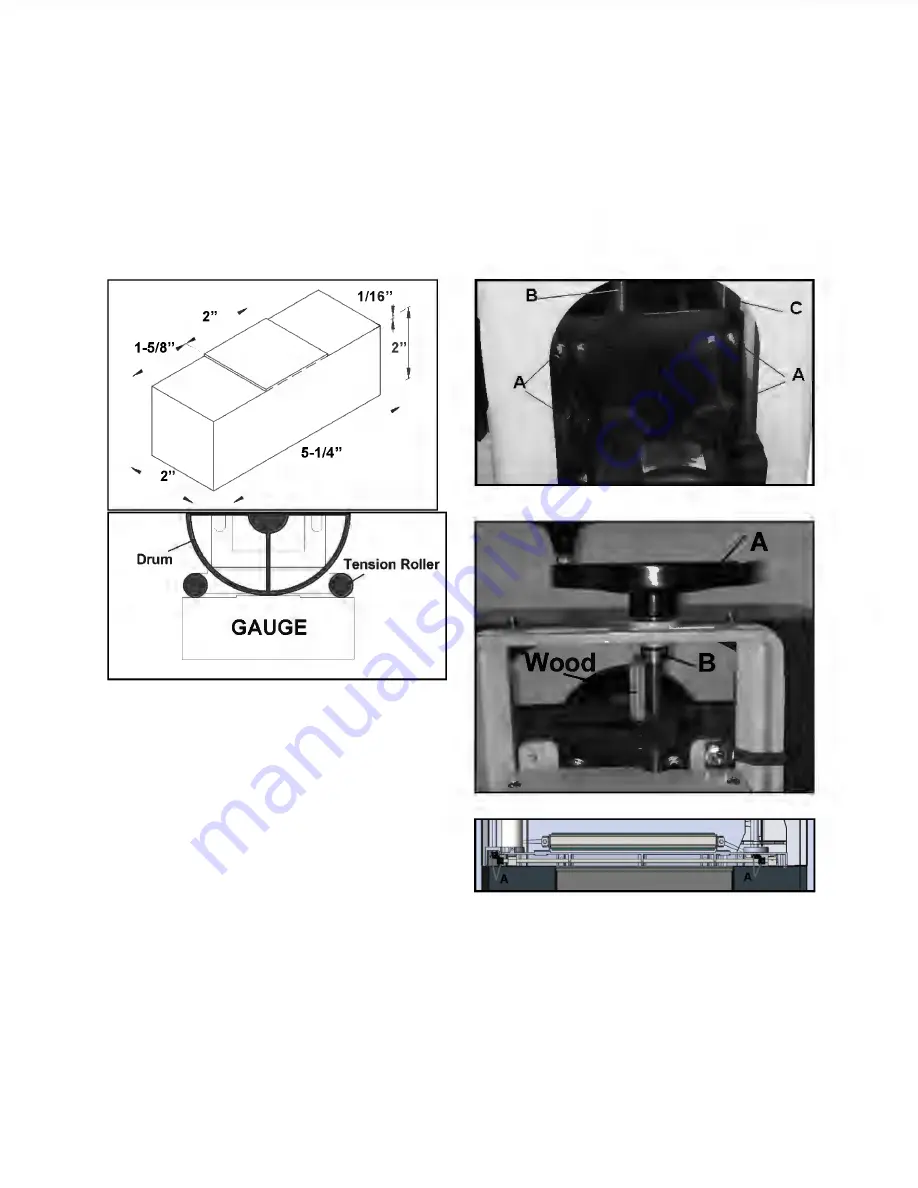
14
8. Move gauge blocks to rear drum and
tighten the other four hex nuts. Rotate the
rear drum by hand to make sure it lightly
contacts gauge blocks on both ends after
tightening the nuts.
9. Install abrasive strips, close dust cover,
tension the belt and reinstall the belt cover.
If there still is a snipe mark left on pieces being
sanded, loosen tension roller spring retain screws
(A, Figure 20) on both ends of rear drum and/or
raise rear drum to keep rear drum just slightly
lower than front drum.
Figure 21
Adjusting height control
If the height control mechanism does not operate
smoothly or there is excessive vertical movement
or deflection of the drum carriage, perform the
following adjustments.
1. Tighten all four lock nuts (A, Figure 22) and
then loosen them 1/8 to 1/4 turn. If the lock
nuts are set too tight, height control will not
operate easily. If the lock nuts are too loose,
excessive deflection or binding may occur.
2. Thoroughly lubricate the mating surfaces of
the motor mount slide (C, Figure 22), and the
height adjustment screw (B, Figure 22).
3. Push height adjustment handwheel (A, Figure
23) downward to set firmly on housing.
Loosen set screws of shaft collar (B, Figure
23). Slide shaft collar upward against housing
so that all vertical free play of height
adjustment screw is eliminated. Use a block of
wood on top of the motor mount plate and
under collar. Raise the motor mount plate by
rotating the handwheel to help remove free
play. Lubricate around washers beneath
handle and above collar.
4. If the height adjustment mechanism still feels
rough, check the miter gear alignment on the
underside of the base. The miter gears (A,
Figure 24) can be adjusted on their shafts by
loosening the set screws on the gears. Check
and adjust so that the gear mesh is not too
tight or too loose, and that the gear teeth align
with the opposing gear.
Figure 22
Figure 23
Figure 24
Poly-v belt adjustment/ replacement
To adjust tension or replace the poly-v belt:
1. Remove belt guard by removing two screws.
2. Loosen the four cap screws (A, Figure 25)
securing motor to motor plate.
3. Push down on motor to de-tension belt, and
remove belt from around pulleys.
Summary of Contents for 913003
Page 25: ...25 Exploded View Machine Body Assembly...
Page 29: ...29 Exploded View Drum Head Assembly...
Page 32: ...32 Exploded View Conveyor and Motor Assembly 33 1Ph...
Page 39: ...39 Notes...