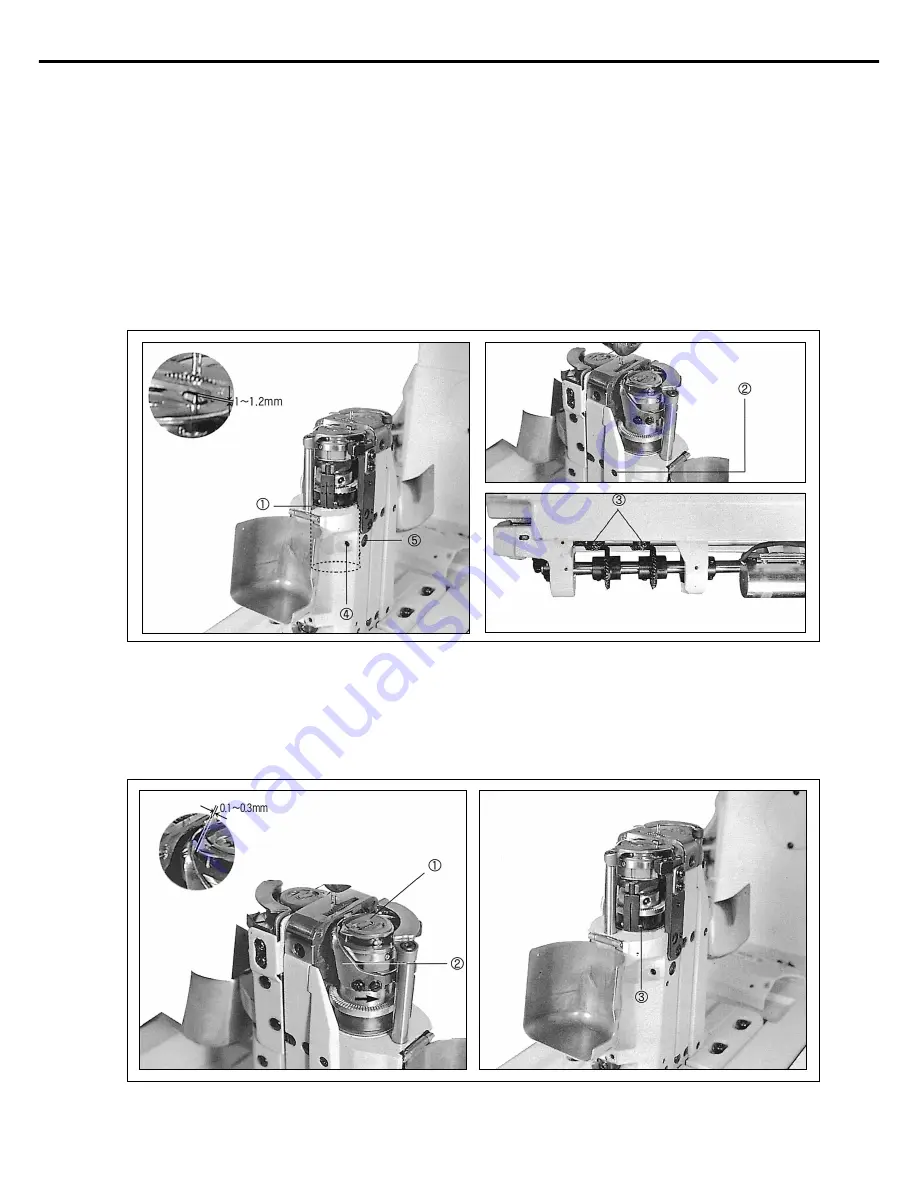
22
14) Adjusting clearance between upper side of hook stopper and needle plate groove
As in Figure 38, the clearance between the upper side of hook stopper and needle plate groove is set to 1~1.2mm by default.
This clearance could impact the stitch tension and thread separation when trimming, so it needs to be checked. If there is a
problem with the clearance, move the hook tray bushing
①
up and down to adjust as in Figure 38, but move it cautiously
after checking the assembly status of surrounding parts. The hook tray bushing
①
is fixed with a fixing screw
②
and when
moving it vertically, adjust with the hook tray bushing fixing screw
②
, hook shaft gear fixing screw
③
, the bushing adjusting
pin fixing screw
④
and the bushing adjusting pin
⑤
. After completion, the hook shaft should turn smoothly without moving
vertically. Fix the lower shaft gear while the hook edge and the needle timing do not change.
[Figure 38]
[Figure 39]
15) Adjusting clearance between hook and opener
When the opener
②
is pulled into the arrow direction to the max, the clearance between hook
①
and opener
②
should be
0.1~0.3mm. Loosen the opener position stopper clamp screw
③
and turn it left and right to adjust that.
Summary of Contents for KM-957 Series
Page 31: ...31 5 Table Drawing 1 KM 967 ...
Page 32: ...32 2 KM 967 7 ...