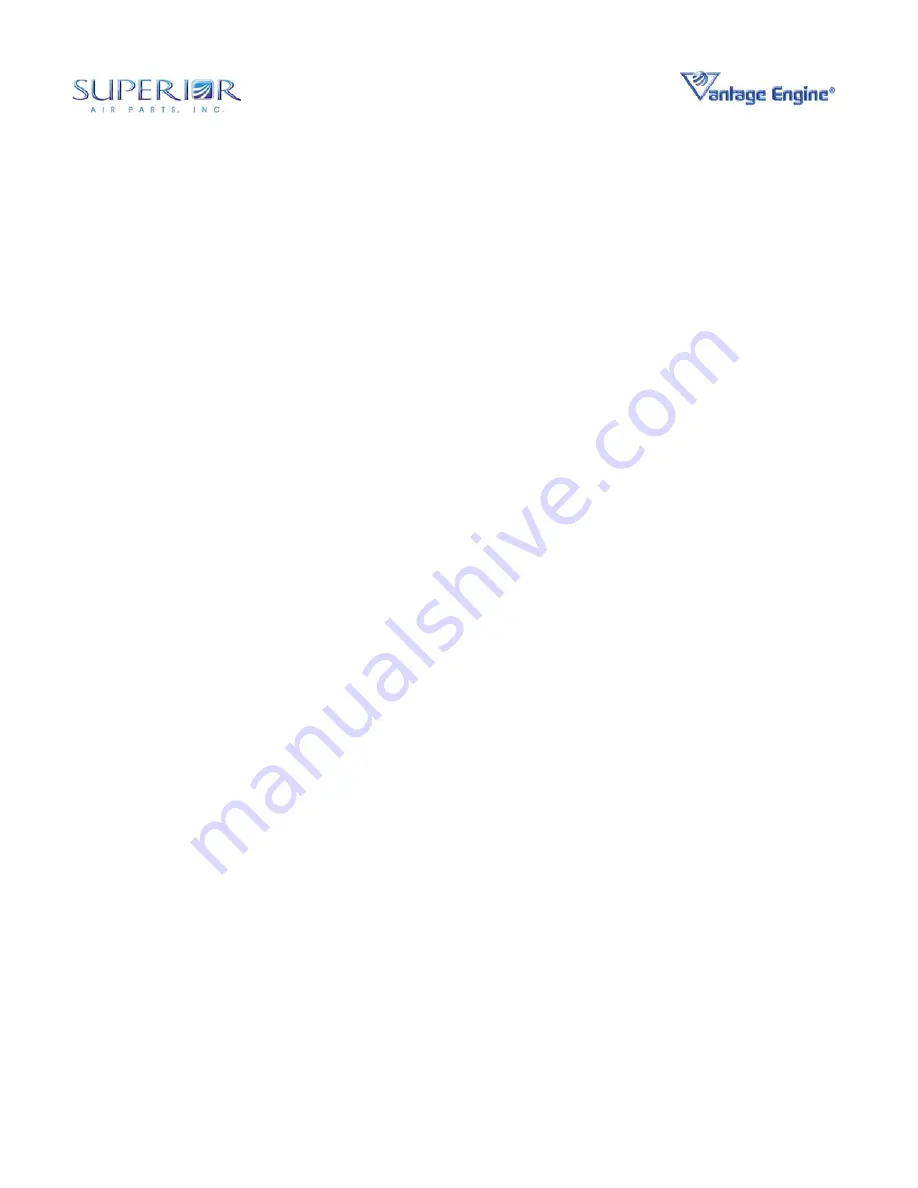
Installation & Operation Manual
O-360 and IO-360 Series Engines
13 Chapter 3 • Aircraft / Engine
© March 2004 Superior Air Parts Inc. Integration Considerations
Specification Data, the valve may be adjusted as
follows:
With the engine warmed up and running at 2000
RPM, observe the oil pressure gage reading. If
the pressure is above maximum or below
minimum specified limits, stop the engine and
turn the adjusting screw, with either a flathead
screwdriver or a 9/16 inch box wrench, inward
(clockwise) to increase pressure or outward
(counter-clockwise) to decrease pressure. See
Table 5 of the Model Specification Data for
specific oil pressure data.
(3.) Vernatherm and Oil Cooler
Automatic oil temperature control valves
(Vernatherm valves) are used to govern the flow
of oil through the external oil cooler. These
valves are set at the time of assembly and are
not serviceable by the operator. When the
engine is cool, the vernatherm valve is open and
oil is free to flow directly through the engine
without being routed through the external oil
cooler. As the oil temperature reaches its
desired limits however some or all of the oil is
routed through the oil cooler circuit.
The oil cooler circuit is the only part of the
lubrication circuit that is controlled by the
installation design. It is necessary to maintain
good hydraulic practices in the design of the oil
cooler circuit to minimize flow and pressure
losses. These include using large diameter
hoses and avoiding sharp bends and restrictive
couplings whenever possible. Flow and
pressure losses in the oil system not only cause
inefficiencies in the overall engine system but
also add to the potential for aeration during high
altitude flight.
C. Crankcase Ventilation
Pressure is generated within the crankcase
during normal engine operation primarily as a
result of piston ring blow-by. If the crankcase
pressure were not controlled nose seal and
other seal failures would occur leading to loss of
oil. Superior Vantage Engines utilize crankcase
breather circuits as a means of controlling
crankcase pressure. See Table 4 of the Model
Specification Data for specific measurements
defining crankcase pressures.
The installation design should include provisions
to connect a crankcase ventilation hose to the
engine breather fitting on the rear of the engine.
The purpose of this hose is to direct the
crankcase gas safely overboard. It is
recommended that an air-oil separator be used
to prevent oil entrained in the gas flow from
getting on the airframe. If an air-oil separator is
used, the oil drain may be connected into a
cylinder head drain back tube or other location
as approved by Superior Air Parts.
Care should be taken in the location of the
breather tube exit so as not to create a positive
or negative pressure in the breather circuit. A
positive pressure would serve to aggravate seal
leakage and a negative pressure could increase
the flowrate out of the crankcase and cause loss
of engine oil.
Superior recommends installation of an air-oil
separator as part of a vacuum pump installation.
The oil drain may be connected into a cylinder
head drain back tube or other location as
approved by Superior Air Parts.