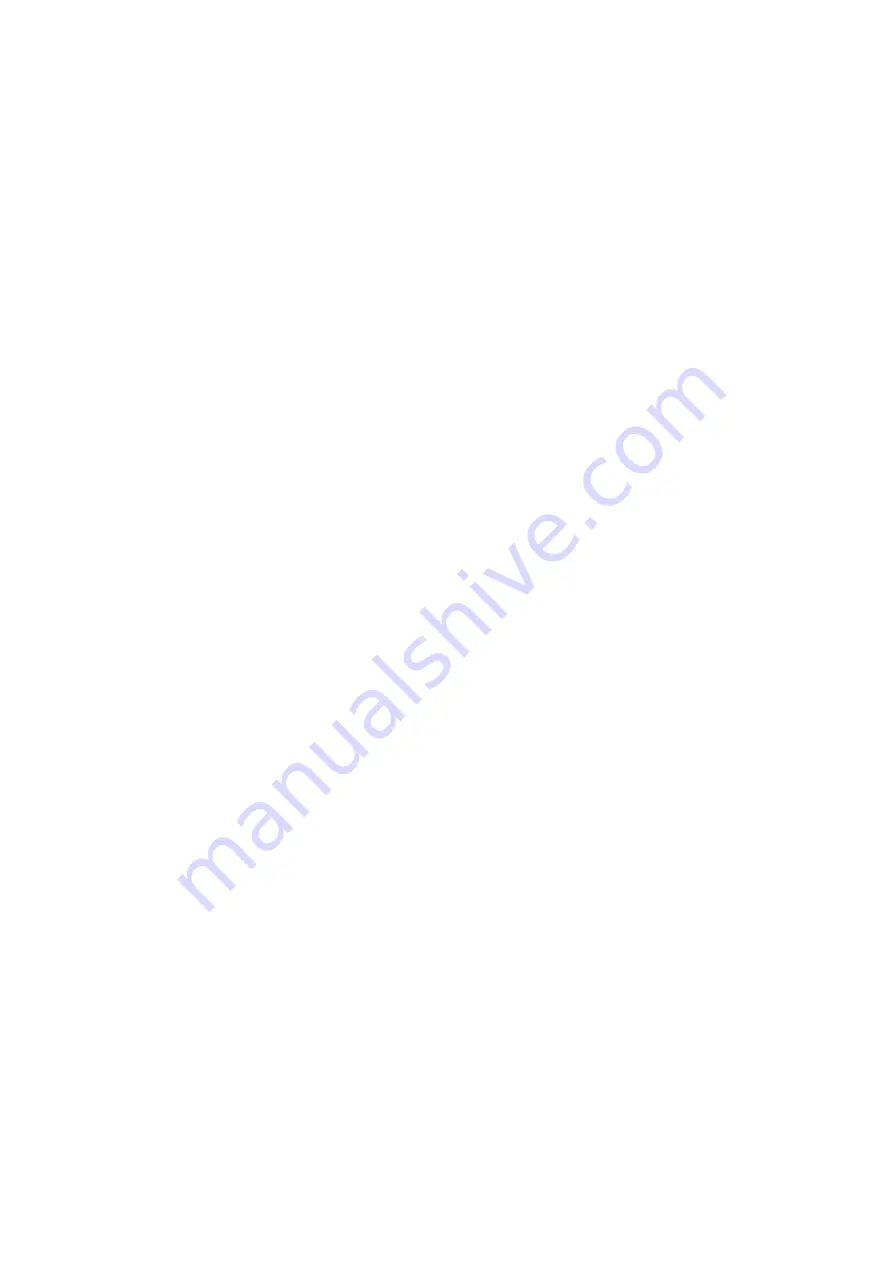
18
Testing
Swagelok recommends that the regulator be tested for seat and shell leakage to atmosphere. A well
performing regulator will not show any indication of leaking. If any evidence of a leak is identified this must be
rectified. Any damaged components must be replaced.
Seat Leak Test
1. Ensure there is sufficient supply pressure to the regulator to be able to perform the tests.
2. Ensure any downstream shutoff valves are open.
3. Set the regulator to 14.5 psig (1 bar) then close the supply shutoff valve.
4. Monitor the inlet pressure and/or use liquid leak detector on the outlet port. A drop in inlet pressure over
time or bubbles in the leak detector indicates a seat leak.
5. Repeat the procedure with the highest set pressure suitable for the regulator and system.
Shell Leak Test
1. Set the regulator to the open position (i.e. ensure the adjusting screw is fully backed off counterclockwise).
2. Close the downstream shutoff valve.
3. Maintain an inlet pressure of approximately 14.5 psig (1 bar) on the regulator. Measure the outlet pressure
to ensure this also reads the same value.
4. Using liquid leak detector, check for bubbles at the spring housing to body interface, body plug to body
interface and the spring housing weep hole.
5. Repeat the procedure with the highest inlet and outlet pressure applicable for the regulator and system.
Summary of Contents for BSH 10 Series
Page 10: ...10 BS H Series Exploded View Fig 1 ...
Page 11: ...11 BS H 10 Series Diaphragm Sensing Section View Fig 2 ...
Page 12: ...12 BS H 10 Series Piston Sensing with Anti Tamper Section View Fig 3 ...
Page 13: ...13 BS H 15 Series Diaphragm Sensing Section View Fig 4 ...
Page 14: ...14 BS H 15 Series Piston Configuration Control Range 5 Fig 5 ...