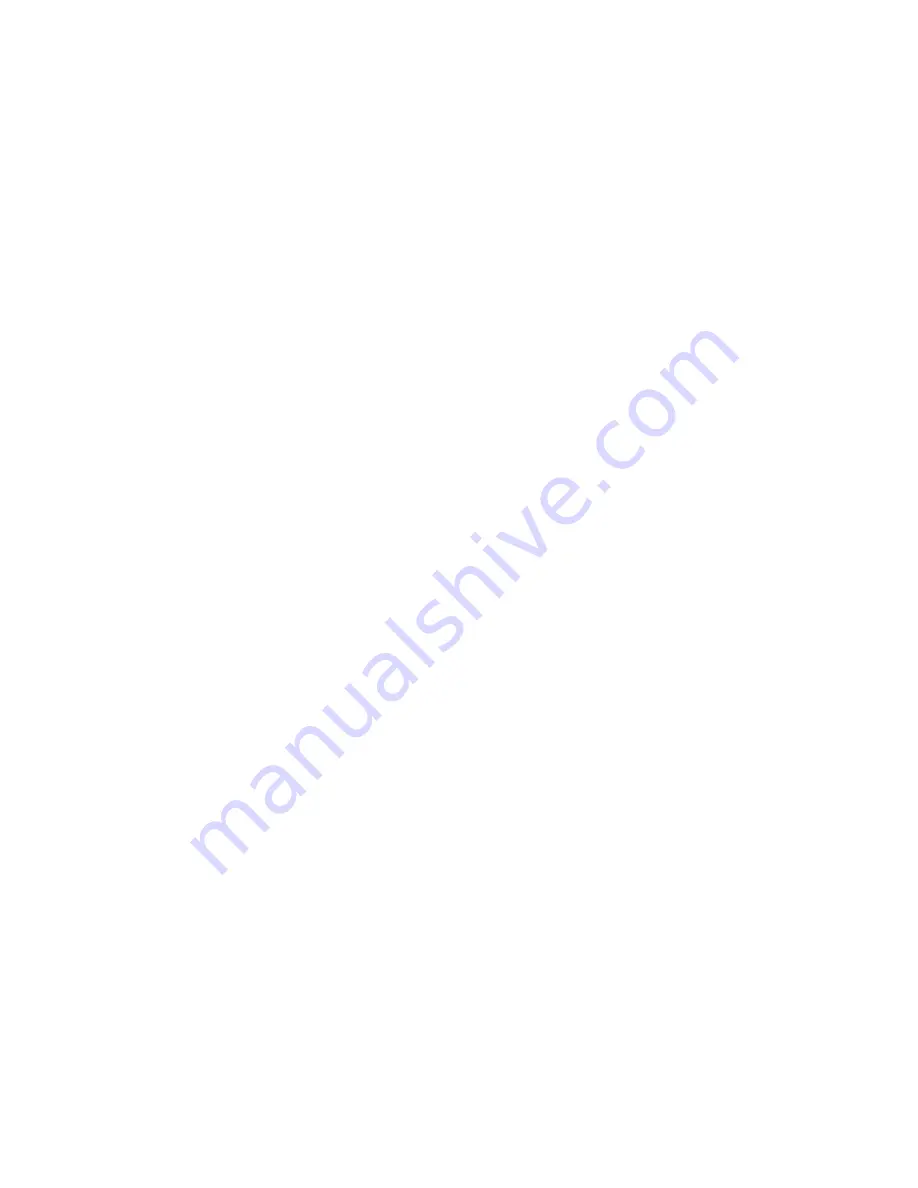
Section 1
SAFETY
3
supplying respirators or other breathing air utiliza-
tion equipment and
DO NOT
discharge air from
these systems into unventilated or other confined
areas.
C.
Operate the compressor only in open or ade-
quately ventilated areas.
D.
Locate the compressor or provide a remote inlet
so that it is not likely to ingest exhaust fumes or
other toxic, noxious or corrosive fumes or sub-
stances.
E.
Coolants and lubricants used in this compressor
are typical of the industry. Care should be taken to
avoid accidental ingestion and/or skin contact. In
the event of ingestion, seek medical treatment
promptly. Wash with soap and water in the event of
skin contact. Consult Material Safety Data Sheet for
information pertaining to fluid of fill.
F.
Wear goggles or a full face shield when adding
antifreeze compound to air line anti-icer systems.
G.
If air line anti-icer system antifreeze compound
enters the eyes or if fumes irritate the eyes, they
should be washed with large quantities of clean
water for fifteen minutes. A physician, preferably an
eye specialist, should be contacted immediately.
H. DO NOT
store air line anti-icer system antifreeze
compound in confined areas.
I.
The antifreeze compound used in air line
antifreeze systems contains methanol and is toxic,
harmful or fatal if swallowed. Avoid contact with the
skin or eyes and avoid breathing the fumes. If swal-
lowed, induce vomiting by administering a table-
spoon of salt, in each glass of clean, warm water
until vomit is clear, then administer two teaspoons
of baking soda in a glass of clean water. Have
patient lay down and cover eyes to exclude light.
Call a physician immediately.
1.8 ELECTRICAL SHOCK
A.
This compressor should be installed and main-
tained in full compliance with all applicable Federal,
State and Local codes, standards and regulations,
including those of the National Electrical Code, and
also including those relative to equipment ground-
ing conductors, and only by personnel that are
trained, qualified and delegated to do so.
B.
Keep all parts of the body and any hand-held
tools or other conductive objects away from
exposed live parts of electrical system. Maintain dry
footing, stand on insulating surfaces and
DO NOT
contact any other portion of the compressor when
making adjustments or repairs to exposed live parts
of the electrical system. Make all such adjustments
or repairs with one hand only, so as to minimize the
possibility of creating a current path through the
heart.
C.
Attempt repairs in clean, dry and well lighted and
ventilated areas only.
D. DO NOT
leave the compressor unattended with
open electrical enclosures. If necessary to do so,
then disconnect, lock out and tag all power at
source so others will not inadvertently restore
power.
E.
Disconnect, lock out, and tag all power at source
prior to attempting repairs or adjustments to rotating
machinery and prior to handling any ungrounded
conductors.
1.9 LIFTING
A.
If the compressor is provided with a lifting bail,
then lift by the bail provided. If no bail is provided,
then lift by sling. Compressors to be air-lifted by hel-
icopter must not be supported by the lifting bail but
by slings instead. In any event, lift and/or handle
only in full compliance with OSHA standards 29
CFR 1910 subpart N and/or any applicable Federal,
State, and Local codes, standards and regulations.
B.
Inspect points of attachment for cracked welds
and for cracked, bent, corroded or otherwise
degraded members and for loose bolts or nuts prior
to lifting.
C.
Make sure entire lifting, rigging and supporting
structure has been inspected, is in good condition
and has a rated capacity of at least the weight of
the compressor. If you are unsure of the weight,
then weigh compressor before lifting.
D.
Make sure lifting hook has a functional safety
latch or equivalent, and is fully engaged and latched
on the bail or slings.
E.
Use guide ropes or equivalent to prevent twisting
or swinging of the compressor once it has been lift-
ed clear of the ground.
F. DO NOT
attempt to lift in high winds.
G.
Keep all personnel out from under and away
from the compressor whenever it is suspended.
H.
Lift compressor no higher than necessary.
I.
Keep lift operator in constant attendance whenev-
er compressor is suspended.
J.
Set compressor down only on a level surface
capable of safely supporting at least its weight and
its loading unit.
K.
When moving the compressor by forklift truck,
utilize fork pockets if provided. Otherwise, utilize
Summary of Contents for LS-20T
Page 6: ......
Page 20: ...Section 2 DESCRIPTION 14 Figure 2 4A Control System Diagram Functional Components...
Page 21: ...Section 2 DESCRIPTION 15 Figure 2 4B Control System Diagram START...
Page 22: ...Section 2 DESCRIPTION 16 Figure 2 4C Control System Diagram MODULATION...
Page 23: ...Section 2 DESCRIPTION 17 Figure 2 4D Control System Diagram FULL LOAD...
Page 24: ...Section 2 DESCRIPTION 18 Figure 2 4E Control System Diagram UNLOAD...
Page 26: ...NOTES 20...
Page 30: ...NOTES 24...
Page 34: ...NOTES 28...
Page 42: ...NOTES 36...
Page 46: ...NOTES 40...
Page 49: ...NOTES 43...
Page 50: ...Section 9 ILLUSTRATIONS AND PARTS LIST 44 02250137 909R00 9 3 MOTOR FRAME COMPRESSOR AND PARTS...
Page 52: ...Section 9 ILLUSTRATIONS AND PARTS LIST 46 02250137 907R03 9 4 AIR INLET SYSTEM...
Page 54: ...Section 9 ILLUSTRATIONS AND PARTS LIST 48 02250137 907R03 9 4 AIR INLET SYSTEM...
Page 56: ...Section 9 ILLUSTRATIONS AND PARTS LIST 50 02250138 702R00 9 5 AIR INLET SUB ASSEMBLY...
Page 58: ...Section 9 ILLUSTRATIONS AND PARTS LIST 52 02250137 908R00 9 6 WATER COOLING SYSTEM...
Page 60: ...Section 9 ILLUSTRATIONS AND PARTS LIST 54 02250137 910R01 9 7 AIR PIPING SYTEM...
Page 62: ...Section 9 ILLUSTRATIONS AND PARTS LIST 56 02250137 912R01 9 8 FLUID PIPING SYSTEM...
Page 64: ...Section 9 ILLUSTRATIONS AND PARTS LIST 58 02250139 798R00 9 9 WATER PIPING SYSTEM...
Page 66: ...Section 9 ILLUSTRATIONS AND PARTS LIST 60 02250137 911R01 9 10 DISCHARGE SYSTEM...
Page 68: ...Section 9 ILLUSTRATIONS AND PARTS LIST 62 02250137 911R01 9 10 DISCHARGE SYSTEM...
Page 70: ...Section 9 ILLUSTRATIONS AND PARTS LIST 64 02250137 911R01 9 10 DISCHARGE SYSTEM...
Page 72: ...Section 9 ILLUSTRATIONS AND PARTS LIST 66 02250137 914R02 9 11 CONTROL START SYSTEM...
Page 74: ...Section 9 ILLUSTRATIONS AND PARTS LIST 68 02250137 914R02 9 11 CONTROL START SYSTEM...
Page 76: ...Section 9 ILLUSTRATIONS AND PARTS LIST 70 9 12 CONTROL PANEL 02250138 633R00...
Page 78: ...Section 9 ILLUSTRATIONS AND PARTS LIST 72 9 13 ENCLOSURE 02250138 672R00...
Page 80: ...Section 9 ILLUSTRATIONS AND PARTS LIST 74 9 13 ENCLOSURE 02250138 672R00...
Page 82: ...Section 9 ILLUSTRATIONS AND PARTS LIST 76 9 14 DECAL GROUP...
Page 84: ...Section 9 ILLUSTRATIONS AND PARTS LIST 78 9 14 DECAL GROUP...
Page 86: ...Section 9 ILLUSTRATIONS AND PARTS LIST 80 9 14 DECAL GROUP...
Page 88: ...Section 9 ILLUSTRATIONS AND PARTS LIST 82 9 15 DECAL LOCATION OPEN MODEL...
Page 90: ...Section 9 ILLUSTRATIONS AND PARTS LIST 84 9 16 DECAL LOCATION ENCLOSED MODEL...
Page 92: ...Section 9 ILLUSTRATIONS AND PARTS LIST 86 9 17 DECAL LOCATION CONTROL BOX...
Page 94: ...Section 9 ILLUSTRATIONS AND PARTS LIST 88 9 18 WIRING DIAGRAM LS20T 525 PSIG 02250137 917R01...
Page 95: ...NOTES 89...