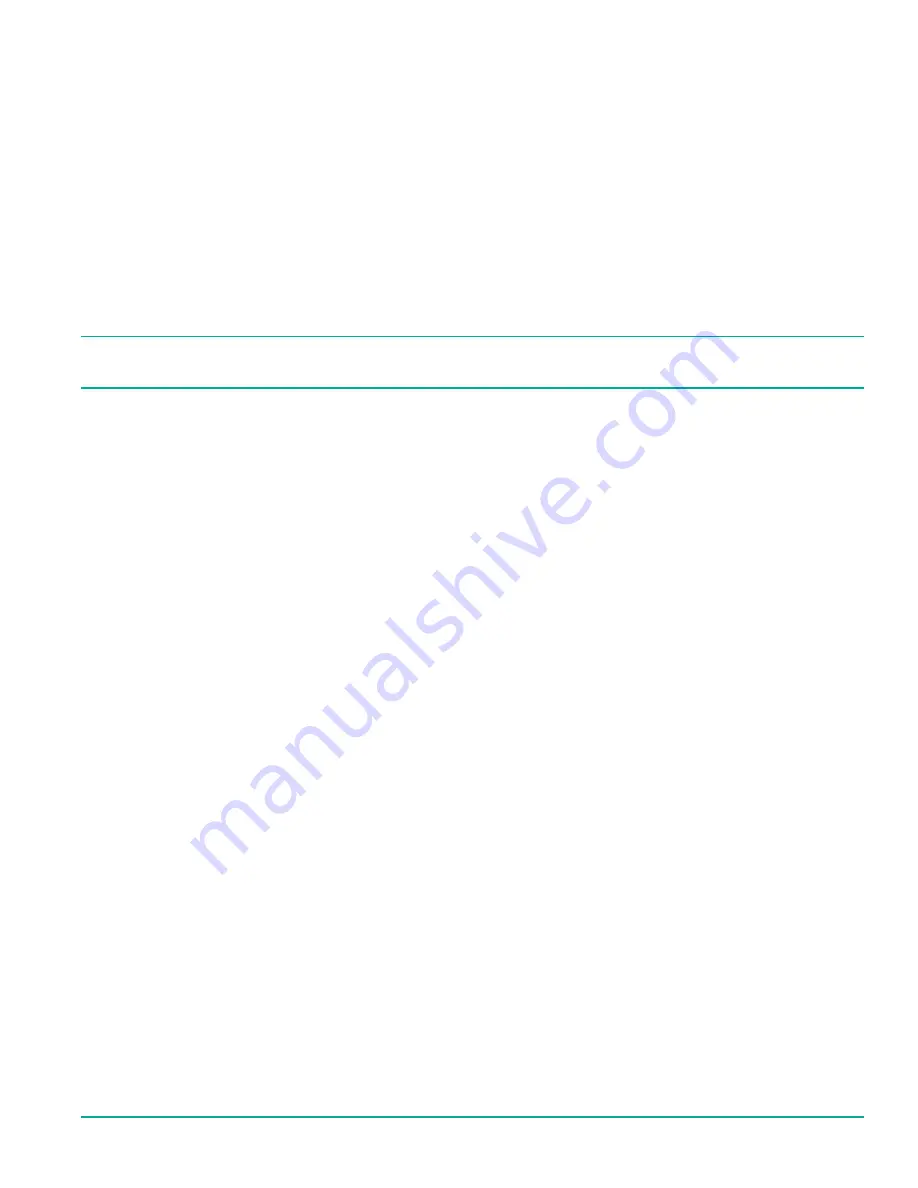
43
OPERATION
5.6
RESTARTS
If the compressor shuts down unexpectedly, special procedures must be followed to safely restart the
compressor. below are the procedures for safely restarting the compressor, depending on the reason for the
shutdown.
5.6.1
POWER FAILURE
1.
Open and lock out main power disconnect.
2.
Check all fuses and breakers.
3.
5.6.2
MOTOR TRIPPED OVERLOAD RELAY
1.
Open and lock out the main power disconnect.
2.
Push the starter overload reset button.
3.
Check the overload relay to be sure that it is properly sized and correctly adjusted.
4.
WARNING!
Never adjust the overload relay higher than indicated by the starter manufacturer to match motor
nameplate service factor amperage rating, as an unsafe condition will result!
Summary of Contents for UD Series
Page 6: ...vi About This Manual ...
Page 12: ...4 Introduction ...
Page 42: ...34 Component Description ...
Page 52: ...44 Operation ...
Page 66: ...58 Troubleshooting ...
Page 74: ...66 Parts Catalog 8 5 COMPRESSOR FRAME AND DRIVE ASSEMBLY Figure 8 1 AS801 25UD 50UD VFD R00 ...
Page 76: ...68 Parts Catalog 8 6 CONTROL ASSEMBLY OPEN Figure 8 2 1072190415 609 R00 ...
Page 78: ...70 Parts Catalog 8 7 STARTER ASSEMBLY ENCLOSED Figure 8 3 AS802 405060 PANEL R03 ...
Page 94: ...86 Parts Catalog 8 15 COOLING ASSEMBLY AIR COOLED Figure 8 11 AS804 50UDAC INLINE R00 ...
Page 100: ...NOTES ...
Page 101: ...NOTES ...