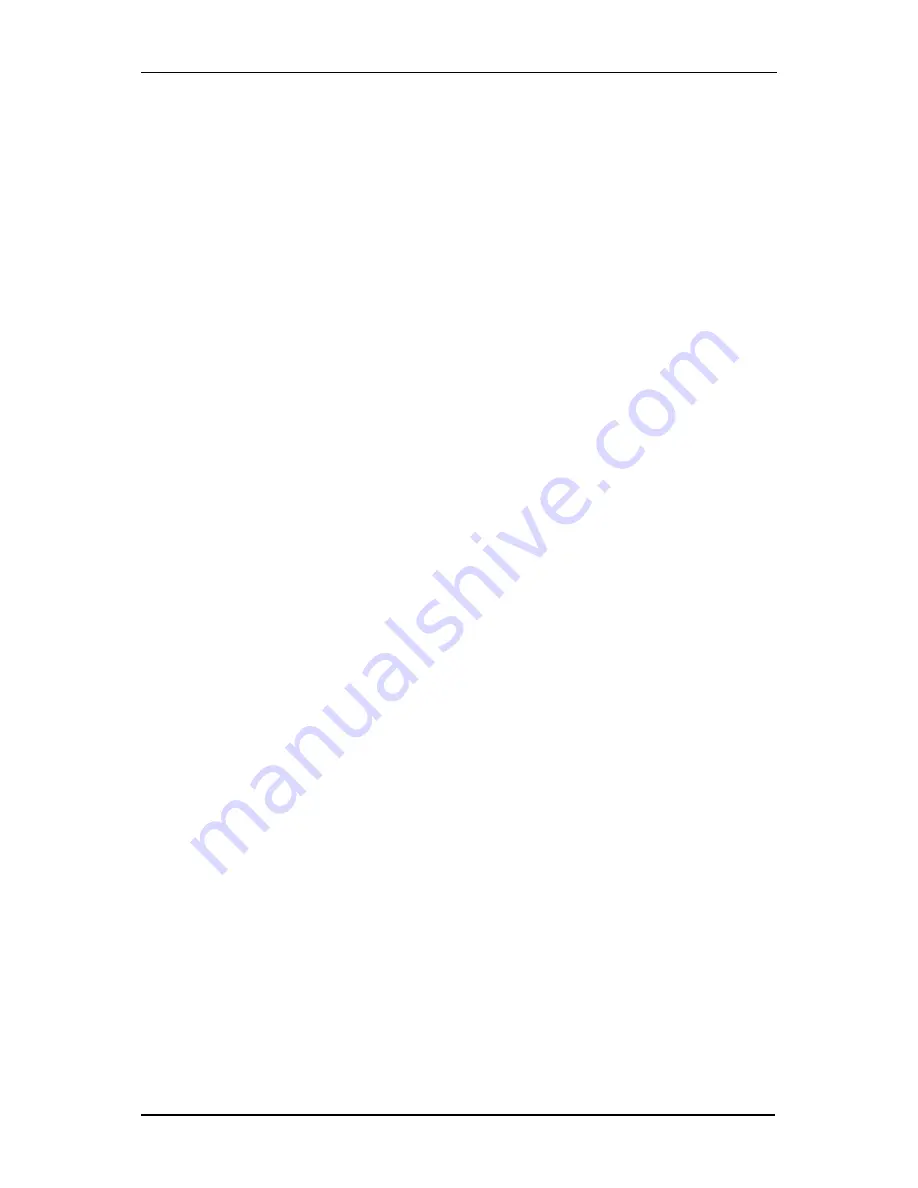
SummaSign
Service Manual
MOTOR HOT
Cause:
Heavy media
can overload the motors, especially the X-motor. The µP on the PCB
calculates the power dissipated in the motors. When this dissipation becomes too high, the
message MOTOR HOT appears. This is not a fatal error. After a while this message will
disappear and the machine will continue its operation.
Action:
1. Wait until the motor has cooled down to an acceptable level.
2. Lower the speed using the menu and use a lower knife pressure if possible.
3. Use lighter or smaller media.
4. Check the cam rollers, replace any damaged cam rollers.
5. Call CalComp for assistance. A system register may have changed the default value.
6. Check whether the drive drum is turning smoothly (first switch the machine off and place
the cam rollers in the up-position). Replace motor and/or drum.
ERROR IN X-AXIS
Cause:
The drum motor cannot move to the required position. This is a fatal error. It can only be
solved by turning the power off and then on again. This error is usually caused by a media
crash in the machine.
Action:
7. Remove the crashed media and restart the machine. Should this happen rather frequently,
the cause can be :
knife depth or pressure is not well set.
bad tracking because an unstabilised media type is used.
bad tracking because the humidity is too high or too low.
bad tracking because an unapproved type of media is used.
the media hit something on the floor while cutting.
the media shows already different tracks, so that the media does not know
which track to follow.
8. Lower the speed of the media.
9. Check whether the drive drum turns smoothly (first turn the power off and place the cam
rollers in the up-position).
10.If the error in the x-axis happens at start-up, check the x-axis motor,
the encoder
connectors and the cables.
11.Replace the X-motor encoder.
12.Replace the PCB.
13.
5-2
Troubleshooting-Error Codes
Summary of Contents for SummaSign D1010
Page 1: ...Service Manual SummaSign Series Summa NV Rochesterlaan 6 8470 Gistel Belgium...
Page 80: ...SummaSign Service Manual 106 107 2 36 Replacements Guidelines Blank page...
Page 85: ...Service Manual SummaSignT se 3 2 OPERATING VOLTAGE CONVERSION Maintenance and Cleaning 3 5...
Page 87: ...Service Manual SummaSignT se Maintenance and Cleaning 3 7 blank page...
Page 92: ...Service Manual SummaSign Calibration 4 5...
Page 93: ...SummaSign Service Manual HEAD CALIBRATION 4 6 Calibration...
Page 131: ...Service Manual SummaSign Spare Parts List 7 13...
Page 134: ...Summasign Service Manual 7 16 Spare Parts List...