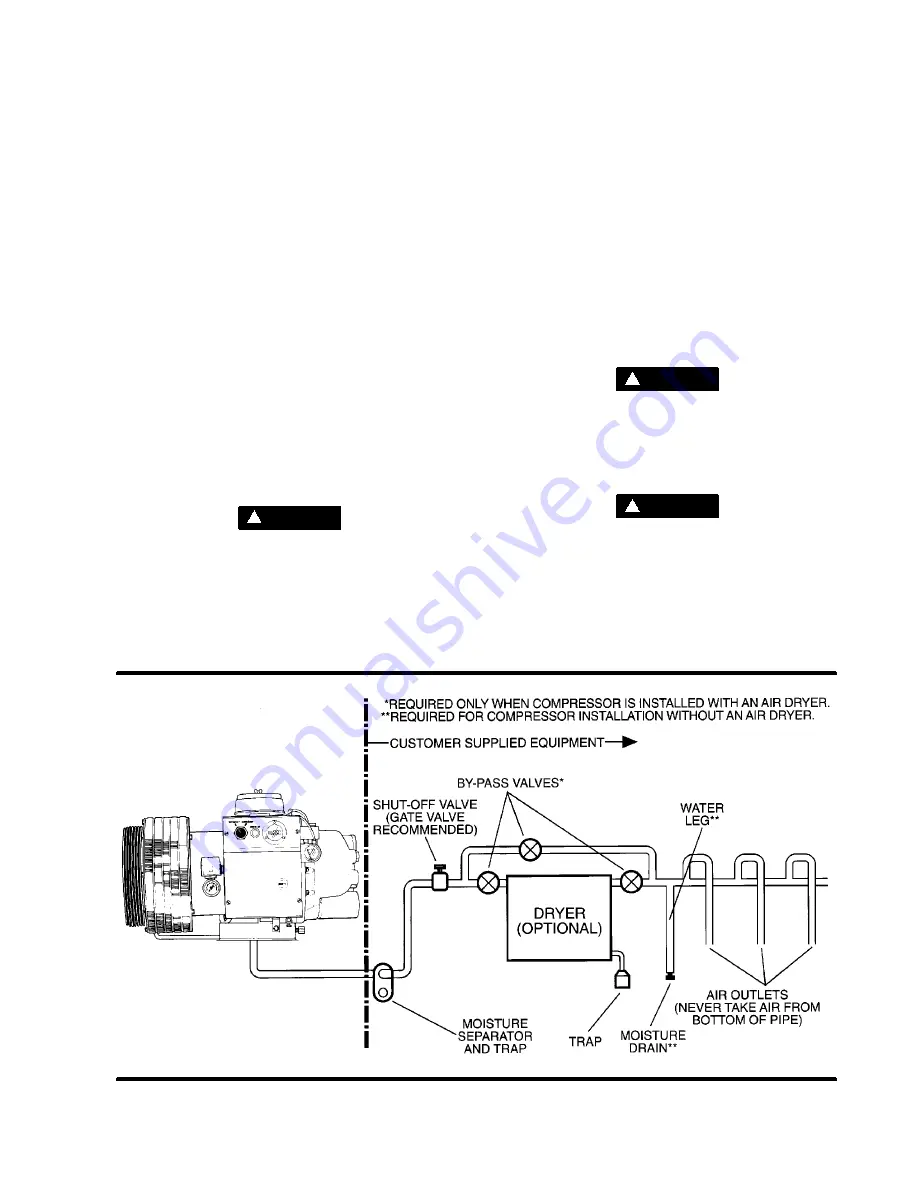
Section 4
INSTALLATION
11
4.1 LOCATION OF COMPRESSOR
The ES--6 Series compressor package may be
placed on any level surface able to support its
weight. The unit should be bolted to a fixed mounting
surface to avoid the possibility of externally applied
forces or vibration which would disturb the piping or
wiring.
4.2 VENTILATION AND COOLING
Select a location to permit sufficient unobstructed
air flow in and out of the compressor to keep the op-
erating temperature stable. The minimum distance
that the machine should be from surrounding walls
is what is needed for service and three (3) feet
(914mm) or more from the fan air discharge end of
the compressor.
4.3 SERVICE AIR PIPING
Service air piping should be installed as shown in
. A s hut -- off v alv e s hould be ins t alled t o
isolate the compressor from the service line. Also
notice that the service line should be equipped with
water legs and condensate drains throughout the
system.
WARNING
!
“The Plastic Pipe Institute recommends against
the use of thermoplastic pipe to transport com-
pressed air or other compressed gases in ex-
posed above ground locations, e.g. in exposed
plant piping.” (I)
Sullube 32 should not be used with PVC piping
systems. It may affect the bond at cemented
joints. Certain other plastic materials may also be
affected.
(I) Plastic Pipe Institute, Recommendation B, Adopted January
19, 1972.
4.4 FLUID LEVEL CHECK AND CHANGE PROCE-
DURE
The Sullair air compressor is equipped with the
proper amount of fluid. However, it is necessary to
check the fluid level at installation. The level is
checked by looking at the fluid level sight glass lo-
c at ed on t he end bell. S ee
If the sump is properly filled, the fluid level should
cover 1/4 to 1/2 of the sight glass during operation.
DO NOT OVERFILL
.
WARNING
!
Before attempting compressor maintenance, dis-
connect compressor from power source and lock
out power source. Isolate compressor from line
pressure by closing recommended discharge
shutoff valve and releasing all internal pressure
from compressor.
WARNING
!
Assure that line pressure guage on compressor
indicates “ZERO” pressure before any work is
done. Failure to comply may cause injury.
When the compressor fluid is ready to be changed,
the compressor needs to be shutdown with the pow-
er to the compressor disconnected (see Warning
above). Drain the fluid from the compressor using
Figure 4--1 Service Air Piping
Summary of Contents for ES-6 series
Page 6: ...NOTES...
Page 30: ...Section 7 ILLUSTRATIONS AND PARTS LIST 24 ES 6 COMPRESSOR ASSEMBLY EXPLODED VIEW 5 5 AND 7 5KW...
Page 32: ...Section 7 ILLUSTRATIONS AND PARTS LIST 26 7 3 FLUID MANAGEMENT SYSTEM...
Page 34: ...Section 7 ILLUSTRATIONS AND PARTS LIST 28 7 4 INLET FILTER...
Page 36: ...Section 7 ILLUSTRATIONS AND PARTS LIST 30 7 5 SEAL AND DRIVE GEAR...
Page 38: ...Section 7 ILLUSTRATIONS AND PARTS LIST 32 7 6 MOTOR HOUSING AND PARTS 7 5 10HP 5 5 7 5KW ONLY...
Page 42: ...Section 7 ILLUSTRATIONS AND PARTS LIST 36 7 8 COMPRESSOR SYSTEM...
Page 44: ...Section 7 ILLUSTRATIONS AND PARTS LIST 38 7 9 INLET CONTROL...
Page 46: ...Section 7 ILLUSTRATIONS AND PARTS LIST 40 7 10 CONTROL BOX...
Page 48: ...Section 7 ILLUSTRATIONS AND PARTS LIST 42 7 10 CONTROL BOX...
Page 52: ...Section 7 ILLUSTRATIONS AND PARTS LIST 46 7 12 FRAME CANOPY AND PARTS...
Page 56: ...Section 7 ILLUSTRATIONS AND PARTS LIST 50 7 14 WYE DELTA ELECTRIC BOX ES 6...
Page 58: ...Section 7 ILLUSTRATIONS AND PARTS LIST 52 7 15 DECAL GROUP 7 8 9 11 12...
Page 60: ...Section 7 ILLUSTRATIONS AND PARTS LIST 54 7 15 DECAL GROUP 13...
Page 62: ...Section 7 ILLUSTRATIONS AND PARTS LIST 56 7 16 WIRING DIAGRAM SINGLE PHASE 60Hz...
Page 63: ...Section 7 ILLUSTRATIONS AND PARTS LIST 57 7 17 WIRING DIAGRAM THREE PHASE 60Hz...
Page 64: ...Section 7 ILLUSTRATIONS AND PARTS LIST 58 7 18 WIRING DIAGRAM 50 Hz...
Page 65: ...Section 7 ILLUSTRATIONS AND PARTS LIST 59 7 19 WIRING DIAGRAM 50 Hz WYE DELTA...
Page 66: ...NOTES...
Page 67: ...NOTES...