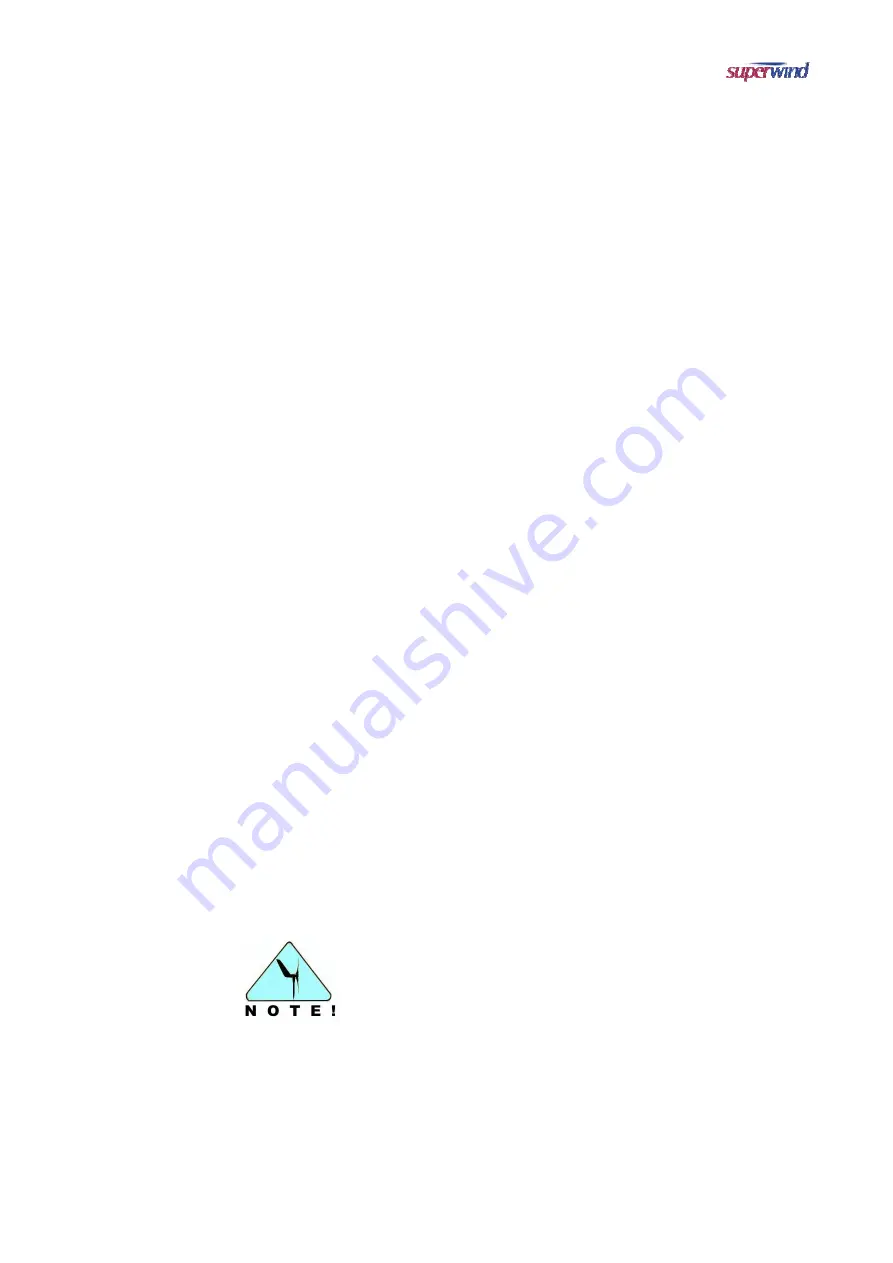
V 01-2017
www.superwind.com
13
4.2 Technical
data
nominal power...................................350 W
nominal wind speed ..........................12,5 m/s
cut in wind speed ..............................3,5 m/s
cut off wind speed .............................none
rotor diameter....................................1,20 m
number of blades ..............................3
blade material ...................................carbon fibre reinforced plastics
rotor speed........................................500 – 1300 rpm
generator ..........................................permanent magnet 3-phase with rectifier
magnets
Neodymium
nominal voltage.................................12 V DC or 24 V DC
speed regulation ...............................rotor blade pitch
power regulation ...............................rotor blade pitch
brake .................................................dynamic, short circuit
weight................................................11,5 kg
rotor thrust (operation) ......................70 N (15.7 lbf)
rotor thrust (extreme wind speed).....220 N (49.5 lbf)
4.3
Functional description / Special features
The
Superwind
, like all wind turbines, uses part of the kinetic energy of the wind
and converts it into electricity.
The power is approximately proportional to the cube of the wind speed - i.e.
doubling the wind speed results in eight times higher power output. Therefore,
power from the wind at low wind speeds produces very little energy. However, as
the wind speed increases exponentially, high pressure suddenly impacts the
turbine and all of its mechanical components. During high wind events,
conventional wind turbine technology resulted in the turbine going into an “over-
speed” condition, damaging both internal electrical components as well as the
blades themselves.
To design the
Superwind,
special technologies were developed in order to
achieve optimum power output for a wide wind speed range, as well as maintain
maximum safety in high wind or storm conditions. The following technology has
been incorporated into the Superwind to achieve this performance.
a) The rotor blades were developed using modern computerized calculation and
simulation methods. The airfoil had been wind tunnel tested and was specifically
developed for small size rotors.
Relatively broad rotor blades combined with a special pitch angle produces a
high start-up torque, enabling the rotor to start at only 3.5 m/s wind speed.
Optimum start-up performance will be reached after a
mechanical run-in period of the bearings and their seals. This
‘break-in’ period will vary depending on the winds speed and
hours the turbine is left “on” in windy conditions.
When using the
Superwind
for battery charging, do not mistake rotor start-up for
the start of charging. The wind speed required to start charging the battery
depends on the battery charge load at the time and might be slightly higher than
the rotor start-up wind speed.
The term ‘cut in speed’ describes when the turbine can start producing power to
charge your batteries. This is a higher wind speed than the ‘start up wind speed’,
a lower wind value where your turbine may spin, but will not be producing power.
Summary of Contents for 350 12V
Page 1: ...www superwind com Superwind 350 12V 24V Manual North Central and South America regions 01 2017...
Page 2: ...V 01 2017 www superwind com 1 Page intentionally left blank...
Page 52: ...V 01 2017 www superwind com 51 ATTACHMENT A Stop Switch Mounting Guidelines...
Page 53: ...V 01 2017 www superwind com 52 STOP SWITCH Mounting Guidelines Manual 01 2017...
Page 60: ...V 01 2017 www superwind com 59 ATTACHMENT B Superwind Charge Regulator 12V Marine...
Page 61: ...V 01 2017 www superwind com 60 Charge Regulator 12V Marine Instructions Manual 01 2017...
Page 70: ...V 01 2017 www superwind com 69 ATTACHMENT C Superwind Charge Regulator 24V Marine...
Page 71: ...V 01 2017 www superwind com 70 Charge Regulator 24V Marine Instructions Manual...