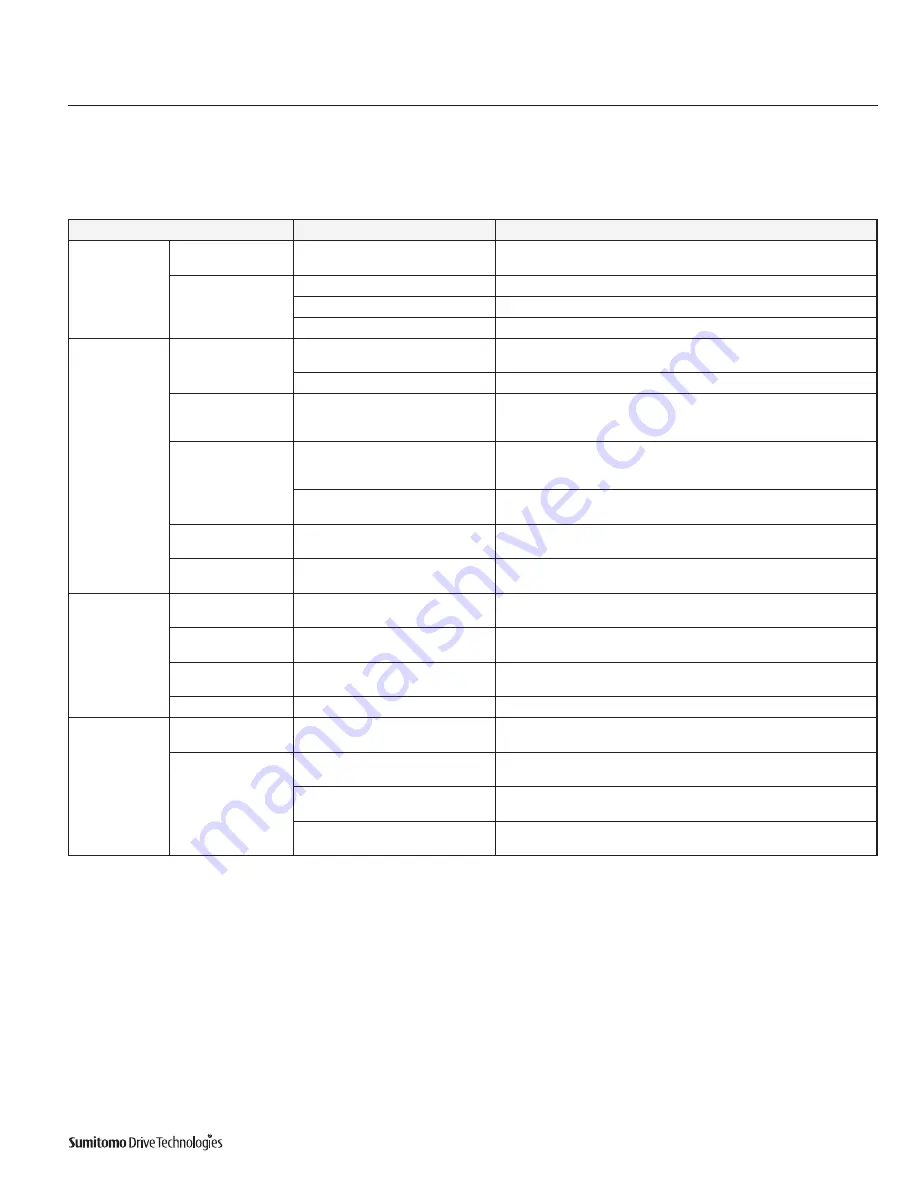
Cyclo® HBB
Operation & Maintenance Manual
45
Cyclo® HBB
Troubleshooting
This troubleshooting guide provides assistance in identifying and overcoming common problems in reducers and motors If you have a
problem with the reducer and/or the motor that is not listed below, please consult the factory for assistance
Problem with the Reducer
Possible Causes
Suggested Remedy
Runs Hot
Overloading
Load exceeds capacity of the reducer
Check the rated capacity of the reducer, replace with unit of sufficient capacity
or reduce the load
Improper lubrication
Insufficient lubricant
Check lubricant level and increase to recommended levels.
Excessive lubricant
Check lubricant level and reduce to recommended level.
Incorrect lubricant
Flush old lubricant from the unit and refill with correct recommended lubricant
Vibration or
Noise
Loose foundation bolts
Weak mounting structure
Inspect mounting of reducer Tighten loose bolts and/or reinforce mounting &
structure
Loose hold-down bolts
Tighten bolts
Worn disc and/or helical
gearing
Overloading of the unit may result in
damage to the Helical gearing and/or the
Cycloid discs
If helical gearset is damaged, contact the factory
If Cycloid discs are damaged, disassemble the Cyclo® portion and replace discs
Re-check the rated capacity of the unit.
Bearing Failure
May be due to lack of lubricant
If output bearings are damaged, contact the factory
If bearings in Cyclo® portion are damaged, replace the affected bearings Clean &
flush the reducer and fill with the correct type and quantity of lubricant
Overload
Check the rated capacity of the reducer. Replace with unit of sufficient capacity
or reduce the driven load
Insufficient Lubricant
Level of lubricant in the reducer not
properly maintained
Check lubricant level and adjust to factory-recommended level.
Damaged Cyclo® pins
and rollers
Overloading of reducer
Disassemble Cyclo® portion of reducer and replace ring
gear housing pins and rollers. Check load on reducer.
Output
Shaft/Hub does
not turn
Motor shaft broken
Overloading of reducer can cause
this type of damage
Replace broken shaft. Check rated capacity of reducer.
Input shaft key missing
or broken
Replace key.
Eccentric bearing
broken
Lack of Lubricant
Replace the Eccentric Bearing in the Cyclo® portion Flush
and refill the unit with the recommended lubricant
Motor does not turn
Motor
Refer to the “Motor” portion of this Troubleshooting guide
Oil Leakage
Worn seals
Caused by dirt or grit entering the seal
area
Replace the oil seals The breather filter may be clogged Replace or clean filter
Leakage into motor
Reducer has been overfilled with
lubricant
Check the lubricant level and adjust to the recommended level.
Air breather clogged
Clean or replace element, being sure to prevent any dirt from falling into the
reducer
Improper mounting position, such as
other than designed mounting angle
Mount the unit in it’s designed mounting angle
Summary of Contents for Cyclo HBB
Page 1: ...0 7 6 0 1 6 0 0 0 3 H B B O M2 0 1 8...
Page 27: ...MA X MI N...