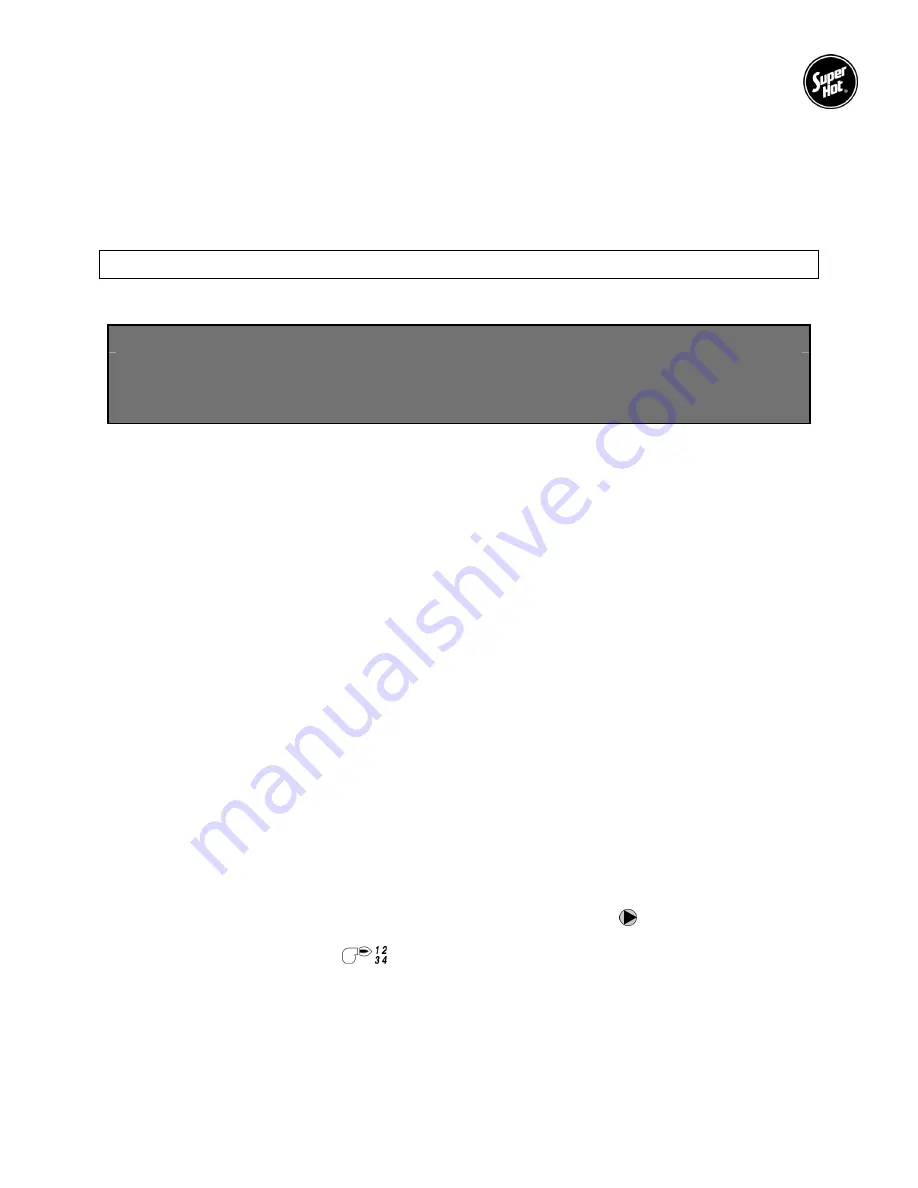
MSE Series Electric Boilers – Installation and Service Manual
9
b. Power Supply to Heaters
The supply cable has to be sized based on the amperage in Table 1 and the cables used.
Connect only specified line voltage and phase power to main terminal block on the control panel.
Strip wire ends before inserting into terminal block. Tighten terminal screw clamps. Attach ground
wire to ground terminal block on the control panel.
Startup Instructions
Section 4
4.1 WARNING
WARNING
The following instructions are intended as a guide for a Qualified Service Technician. Before
switching the power on, fill the system with water and vent air. Check for and repair any leaks
in the water piping.
4.2 STARTUP
a. Fill System
Figure 2 shows the suggested set-up for a make-up water supply using a pressure regulator (supplied
with “PS” package). Do not apply full line make-up water pressure to the system. Fill the system to
approximately 12 psi (cold water) if the expansion tank is pressurized at 12 psi. The expansion tank
should be sized to provide the system with enough volume for thermal expansion and contraction while
maintaining operating pressures within safe and reasonable limits. There should be no significant
pressure fluctuations in systems having both an effective automatic fill valve and a properly sized
expansion tank or expansion tank arrangement. The standard pressure relief valve supplied with the
boiler is rated at 30 psi, or as required by order, but the maximum working pressure cannot exceed 90 psi
for the electric boiler. Once the system is filled with water, all trapped air must be removed to avoid air
locks, which can reduce flow rate and cause thermal shock. Figure 2 also illustrates the connections to
the air purger (not supplied by manufacturer) and expansion tank in the line from the boiler to the
radiation units. Additional air purgers should be installed at high points in the system to assist in
removing air which can accumulate from the water supply line. All high points must be vented.
b. Startup Procedure
Perform the following procedure as a check for proper boiler and system operation:
1. Press and hold three keys found below the LCD screen of the controller until “Adjust” is displayed
(Figure 5). In adjust mode, enter the desired settings for your heating application (see BC-1 Boiler
Controller Manual for more information). (Note: This boiler is also equipped with a non-adjustable,
high-limit temperature device set at 239
°
F as safety limit control. The high limit temperature device
has an automatic reset function.)
2. Turn up all room thermostats above room temperature.
3. When power is supplied to the controller, the LCD displays “- - -“. When the thermostat calls for
heat, the pump will be energized immediately and the pump indicator, , will display on the LCD.
The “- - -“ screen is replaced with the boiler target temperature. Next, the three stages are energized
along with the stage indicator,
, in sequence and based on the user settings. Once the boiler
water temperature reaches the setpoint, the controller will regulate the boiler water temperature using
the three stages. The number of stages that switch on is based on the heating demand and user
settings. After all room thermostats are satisfied, the controller de-energizes the three stages, in
sequence, and then switches off the pump.
4. Current must be checked by a qualified electrician at the feeder panel and compared to the values
shown in Table 1.
5. Turn thermostats to the desired room temperature.