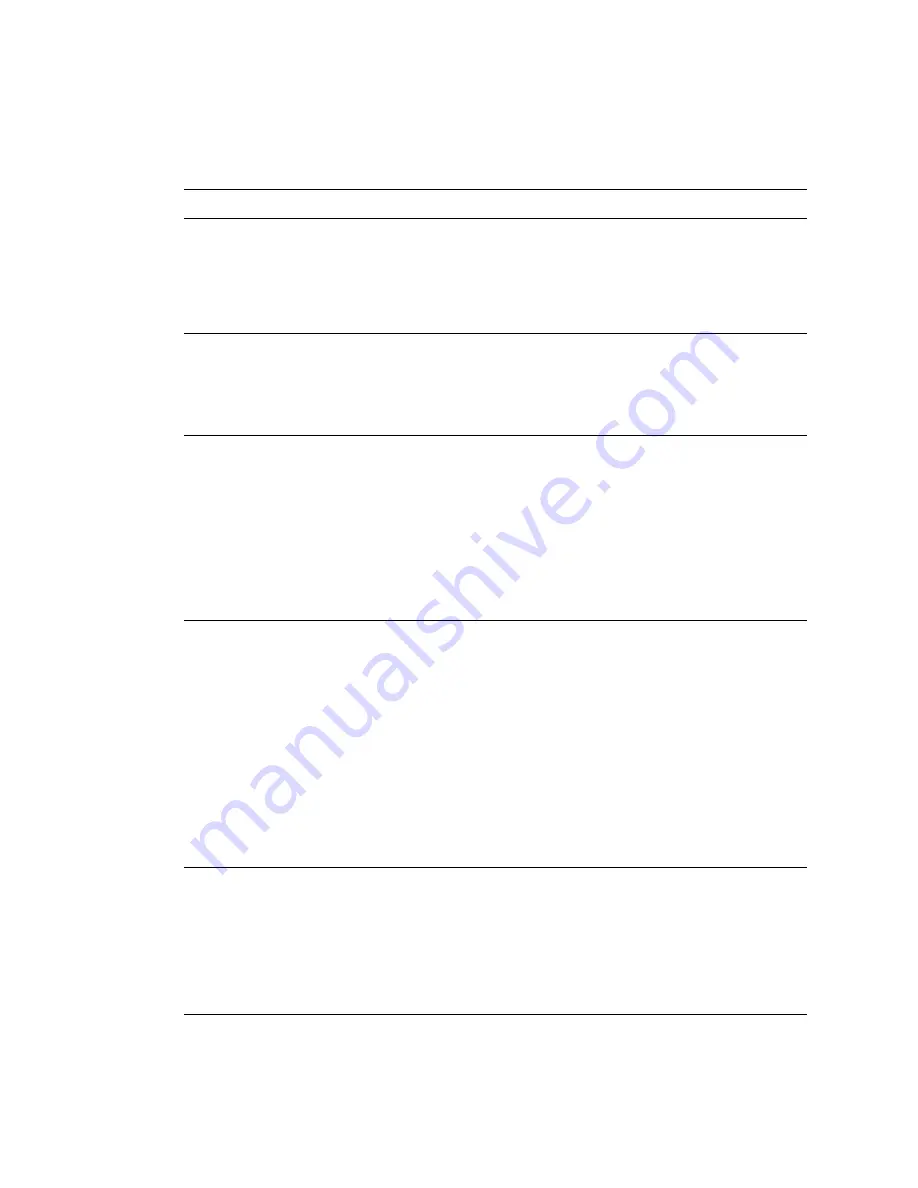
8
1.3
Guidelines and standards
The following guidelines and standards are of critical importance for the implementation of laser
scanner. Guidelines providing particularly relevant information for users of such systems are
marked with an asterisk (
*
).
Guideline / Standard
Designation
European Guidelines
98 / 37 / EG
Machine guideline
73 / 23 / EWG
Low voltage guideline
89 / 336 / EWG
EMC guideline
A Standards
ISO 12100-1 and 2
Safety of machinery - basic concepts
ISO 14121
Safety of machinery - principles for risk assessment
*
B1 Standards
ISO 13852
Safety of machinery - safety distances to prevent danger
zones being reached by the upper limbs
*
ISO 13849-1
Safety of machinery - Safety related parts of control
systems; Part 1: General principles for design
ISO
13855
Safety of machinery. The positioning of protective
equipment in respect of approach speeds of parts of the
human body
*
B2 Standards
IEC 60204-1
Safety of machinery - Electrical equipment of machines -
Part 1: General requirements
IEC 60825-1
Safety of laser products - Part 1: Equipment classification
and requirements
IEC
61496-1
Safety of machinery. Electro-sensitive protective
equipment. General requirements and tests
*
IEC
61496-3
Safety of machinery - Electro-sensitive protective
equipment - Part 3: Particular requirements for Active
Opto-electronic Protective Devices responsive to Diffuse
Reflection (AOPDDR)
*
C Standards
DIN EN 775
Industrial robots - Safety
*
DIN EN 1525
Safety of industrial trucks - Driverless trucks and their
systems
*
DIN EN 12895
Industrial trucks - Electromagnetic compatibility
Summary of Contents for SD3-A1
Page 1: ......
Page 12: ...12...
Page 40: ...40 Fig 5 4 5 Considering the maximum measurement distance when safeguarding an area...
Page 60: ...60 Fig 6 2 1 Example of a zone pair changeover for an AGV on a curved route...
Page 61: ...61 Fig 6 2 2 Example of zone pair changeover with combined with reducing speed of the AGV...
Page 101: ...101 13 13 Dimensional drawings of the SD3 A1...
Page 102: ...102 13 14 Dimensional drawings of the mounting system...
Page 106: ......