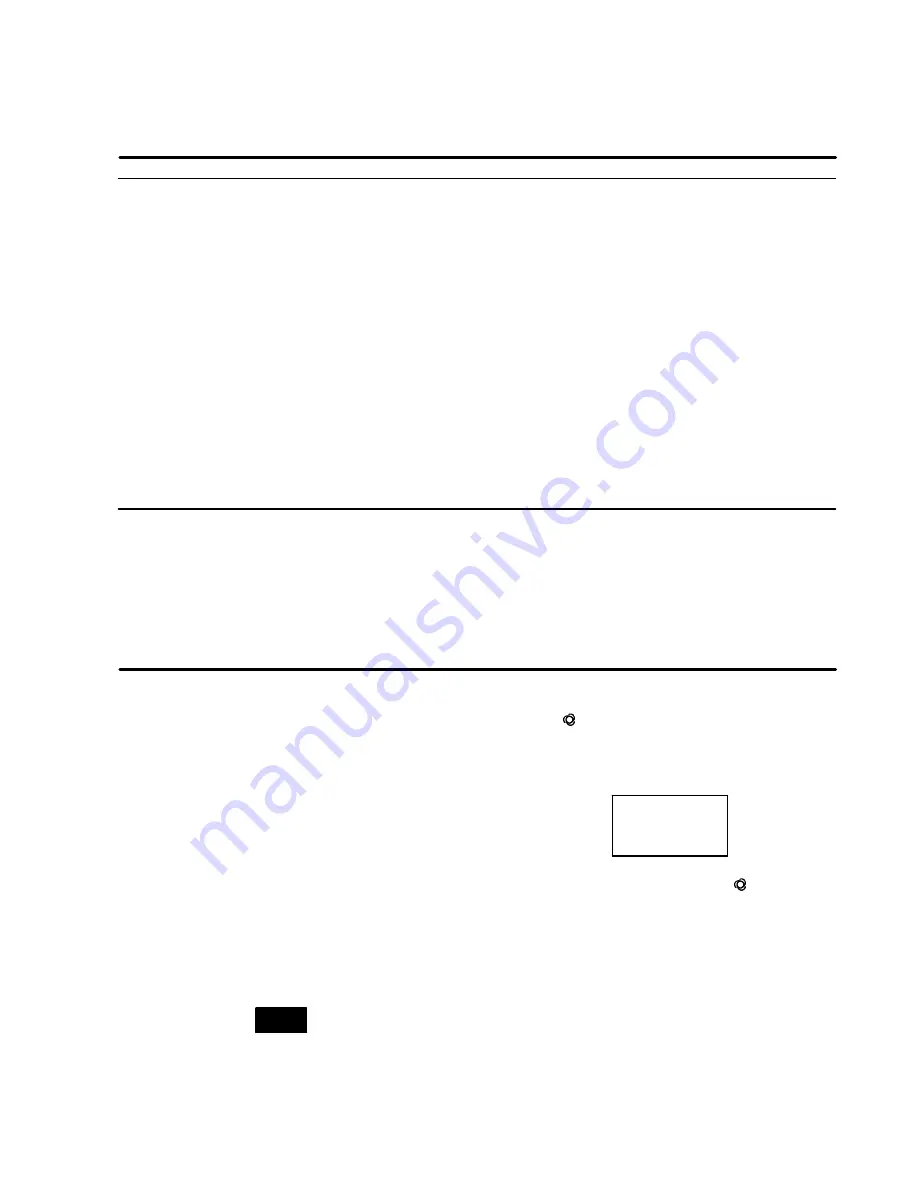
Section 8
TROUBLESHOOTING
39
8.2 TROUBLESHOOTING (CONTINUED)
SYMPTOM/MESSAGE
PROBABLE CAUSE
REMEDY
COOL FLT
Cooling Fan Motor Starter Overloads
Reset after heater elements cool down.
Tripped
Should trouble persist, check whether
motor starter contacts are functioning
properly.
COMPRESSOR DOES NOT
Air Demand Exceeds Supply
Check air service lines for open
BUILD FULL DISCHARGE
valves or leaks.
PRESSURE
Inlet Air Filter Clogged
Check for maintenance message
on Supervisor
II
display. Change
element.
Inlet Air Valve Not Fully Open
Check actuation and butterfly disc
position.
Low oil pressure defective control
solenoid valve.
Transducer P2 Malfunction
Check connections from trans---
ducer. If adequate, replace trans---
ducer.
Blowdown Valve Leaking
Refer to Component Manual for
or Sluggish
valve maintenance.
Limit Switch Controlling BVD Failed
Check limit switch and cam adjuster
to Operate
on butterfly valve.
Defective LP Stage
Consult Sullair Service Department.
LINE PRESSURE RISES ABOVE
Blowdown Valve Failed to
Refer to Component Manual for
UNLOAD SETTING
Activate
valve maintenance.
Inlet Throttling Valve Not Fully Open
See inlet valve adjustment.
Limit Switch Controlling BVD Failed
Check limit switch and cam adjuster
to Operate
on butterfly valve.
Transducer P2 Malfunction
Check connections from transducer.
If adequate, replace transducer.
Control Air Filter Clogged
Refer to Component Manual for valve
maintenance. Check operation of limit
switch.
NOTE ON TRANSDUCERS:
Whenever a sen-
sor is suspected of fault, the recommended
cause of action is to measure the signal (pres-
sure, temperature, etc.) with an alternate cali-
brated instrument and compare readings. If
readings conflict, the electrical and/or tubing
connections should be inspected, and if no
faults are evident, then replace the sensor and
re---evaluate against the calibrated instrument.
8.3 CALIBRATION
The Supervisor
II
has software calibration of the
pressure and temperature probes. This calibra-
tion affects the offset but not the slope of the
pressure and temperature calculations. Be-
cause of this, the most accurate method is to
heat or pressurize the transducer to its operating
value. If this is too difficult, room temperature/
open atmosphere calibration is adequate. Cal-
ibration may only be done while machine is
stopped and unarmed.
NOTE
Calibration mode may be entered from the de-
fault display mode when the machine is in
“MANUAL” SHUTDOWN.
To enter calibration mode, you must press the
following keys in sequence:
“LOGO”, DELTA,
DSP, “ ”, PRG
. Once in calibration mode, you
will see a screen like the following: In the above
example, “0” refers to the amount of adjustment
(in psi or
_
F, “97” refers to the current value of
P1).
CAL P1
97
0
To make adjustments, Press the
“DELTA”
key to
increase the value, press the
“ ”
key to de-
crease the value. The number on the left will in-
crease or decrease always showing the total
amount of adjustment. Maximum adjustments is
+/---7.
Other keys operate the same as in program
mode. The
“LOGO”
key restores the original val-
ue of the current item. The
“DSP”
key exits, wip-
ing out changes to the current item, while saving
changes to any previous items. The
“PRG”
key
saves the current item and advances to the next.
Items following P1 calibration are (in order): P1,
P2, P3, P4, T1, T2, T3, T4 and T5 calibration.
Summary of Contents for DR-13 Series
Page 6: ...NOTES ...
Page 14: ...8 NOTES ...
Page 18: ...Section 4 COMPRESSOR SYSTEMS 12 Figure 4 5 Piping and Instrumentation Diagram Air cooled ...
Page 21: ...Section 5 SUPERVISOR II 15 Figure 5 1 Supervisor II Panel ...
Page 28: ...22 NOTES ...
Page 32: ...26 NOTES ...
Page 42: ...Section 7 MAINTENANCE 36 Table 1 Installation Data ...
Page 46: ...40 NOTES ...
Page 48: ...Section 9 ILLUSTRATIONS AND PARTS LIST 42 9 3 COMPRESSOR MOTOR AND FRAME ...
Page 50: ...Section 9 ILLUSTRATIONS AND PARTS LIST 44 9 4 AIR INLET SYSTEM ...
Page 52: ...Section 9 ILLUSTRATIONS AND PARTS LIST 46 9 5 COOLER ASSEMBLY ...
Page 54: ...Section 9 ILLUSTRATIONS AND PARTS LIST 48 9 6 LP HOT LP COLD ...
Page 56: ...Section 9 ILLUSTRATIONS AND PARTS LIST 50 9 7 HP DISCHARGE ...
Page 58: ...Section 9 ILLUSTRATIONS AND PARTS LIST 52 9 8 LUBE SYSTEM ...
Page 60: ...Section 9 ILLUSTRATIONS AND PARTS LIST 54 9 9 ELECTRICAL BOX ...
Page 62: ...Section 9 ILLUSTRATIONS AND PARTS LIST 56 9 10 CONTROL SYSTEM CONDENSATE DRAIN ...
Page 64: ...Section 9 ILLUSTRATIONS AND PARTS LIST 58 9 11 CANOPY ...
Page 66: ...Section 9 ILLUSTRATIONS AND PARTS LIST 60 9 12 DECALS ...
Page 68: ...Section 9 ILLUSTRATIONS AND PARTS LIST 62 9 12 DECALS ...
Page 70: ...Section 9 ILLUSTRATIONS AND PARTS LIST 64 9 12 DECALS ...
Page 72: ...Section 9 ILLUSTRATIONS AND PARTS LIST 66 9 13 DECAL LOCATIONS ...
Page 74: ...Section 9 ILLUSTRATIONS AND PARTS LIST 68 9 13 DECAL LOCATIONS ...
Page 76: ...Section 9 ILLUSTRATIONS AND PARTS LIST 70 9 13 DECAL LOCATIONS ...
Page 78: ...Section 9 ILLUSTRATIONS AND PARTS LIST 72 9 14 WIRING DIAGRAM ...
Page 79: ...NOTES ...