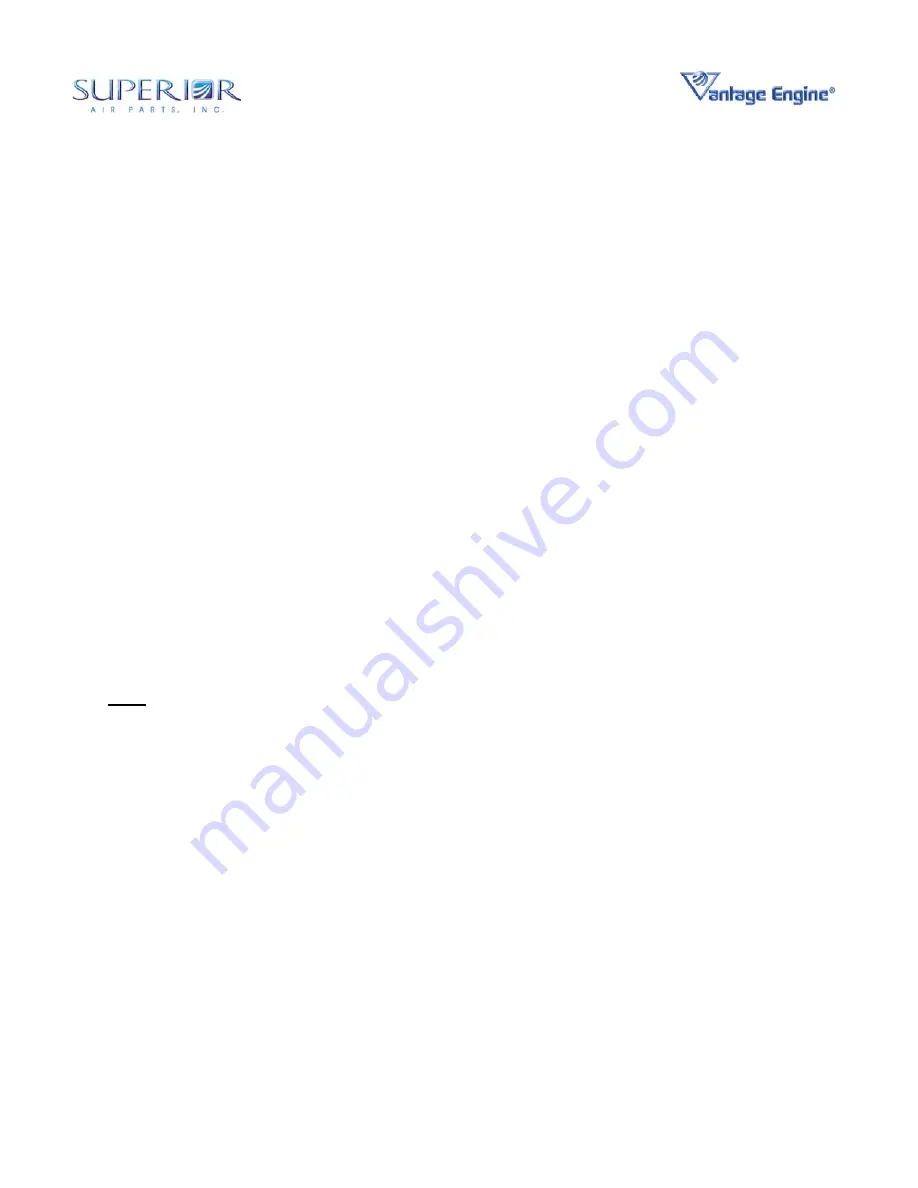
Installation & Operation Manual
O-360 and IO-360 Series Engines
1
© March 2004 Superior Air Parts Inc. Chapter 4 • Engine Installation
CHAPTER 4
Engine Installation
1. GENERAL INSTRUCTIONS
Superior Vantage Engines are carefully
packaged to prevent shipping damage and
preserved for extended storage. These
measures include the use of metal shipping
fixtures, isolation mounts and desiccant plugs
(when preserved for extended storage). These
items are not intended for further use and should
be discarded when the engine is unpacked.
Superior Air Parts recommends particular
attention to the discard of hardware used to
secure the engine during shipment and in the
attachment of the engine to the shipping fixture.
This hardware is not suitable for the structural
requirements of an engine installation and it is
important to verify that it is not used in that
regard.
A lifting eye bracket is installed on the
“backbone” of each engine crankcase for the
purposes of hoisting the engine.
Note: This is the only means by which the
engine should be lifted. Lifting the engine by
any other means may result in damage to the
engine and is not covered by warranty.
The following includes a discussion of general
engine installation practices. This discussion
should be used IN ADDITION TO the applicable
requirements of the FARs.
2. PREPARING ENGINE FOR SERVICE
If the engine has been preserved for extended
storage, remove the shipping plugs installed in
the lower spark plug holes and turn the
crankshaft through at least twice in order to
remove the cylinder preservation oil from the
cylinders. Remove the shipping plugs installed
in the upper spark plug holes and inspect the
cylinder bores for rust or contamination. Contact
Superior if any abnormal condition is noted.
Engines that have been subjected to a cold
environment for long periods of time should be
placed into at least 70ºF atmosphere for 24
hours or more before attempting to drain the
preservative oil. Alternatively, the cylinders may
be heated with heating lamps before attempting
to drain the engine.
Remove exhaust port protective plugs. Service
the lubrication system in accordance with
instructions from Chapter 5, Section 3 A.
Remove the shipping plate from the propeller
governor pad as required for governor
installation. Lubricate the governor shaft splines
with engine oil, install a new gasket and then
install the propeller governor control. Attach
with plain washers, new lock washers and
torque the nuts to 204 in-lbs.
Align the spline of the governor drive gear and
be sure that the governor is fully seated to the
adapter prior to installing the attaching
hardware. This eliminates the possibility of
misalignment.
Optional accessories such as vacuum pumps,
hydraulic pumps, etc., may be installed on the
accessory drive pads located on the rear of the
accessory housing. Remove the accessory
drive covers and install new gaskets.
Install accessories in accordance with the
manufacturer’s instructions.
Install all airframe manufacturers’ required
cooling baffles, hoses, fittings, brackets and
ground straps in accordance with airframe
manufacturer’s instructions.