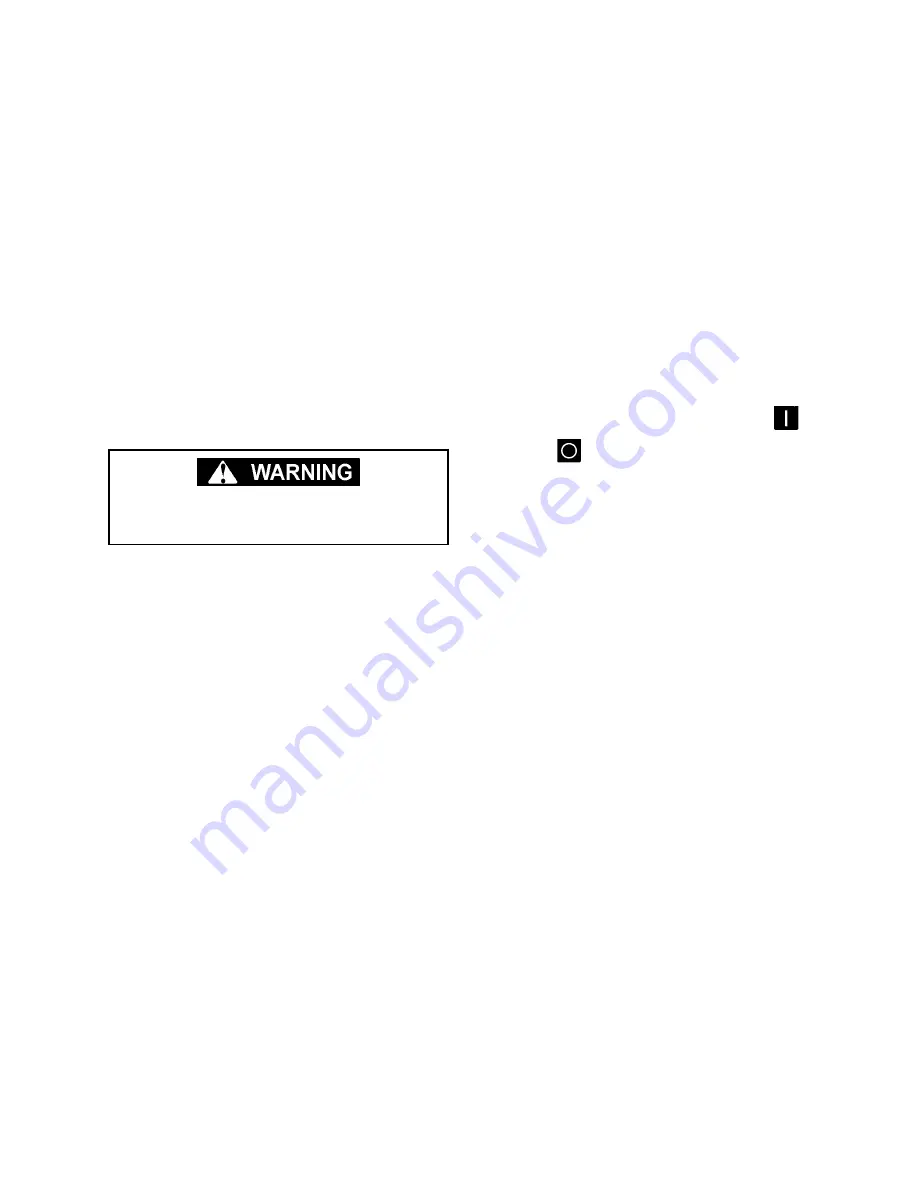
Section 4
INSTALLATION
25
to check this alignment, unless high vibration is
noticed.
4.5 FLUID LEVEL CHECK
Your air compressor is also supplied with the prop-
er amount of fluid. However, it is necessary to
check the fluid level at installation. The level is
checked by looking at the sight glass located on the
sump. If the sump is properly filled, the coolant level
should fill 1/2 of the sight glass when the compres-
sor is shutdown.
4.6 ELECTRICAL PREPARATION
Interior electrical wiring is performed at the factory.
Required customer wiring is minimal, but should be
done by a qualified electrician in compliance with
any applicable regional or local electrical code con-
cerning isolation switches, fuse disconnects, etc.
Sullair provides a wiring diagram for use by the
installer.
1. Check incoming voltage. Be sure that the incom-
ing voltage is the same voltage that the com-
pressor was wired for.
2. Check starter and overload heater sizes (see
electrical parts in Parts Manual).
3. Check all electrical connections for tightness.
4. “DRY RUN” the electrical controls by disconnect-
ing the three (3) motor leads from the starter.
Pull out the EMERGENCY STOP button on the
control panel. Depress the PROG pad twice to
get to AUTOMATIC/MANUAL mode selection
and use the cursor pad to change to MANUAL
mode.
5. Reconnect the three (3) motor leads and jog the
motor for a direction of rotation check, as
explained in Section 4.7.
4.7 MOTOR ROTATION CHECK
After the electrical installation has been done, it is
necessary to check the direction of motor rotation.
With the control system in MANUAL MODE, pull out
the
EMERGENCY STOP
button and press once,
quickly and in succession, the (
START
) “
” and
(
STOP
) “
” pads. This action will bump start the
motor for a very short time. When looking at the
motor rear end, the driveline should be rotating in
the direction indicated by the “Direction of Rotation”
decal located on the top of the compressor/motor
adapter piece. If the reversed rotation is noted, dis-
connect the power to the starter and exchange any
two of the three power input leads, then re-check
rotation. A “Direction of Rotation” decal is located on
the top of the compressor/motor adapter piece.
Lethal shock hazard inside.
Disconnect all power at source before opening or
servicing starter or control panel.
Summary of Contents for LS20T 1100 CFM
Page 18: ...Section 2 DESCRIPTION 12 Figure 2 3B Control System Diagram START...
Page 19: ...Section 2 DESCRIPTION 13 Figure 2 3C Control System Diagram MODULATION...
Page 20: ...Section 2 DESCRIPTION 14 Figure 2 3D Control System Diagram FULL LOAD...
Page 21: ...Section 2 DESCRIPTION 15 Figure 2 3E Control System Diagram UNLOAD...
Page 44: ...NOTES 38...
Page 104: ...Section 9 ILLUSTRATIONS AND PARTS LIST 98 02250146 367R00 9 19 CONTROL START SYSTEM...
Page 106: ...Section 9 ILLUSTRATIONS AND PARTS LIST 100 02250146 367R00 9 19 CONTROL START SYSTEM...
Page 108: ...Section 9 ILLUSTRATIONS AND PARTS LIST 102 02250138 633R00 9 20 CONTROL PANEL...
Page 110: ...Section 9 ILLUSTRATIONS AND PARTS LIST 104 02250139 119R01 9 21 ENCLOSURE...
Page 112: ...Section 9 ILLUSTRATIONS AND PARTS LIST 106 02250139 119R01 9 21 ENCLOSURE...
Page 114: ...Section 9 ILLUSTRATIONS AND PARTS LIST 108 9 22 DECAL GROUP...
Page 116: ...Section 9 ILLUSTRATIONS AND PARTS LIST 110 9 22 DECAL GROUP...
Page 118: ...Section 9 ILLUSTRATIONS AND PARTS LIST 112 9 22 DECAL GROUP...
Page 120: ...Section 9 ILLUSTRATIONS AND PARTS LIST 114 9 23 DECAL LOCATIONS OPEN AIR COOLED...
Page 122: ...Section 9 ILLUSTRATIONS AND PARTS LIST 116 9 24 DECAL LOCATIONS OPEN WATER COOLED...
Page 124: ...Section 9 ILLUSTRATIONS AND PARTS LIST 118 9 25 DECAL LOCATIONS REMOTE COOLER...
Page 126: ...Section 9 ILLUSTRATIONS AND PARTS LIST 120 9 26 DECAL LOCATIONS CONTROL BOX...
Page 128: ...Section 9 ILLUSTRATIONS AND PARTS LIST 122 9 27 ENCLOSURE DECALS...
Page 145: ...NOTES 139...