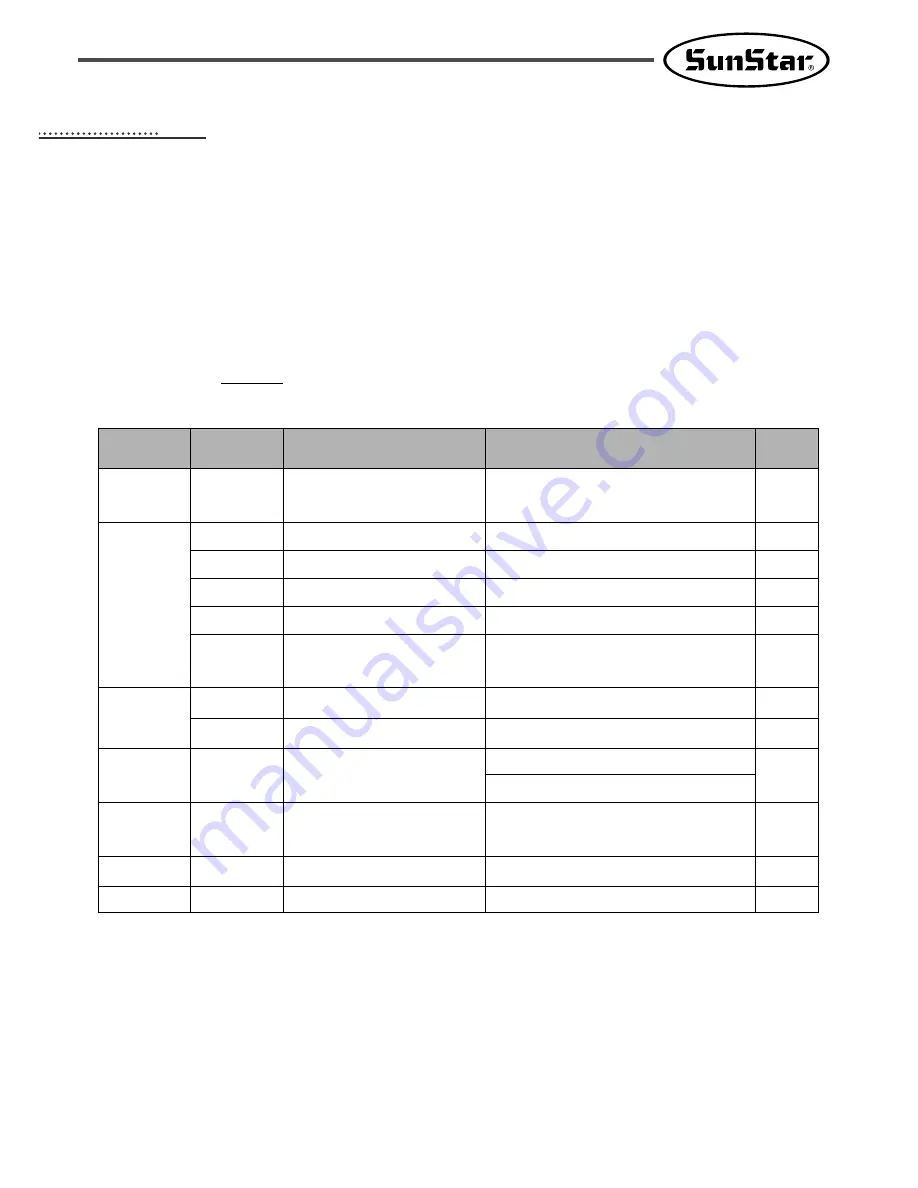
69
22
Maintenance
Code description) The 6-digit code appears on the screen as below. Please see the front two digits.
[02][0100]
※
Please cope with problems about each alarm code using the codes below when the error alarm occurs.
Alarm Code
Delete
Alarm
Alarm Name
Description
Data Read/Write error
Version update error
Main motor operation error
XY motor movement error
Lower shaft motor movement error
Rocking Motor movement error
Presser foot minute adjusting motor
movement error
Input device operation error
Output device operation error
Overvoltage error
Low-voltage error
Serial communication and CAN
communication error
CPU board operating and arithmetic error
Operation box operating error
Design & Update file Error
Main Motor Error
XY Motor Error
Hook Motor Error
Turning Motor Error
Pressure Foot Motor Error
Input Error
Output Error
Voltage Error
Serial Com. & Can Com. Error
CPU Error
Operation Box Error
[01][XXXX]
[02][XXXX]
[03][XXXX]
[04][XXXX]
[05][XXXX]
[06][XXXX]
[07][XXXX]
[08][XXXX]
[09][XXXX]
[OA][XXXX]
[OB][XXXX]
[OC][XXXX]
Design
Motor
Input
Output
Voltage
Communication
CPU
OP BOX
O
X
X
X
X
X
O
O
X
X
O
X
1) Alarm and Warning List [HT-Series Whole Aspect]
Alarm Code
Summary of Contents for SPS/E-5050 Series
Page 2: ......