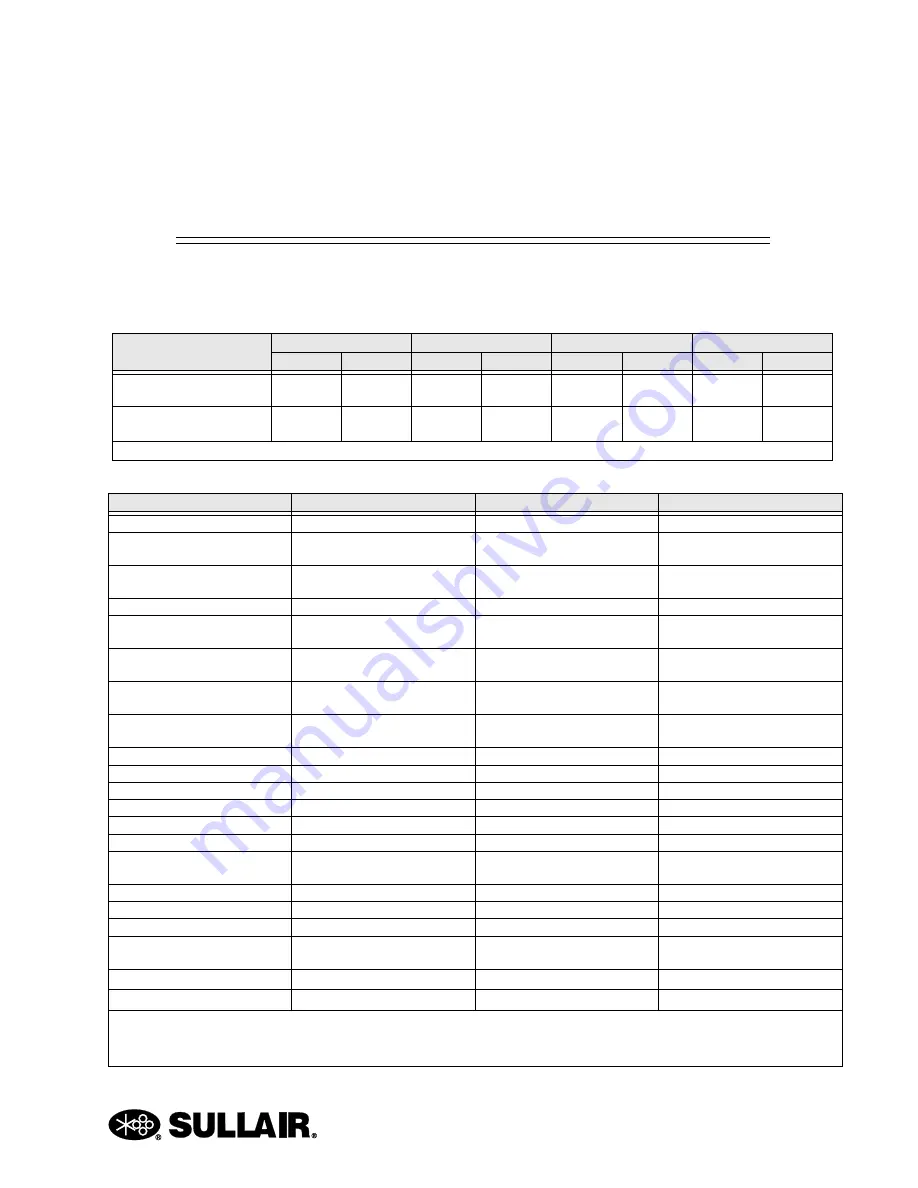
Section 3
300HH, 375, 375H, 375HH, 425 AND 425H USER MANUAL R00
53
SPECIFICATIONS
3.1
SPECIFICATIONS—300HH, 375, 375H JOHN DEERE
Table 3-1: Overall Specifications
Model Series
Length (I)
Width
Height (II)
Weight (wet)
in
mm
in
mm
in
mm
lb
kg
300HH, 375, 375H
2-Wheel (III)
156.2
3967.5
77.2
1960.9
74.0
1879.6
4440*
2014.0*
300HH, 375, 375H
Less Running Gear
98.8
2509.5
59.3
1506.2
63.6
1615.4
4195*
1902.9*
(l) Length over drawbar for 2-wheel version, (III) American models. *Add 115 lbs (52 kg) for Aftercooled Version
Table 3-2: Compressor Specifications
Compressor
300HH
375
375H
Type
Rotary Screw
Rotary Screw
Rotary Screw
Maximum Operating
Pressure
200 psig (13.8 bar)
125 psig (8.6 bar)
150 psig (10.3 bar)
Pressure Delivery
300 Free CFM
(142 L/S)
375 Free CFM
(177 L/S)
375 Free CFM
(177 L/S)
Rated Pressure
200 psig (13.8 bar)
100 psig (6.9 bar)
150 psig (10.3 bar)
Cooling
Pressurized Compressor
Fluid
Pressurized Compressor
Fluid
Pressurized Compressor
Fluid
Lubricating Compressor
Fluid
See
See
Sump Capacity
7 US gallons
(26.5 liters)
7 US gallons
(26.5 liters)
7 US gallons
(26.5 liters)
Track Width
67.5"
(1714.5 mm)
67.5"
(1714.5 mm)
67.5"
(1714.5 mm)
Tire Size (Load Range)
H78 x 15ST (D)
H78 x 15ST (D)
H78 x 15ST (D)
Tire Pressure
65 psig (4.4 bar)
65 psig (4.4 bar)
65 psig (4.4 bar)
Wheel Size
15 x 6JJ
15 x 6JJ
15 x 6JJ
Lug Nut Torque
60 ft-lbs (81 Nm)
60 ft-lbs (81 Nm)
60 ft-lbs (81 Nm)
Operating Tilt (maximum)
15°
15°
15°
Electrical System
12 volt
12 volt
12 volt
Compressor Discharge
Temperature
Shutdown 250°F (121°C)
Shutdown 250°F (121°C)
Shutdown 250°F (121°C)
Service Valves (American)
(2) 3/4”
(2) 3/4”
(2) 3/4”
Service Valves (CE)
(3) 3/4” + (1) 1-1/4”
(3) 3/4” + (1) 1-1/4”
(3) 3/4” + (1) 1-1/4”
Maximum Towing Speed
55 mph (88 kmph)
55 mph (88 kmph)
55 mph (88 kmph)
Axle Rating
5000 lbs
(2268 kg)
5000 lbs
(2268 kg)
5000 lbs
(2268 kg)
Sound Level (US EPA)
1
76 dBA
76 dBA
76 dBA
Soun dLevel (CE)
2
71 dBA
71 dBA
1
Sound level measured per U.S. CFR Ch. 1 Part 204
2
Sound level measure per 2000/14/EC Outdoor Noise Directive
(III) American models.
Summary of Contents for 300HH
Page 17: ...SECTION 1 15 Safety Symbols 2 ...
Page 18: ...SECTION 1 16 Safety Symbols 3 ...
Page 49: ...SECTION 2 300HH 375 375H 375HH 425 AND 425H USER MANUAL R00 47 2 9 WIRING DIAGRAM ...
Page 60: ...NOTES 58 ...
Page 79: ...NOTES ...