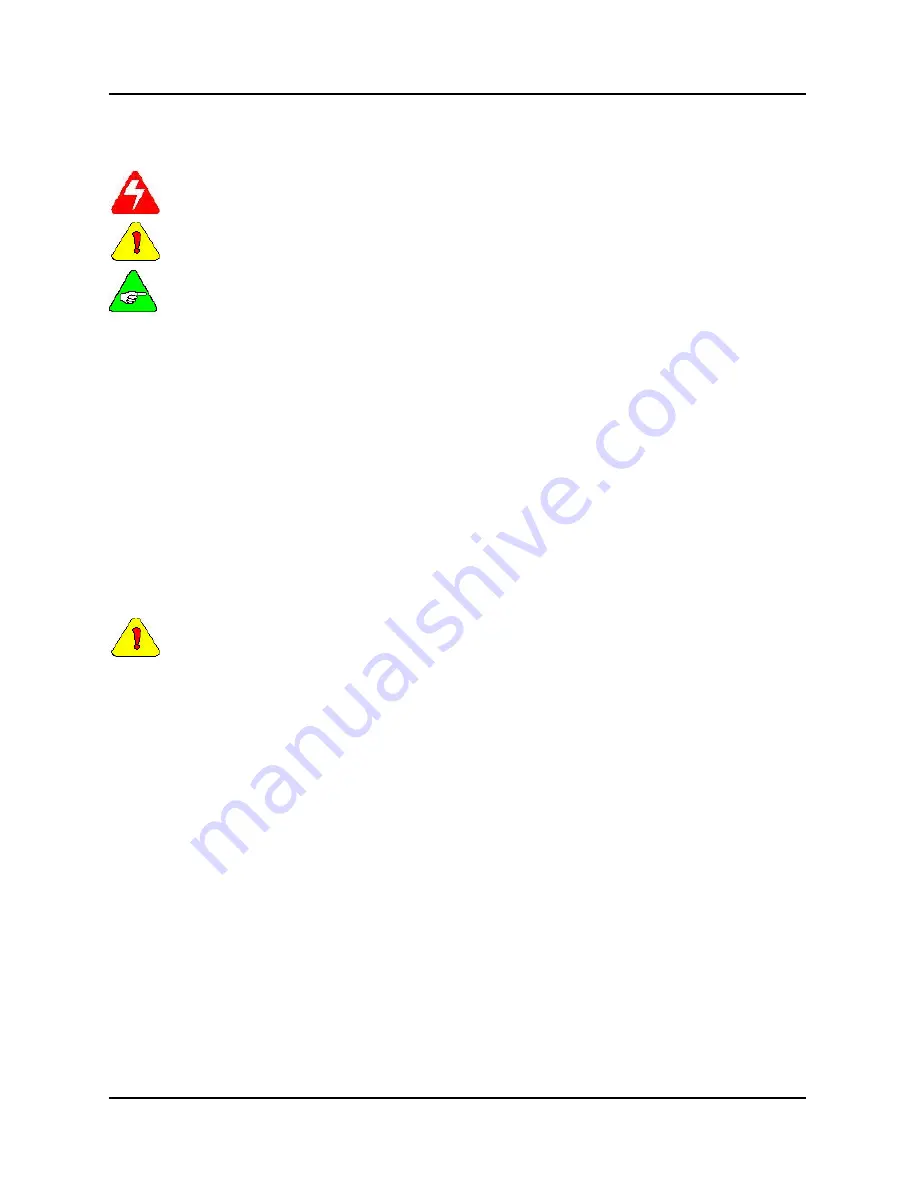
Danaher Motion Superior Electric
SS2000MD4
3
400030-043 Rev G
Safety
Safety symbols used in this manual are:
Warning
Alerts users to potential physical danger or harm. Failure to follow
warning notices could result in personal injury or death.
Caution
Directs attention to general precautions, which if not followed, could result
in personal injury and/or equipment damage.
Note
Highlights information critical to your understanding or use of the product.
Instructions
Only qualified personnel should install or perform servicing procedures on this equipment.
Do not
operate the unit without the enclosures in place as voltage present in this unit can cause serious or
fatal injury.
Before performing any work on the unit, allow at least five minutes for the capacitors to
discharge fully.
Voltage is present on unprotected pins when unit is operational.
The "PWR ON" LED must be off for approximately 30 seconds before making or breaking
the motor connections.
Motors powered by these drives may develop extremely high torque. Disconnect AC power to
these drive before doing any mechanical work.
This unit is designed for 115 VAC input only (see Section 4.2,
Electrical Specifications).
Warranty And Limitation Of Liability
Danaher Motion (the "Company") warrants to the first end user purchaser (the "purchaser") of
equipment manufactured by the Company that such equipment, if new, unused and in original
unopened cartons at the time of purchase, is free from defects in material and workmanship under
normal use and service for a period of one year from date of shipment from the Company's factory or
a warehouse of the Company in the event that the equipment is purchased from the Company or for a
period of one year from the date of shipment from the business establishment of an authorized
distributor of the Company in the event that the equipment is purchased from an authorized
distributor.
THE COMPANY'S OBLIGATION UNDER THIS WARRANTY SHALL BE STRICTLY AND
EXCLUSIVELY LIMITED TO REPAIRING OR REPLACING, AT THE FACTORY OR A SERVICE
CENTER OF THE COMPANY, ANY SUCH EQUIPMENT OR PARTS THEREOF WHICH AN
AUTHORIZED REPRESENTATIVE OF THE COMPANY FINDS TO BE DEFECTIVE IN MATERIAL
OR WORKMANSHIP UNDER NORMAL USE AND SERVICE WITHIN SUCH PERIOD OF ONE
YEAR. THE COMPANY RESERVES THE RIGHT TO SATISFY SUCH OBLIGATION IN FULL BY
REFUNDING THE FULL PURCHASE PRICE OF ANY SUCH DEFECTIVE EQUIPMENT
. This
warranty does not apply to any equipment which has been tampered with or altered in any way,
improperly installed or has been subject to misuse, neglect or accident.
Summary of Contents for SLO-SYN SS2000MD4
Page 20: ...Danaher Motion Superior Electric SS2000MD4 20 400030 043 Rev G...
Page 21: ...Danaher Motion Superior Electric SS2000MD4 21 400030 043 Rev G...
Page 22: ...Danaher Motion Superior Electric SS2000MD4 22 400030 043 Rev G...
Page 23: ...Danaher Motion Superior Electric SS2000MD4 23 400030 043 Rev G...
Page 24: ...Danaher Motion Superior Electric SS2000MD4 24 400030 043 Rev G...
Page 25: ...Danaher Motion Superior Electric SS2000MD4 25 400030 043 Rev G...
Page 26: ...Danaher Motion Superior Electric SS2000MD4 26 400030 043 Rev G...
Page 27: ...Danaher Motion Superior Electric SS2000MD4 27 400030 043 Rev G...
Page 28: ...Danaher Motion Superior Electric SS2000MD4 28 400030 043 Rev G...
Page 29: ...Danaher Motion Superior Electric SS2000MD4 29 400030 043 Rev G...
Page 30: ...Danaher Motion Superior Electric SS2000MD4 30 400030 043 Rev G...
Page 31: ...Danaher Motion Superior Electric SS2000MD4 31 400030 043 Rev G...
Page 32: ...Danaher Motion Superior Electric SS2000MD4 32 400030 043 Rev G...
Page 33: ...Danaher Motion Superior Electric SS2000MD4 33 400030 043 Rev G...
Page 34: ...Danaher Motion Superior Electric SS2000MD4 34 400030 043 Rev G...