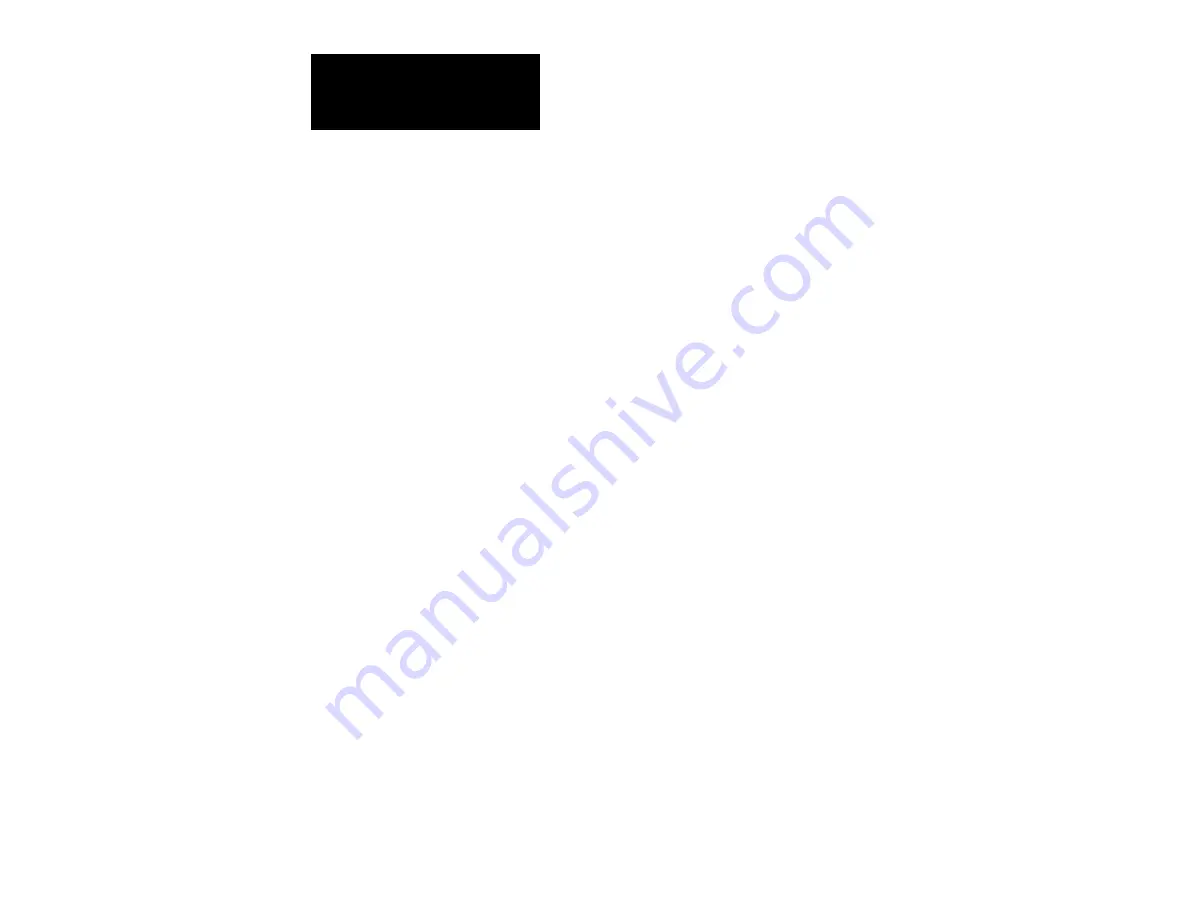
7. Do not move the winching or
winched vehicle to assist in
pulling the load. This may result
in overloading the winch and/or
the winch mounting system.
8. Do not allow the wire rope to
pile up on one side of the drum.
Doing so will damage the wire
rope, and potentially the winch.
If the rope piles up, stop the
operation, secure the load, and
change the position of the
winching vehicle so it pulls in a
direct line. If it is not practical to
move the winching vehicle
install a pulley block in the line
to act as a guide.
9. When the winching operation is
complete and the load is in posi-
tion, use alternate means to
secure the load for transport
(i.e., chains, or nylon strap
tie downs). The winch is not
intended for holding a load dur-
ing transport. The winch and/or
wire rope may break due to
shock loads greater than the rat-
ing generated during transport.
10. Use caution when powering out
or lowering a load down a ramp
or incline. Stay clear of, and
keep people, pets and property
out of the path of the load
being lowered. The winch‘s
hydraulic control circuit must
make provisions for applications
involving lowering of loads (see
the hydraulic system/control cir-
cuit section of the manual).
ROUTINE MAINTENANCE
The SUPERWINCH H11/13/15P is
designed to provide years of trou-
ble free operation. As with any
machine, periodic routine mainte-
nance is required. Use the following
as a guideline to keep your winch in
top operating condition.
THE FOLLOWING ITEMS SHOULD
BE CHECKED WEEKLY. A DAILY
INSPECTION OF THESE ITEMS
SHOULD BE PERFORMED ON
WINCHES IN FREQUENT USE.
Check all bolts, screws and other
fasteners mounting the winch and
its accessories, to be sure they have
not vibrated loose and fallen out.
Check the wire rope for damage.
Replace as required. Check the
winch for hydraulic fluid leaks
around the gearbox and brake. At
the same time check the casting for
any cracks or other signs of dam-
age. Be sure the freespool mecha-
nism is operating properly. Check
the hydraulic control circuit for
proper function. Check hoses for
deterioration. Check all connections
and fitting for leaks.
THE FOLLOWING ITEMS SHOULD
BE CHECKED MONTHLY. A WEEK-
LY INSPECTION OF THESE ITEMS
SHOULD BE PERFORMED ON
WINCHES IN FREQUENT USE.
Check the brake. Follow the guide-
lines listed in the section of this
manual describing the brake
(Page 12).
T R O U B L E
S H O O T I N G A N D
M A I N T E N A N C E G U I D E
14
After 50 hours of winching or
annually:
Change gearbox grease (approxi-
mately 1/4 lb. Super Lube
Superwinch Part No. 90-15020).
Check brake function. Lubricate
freespool mechansim with light oil.
Check tightness of mounting bolts
and hydraulic connections.
LUBRICATION
1. The winch gearbox is grease
lubricated with Super Lube at the
factory. If the winch is torn down
and washed out use SUPER-
WINCH grease 90-15020 to
repack.
2. All freespool mechanism parts
require periodic regreasing to
keep them operating properly.
Any high quality white automo-
tive grease is acceptable.
Superwinch grease 90-15020 is
recommended. In cold climates a
light oil should be substituted
for grease.
HYDRAULIC SYSTEM
TROUBLE SHOOTING
Most hydraulic system failures fol-
low the same pattern — a gradual
or sudden loss of pressure or flow
with a resulting loss of motor
power. Any one of the system‘s
components may be at fault. By
following step-by-step procedures,
the trouble can be isolated in a
short time.
A. System Inoperative
1. No hydraulic fluid in system:
insufficient fluid in system. Fill
system and check for leaks.
2. Wrong hydraulic fluid in system:
Refer to manufacturer‘s specifi-
cations. Change fluid.
3. Filter dirty or clogged: Drain
fluid and replace filter or filter
element.
4. Fluid line restriction: Fluid lines
dirty or collapsed. Clean or
replace.
5. Air leaks in pump suction line:
Repair or replace as necessary.
6. Worn or dirty pump: Clean,
repair or replace. Check align-
ment. Check for contaminated
oil. Drain and flush system.
7. Badly worn components:
Examine and test for external
leakage. Replace faulty compo-
nents. Check for cause of wear.
8. Leakage: Check all components,
particularly the relief valve, for
proper setting. Refer to techni-
cal manuals.
9. Excessive load: Check unit speci-
fications for load limits.
10. Slipping or broken pump drive:
Repair or replace belts, cou-
plings, etc. Check for proper
alignment of tension.
15