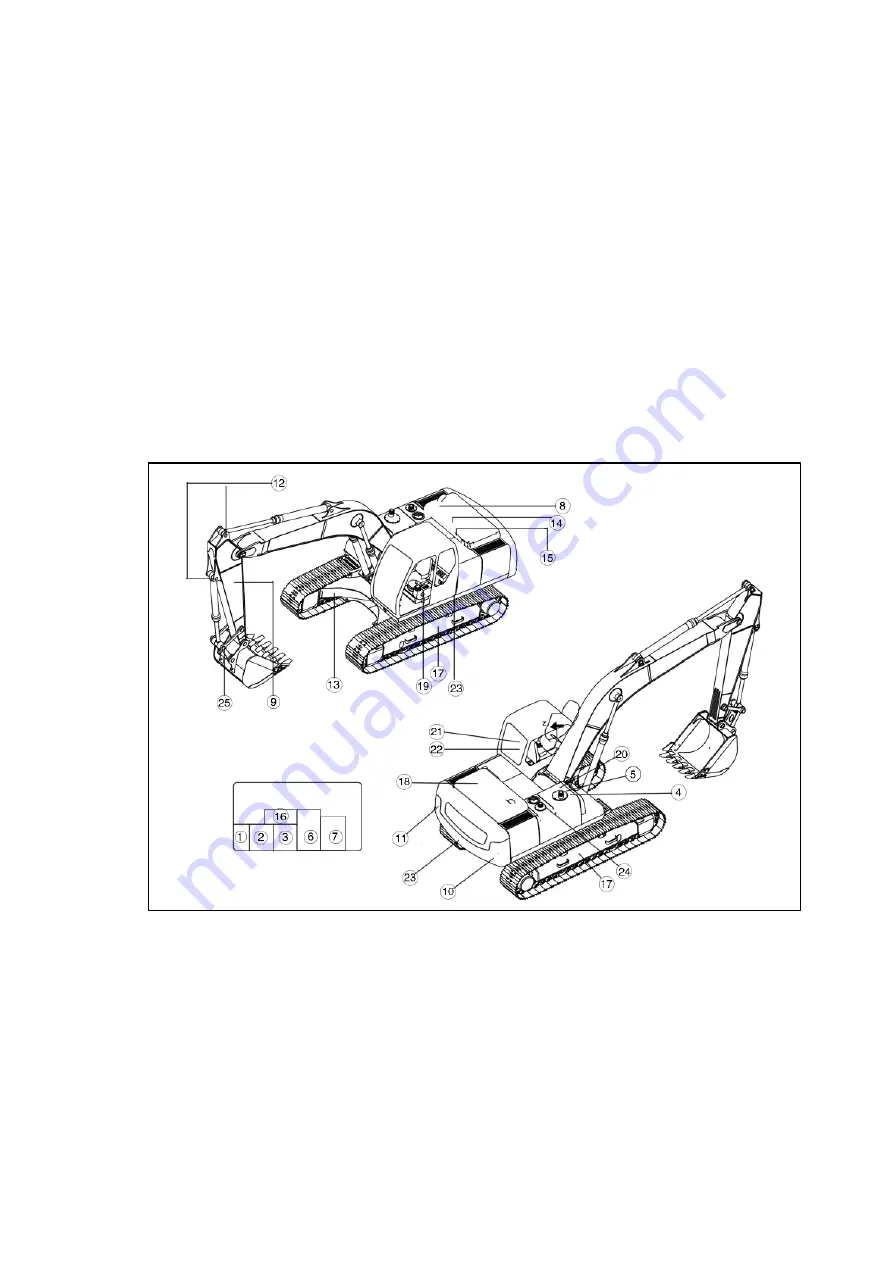
2
§1 SAFETY RULES
1.1 Safety labels
1.1.1 Location of safety labels
Fully understand the correct position and contents of safety labels in this machine.
To ensure that the content of labels can be read properly, be sure that they are in right place and
always keep them clean. When cleaning them, do not use solvents or gasoline. It may cause
labels to peel off.
There are also other labels in addition to warning labels. Handle these labels in the same way.
In case the labels are damaged, lost or not legible, replace them with new ones. For details of
the part number, refer to parts manual or actual label, and place an order with SUNWARD or
our authorized distributors.
Actual position of safety labels in the machine
Summary of Contents for SWE150F
Page 19: ...12 18 No unauthorized access label Warning Stay clear of operation area of working device...
Page 22: ...15 23 Gravity label 24 Hydraulic oil label 25 Greasing...
Page 151: ...144 4 4 9 Hose...
Page 193: ...186 5 Technical specification...
Page 197: ...190 5 1 4 Circuit diagram...
Page 199: ...192 5 1 6 Hydraulic diagram...
Page 204: ...197 5 2 4 SWE210F Circuit diagram...
Page 206: ...199 5 2 6 Hydraulic diagram...