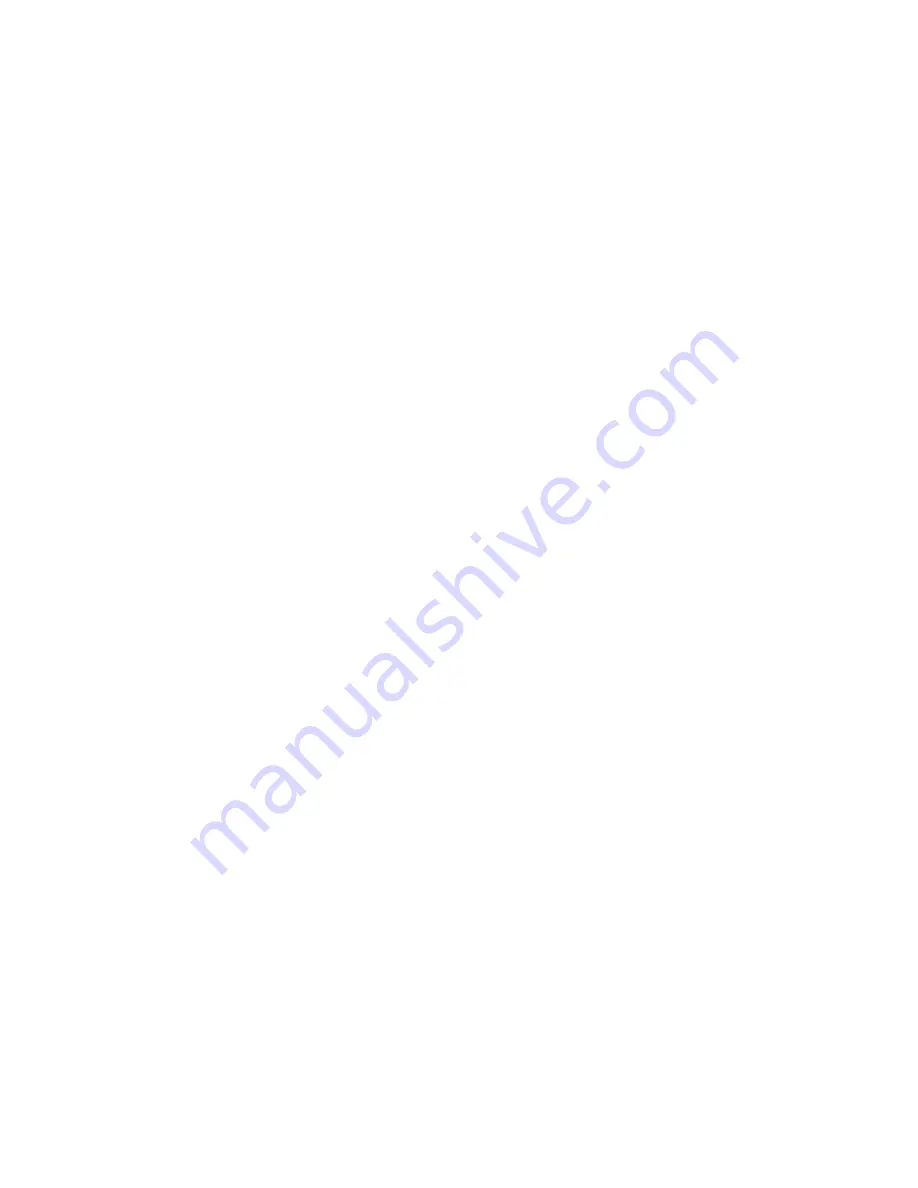
Section 1
SAFETY
1
1.1 GENERAL
Sullair Corporation and its subsidiaries design and
manufacture all of their products so they can be
operated safely. However, the responsibility for
safe operation rests with those who use and main-
tain these products. The following safety precau-
tions are offered as a guide which, if conscientious-
ly followed, will minimize the possibility of accidents
throughout the useful life of this equipment.
The compressor should be operated only by those
who have been trained and delegated to do so, and
who have read and understood this Operator’s
Manual. Failure to follow the instructions, proce-
dures and safety precautions in this manual can
result in accidents and injuries. Read this manual
prior to startup.
NEVER
start the compressor unless it is safe to do
so.
DO NOT
attempt to operate the compressor
with a known unsafe condition. Tag the compressor
and render it inoperative by disconnecting and lock-
ing out all power at source or otherwise disabling its
prime mover, so others who may not know of the
unsafe condition, cannot attempt to operate it until
the condition is corrected.
Install, use and operate the compressor only in full
compliance with all pertinent regulations and all
applicable Federal, State, and Local codes, stan-
dards and regulations.
DO NOT
modify the compressor and/or controls in
any way except with written factory approval.
While not specifically applicable to all types of com-
pressors with all types of prime movers, most of the
precautionary statements contained herein are
applicable to most compressors and the concepts
behind these statements are generally applicable to
all compressors.
1.2 PERSONAL PROTECTIVE EQUIPMENT
Prior to installing or operating the compressor, own-
ers, employers and users should become familiar
with, and comply with, all applicable regulations and
any applicable Federal, State and Local codes,
standards, and regulations relative to personal pro-
tective equipment, such as eye and face protective
equipment, respiratory protective equipment, equip-
ment intended to protect the extremities, protective
clothing, protective shields and barriers and electri-
cal protective equipment, as well as noise exposure
administrative and/or engineering controls and/or
personal hearing protective equipment.
1.3 PRESSURE RELEASE
A.
Install an appropriate flow-limiting valve between
the service air outlet and the shut-off (throttle)
valve, either at the compressor or at any other point
along the air line, when an air hose exceeding 1/2”
(13mm) inside diameter is to be connected to the
shut-off (throttle) valve, to reduce pressure in case
of hose failure, per all applicable Federal, State and
Local codes, standards and regulations.
B.
When the hose is to be used to supply a mani-
fold, install an additional appropriate flow-limiting
valve between the manifold and each air hose
exceeding 1/2” (13mm) inside diameter that is to be
connected to the manifold to reduce pressure in
case of hose failure.
C.
Provide an appropriate flow-limiting valve at the
beginning of each additional 75 feet (23m) of hose
in runs of air hose exceeding 1/2” (13mm) inside
diameter to reduce pressure in case of hose failure.
D.
Flow-limiting valves are listed by pipe size and
rated CFM. Select appropriate valves accordingly,
in accordance with their manufacturer’s recommen-
dations.
E. DO NOT
use air tools that are rated below the
maximum rating of the compressor. Select air tools,
air hoses, pipes, valves, filters, and other fittings
accordingly.
DO NOT
exceed manufacturer’s rated
safe operating pressures for these items.
F.
Secure all hose connections by wire, chain or
other suitable retaining devices to prevent tools or
hose ends from being accidentally disconnected
and expelled.
G.
Open fluid filler cap only when compressor is not
running and is not pressurized. Shut down the com-
pressor and bleed the sump (receiver) to zero inter-
nal pressure before removing the cap.
H.
Vent all internal pressure prior to opening any
line, fitting, hose, valve, drain plug, connection or
other component, such as filters and line oilers, and
before attempting to refill optional air line anti-icer
systems with antifreeze compound.
I.
Keep personnel out of line with and away from the
discharge opening of hoses or tools or other points
of compressed air discharge.
J.
Use air at pressures less than 30 psig (2.1 bar)
for cleaning purposes, and then only with effective
chip guarding and personal protective equipment.
K. DO NOT
engage in horseplay with air hoses as
death or serious injury may result.
L. DO NOT
tamper with sump and unit (if provid-
ed) relief valves. Check the relief valve as recom-
mended in the Maintenance Section of this manual
Summary of Contents for TS-32S
Page 16: ...Section 2 DESCRIPTION 10 Figure 2 3A Compressor Cooling and Lubrication System Air cooled...
Page 17: ...Section 2 DESCRIPTION 11 Figure 2 3B Compressor Cooling and Lubrication System Water cooled...
Page 18: ...Section 2 DESCRIPTION 12 Figure 2 4A Compressor Discharge System Air cooled...
Page 19: ...Section 2 DESCRIPTION 13 Figure 2 4B Compressor Discharge System Water cooled...
Page 20: ...Section 2 DESCRIPTION 14 Figure 2 5A Control System START Typical...
Page 21: ...Section 2 DESCRIPTION 15 Figure 2 5B Control System MODULATION Typical...
Page 22: ...Section 2 DESCRIPTION 16 Figure 2 5C Control System UNLOAD Typical...
Page 23: ...Section 2 DESCRIPTION 17 Figure 2 5D Control System FULL LOAD Typical...
Page 27: ...Section 3 SPECIFICATIONS 21 NOTES...
Page 40: ...34 NOTES...
Page 48: ...42 NOTES...
Page 60: ...54 NOTES...
Page 63: ...57 NOTES...
Page 72: ...Section 8 ILLUSTRATIONS AND PARTS LIST 66 8 5 AIR INLET SYSTEM 02250135 499R01...
Page 114: ...Section 8 ILLUSTRATIONS AND PARTS LIST 108 02250135 534R03 8 20 SUMP AND PARTS...
Page 116: ...Section 8 ILLUSTRATIONS AND PARTS LIST 110 02250135 534R03 8 20 SUMP AND PARTS...
Page 118: ...Section 8 ILLUSTRATIONS AND PARTS LIST 112 02250134 158R00 8 21 SULLICON CONTROL...
Page 120: ...Section 8 ILLUSTRATIONS AND PARTS LIST 114 8 22 COMPRESSOR SPIRIAL VALVE ACTUATOR...
Page 124: ...Section 8 ILLUSTRATIONS AND PARTS LIST 118 02250135 643R05 8 24 PNEUMATIC CONTROLS...
Page 126: ...Section 8 ILLUSTRATIONS AND PARTS LIST 120 02250135 643R05 8 24 PNEUMATIC CONTROLS...
Page 128: ...Section 8 ILLUSTRATIONS AND PARTS LIST 122 02250135 643R05 8 24 PNEUMATIC CONTROLS...
Page 134: ...Section 8 ILLUSTRATIONS AND PARTS LIST 128 8 27 CONTROL BOX WYE DELTA TYPICAL 02250122 516R08...
Page 140: ...Section 8 ILLUSTRATIONS AND PARTS LIST 134 02250133 674R04 8 30 ENCLOSURE AIR COOLED...
Page 142: ...Section 8 ILLUSTRATIONS AND PARTS LIST 136 02250133 674R04 8 30 ENCLOSURE AIR COOLED...
Page 144: ...Section 8 ILLUSTRATIONS AND PARTS LIST 138 02250133 675R04 8 31 ENCLOSURE WATER COOLED...
Page 146: ...Section 8 ILLUSTRATIONS AND PARTS LIST 140 02250133 675R04 8 31 ENCLOSURE WATER COOLED...
Page 148: ...Section 8 ILLUSTRATIONS AND PARTS LIST 142 8 32 DECALS...
Page 150: ...Section 8 ILLUSTRATIONS AND PARTS LIST 144 8 32 DECALS...
Page 152: ...Section 8 ILLUSTRATIONS AND PARTS LIST 146 8 32 DECALS...
Page 154: ...Section 8 ILLUSTRATIONS AND PARTS LIST 148 8 33 DECAL LOCATIONS...
Page 156: ...Section 8 ILLUSTRATIONS AND PARTS LIST 150 8 34 DECAL LOCATIONS AIR COOLED ENCLOSURE TYPICAL...
Page 158: ...Section 8 ILLUSTRATIONS AND PARTS LIST 152 8 35 DECAL LOCATIONS WATER COOLED ENCLOSURE TYPICAL...
Page 160: ...Section 8 ILLUSTRATIONS AND PARTS LIST 154 8 36 DECAL LOCATIONS CONTROL BOX...
Page 162: ...Section 8 ILLUSTRATIONS AND PARTS LIST 156 8 37 DECAL LOCATIONS AFTER COOLER...
Page 171: ...NOTES...