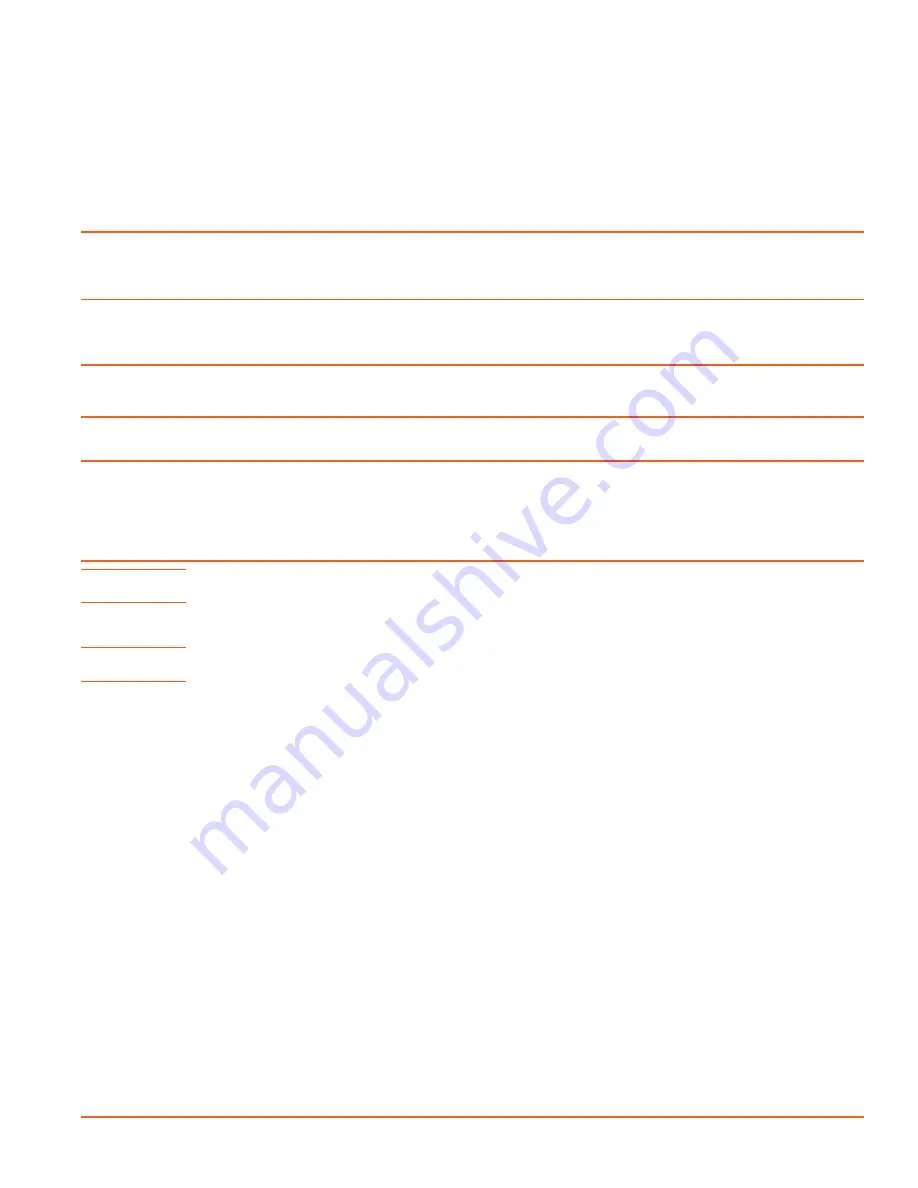
21
oPERATIon
»
Provide an appropriate flow-limiting valve for each additional 75 feet of hose in runs of air hose
exceeding 0.5-inch inside diameter to reduce pressure in case of hose failure.
»
Flow limiting valves are listed by pipe size and rated CFM. Select appropriate valves accordingly.
»
Do not exceed manufacturer’s rated safe operating pressures for these items.
»
Secure all hose connections by wire, chain, or other suitable retaining devices to prevent tools or hose
ends from being accidentally disconnected. Unrestrained disconnected hoses can flail around an cause
injury or damage.
»
Vent and release all internal pressure prior to opening any line, fitting, hose, valve, drain plug or
connection. This includes components such as filters, line oilers and optional airline anti-icing systems.
WARNING!
Serious injury can result from the direct discharge of compressed air. Do not allow personnel to be in line
or front of the discharge opening of the service valve, hoses or tools or other points of compressed air
discharge.
Air gun cleaning devices must not be used and pressures above 30 psig (2 Bars). Always use an appropriate
regulator to reduce pressure at the cleaning tool and always use with effective chip guarding and personal
protective equipment per OSHA Standard 29 CFR 1910.242 (b).
WARNING!
Serious injury or death may result from horseplay with air hoses and compressed air. HORSEPLAY - DO NOT
DO IT, DO NOT ALLOW IT!
5.10
JUMP-STARTING BATTERY
WARNING!
Always wear an acid-resistant apron, face shield with goggles, and gloves when working with batteries!
Batteries may contain hydrogen gas which is explosive and flammable! Keep flames, sparks and any other
source of ignition away. Batteries also contain acid which is corrosive and poisonous. DO NOT allow battery
acid to contact eyes, skin, or fabrics. Serious personal injury or property damage could result! Flush any
contacted areas thoroughly with water immediately and seek medical attention.
NOTE!
The following instructions are for single battery 12 VDC starting systems only. Make sure both compressor
and starting vehicle have the ignition “OFF” before connecting the jumper cables.
1.
Remove all vent caps from the battery or batteries in the compressor. Do not permit dirt or foreign
matter to enter the open cells.
CAUTION!
Remove vent caps on dead battery if the battery is a maintenance type and add distilled water if
needed. This is not required if the battery is a maintenance-free type that is sealed.
2.
Check fluid level. If low bring to a proper level before attempting to jump-start.
3.
Locate the starting vehicle beside the compressor, but do not permit metal-to-metal contact between
the compressor and the starting vehicle. Set the parking brakes of the compressor (if provided) and
the starting vehicle, or chock or block both sides of all wheels. Place the starting vehicle in park, turn off
nonessential accessory electrical loads and start its engine.
4.
Connect one end of the RED (positive) cable to the positive (+) terminal on the dead battery in the
compressor. Make sure the other end of this cable does not touch any metal surface that would cause
arcing!
5.
Connect the other end of the RED (positive ) cable to the positive (+) terminal on the good battery in the
starting vehicle.
6.
Connect one end of the BLACK (negative) cable to the negative (-) post on the good battery in the
starting vehicle.
7.
Connect the other end of the BLACK (negative) cable to an unpainted metal surface on the compressor
engine with the dead battery.
8.
Make sure all the jumper cable clips have a good connection (good clamping force) before attempting to
start.
9.
Start vehicle with the good battery first and let it run a few minutes. Then attempt to start the
compressor with the dead battery.
10.
If the compressor starts then allow it to warm up and then remove the jumper cables while keeping the
compressor running. Make sure not to let the clips of the cables touch while either end of the cables are
attached to one of the batteries. This would cause arcing.
Summary of Contents for D110PKU
Page 4: ......
Page 6: ...vi About This Manual ...
Page 13: ...5 2 SPECIFICATIONS TOPICS IN THIS SECTION Technical Data 6 Dimensions 7 ...
Page 16: ...8 Specifications ...
Page 44: ...36 Troubleshooting ...
Page 48: ...40 Parts Catalog 8 6 ENGINE ASSEMBLY ...
Page 50: ...42 Parts Catalog 8 7 ENGINE MOUNTING ASSEMBLY ...
Page 52: ...44 Parts Catalog 8 8 ENGINE TO FRAME ASSEMBLY ...
Page 54: ...46 Parts Catalog 8 9 BATTERY ASSEMBLY ...
Page 56: ...48 Parts Catalog 8 10 EXHAUST ASSEMBLY ...
Page 58: ...50 Parts Catalog 8 11 COMPRESSOR ASSEMBLY ...
Page 60: ...52 Parts Catalog 8 12 INLET VALVE ASSEMBLY ...
Page 62: ...54 Parts Catalog 8 13 AIR FILTER ASSEMBLY ...
Page 64: ...56 Parts Catalog 8 14 RECEIVER ASSEMBLY ...
Page 66: ...58 Parts Catalog 8 15 RECEIVER ASSEMBLY TO FRAME ...
Page 68: ...60 Parts Catalog 8 16 CONTROL TUBING ASSEMBLY ...
Page 70: ...62 Parts Catalog 8 17 COOLING ASSEMBLY ...
Page 72: ...64 Parts Catalog 8 18 COOLING ASSEMBLY ATTACHMENT TO FRAME ...
Page 74: ...66 Parts Catalog 8 19 COOLING SYSTEM HOSES AND RECOVERY TANK INSTALLATION ...
Page 76: ...68 Parts Catalog 8 20 OIL FILTER AND DISCHARGE HOSE ASSEMBLY ...
Page 78: ...70 Parts Catalog 8 21 FUEL TANK ASSEMBLY ...
Page 80: ...72 Parts Catalog 8 22 INSTRUMENT PANEL ASSEMBLY ...
Page 82: ...74 Parts Catalog 8 23 CANOPY ASSEMBLY ...
Page 84: ...76 Parts Catalog 8 24 CANOPY INSTALLATION ...
Page 86: ...78 Parts Catalog 8 25 LIFTING BAIL ASSEMBLY ...
Page 88: ...80 Parts Catalog 8 26 FRONT CROSSMEMBER ASSEMBLY ...
Page 90: ...82 Parts Catalog 8 27 LIGHT PACKAGE ...
Page 92: ...84 Parts Catalog 8 28 FENDER INSTALLATION ...
Page 94: ...86 Parts Catalog 8 29 AXLE AND WHEEL ASSEMBLY ...
Page 98: ...NOTES ...
Page 99: ...NOTES ...