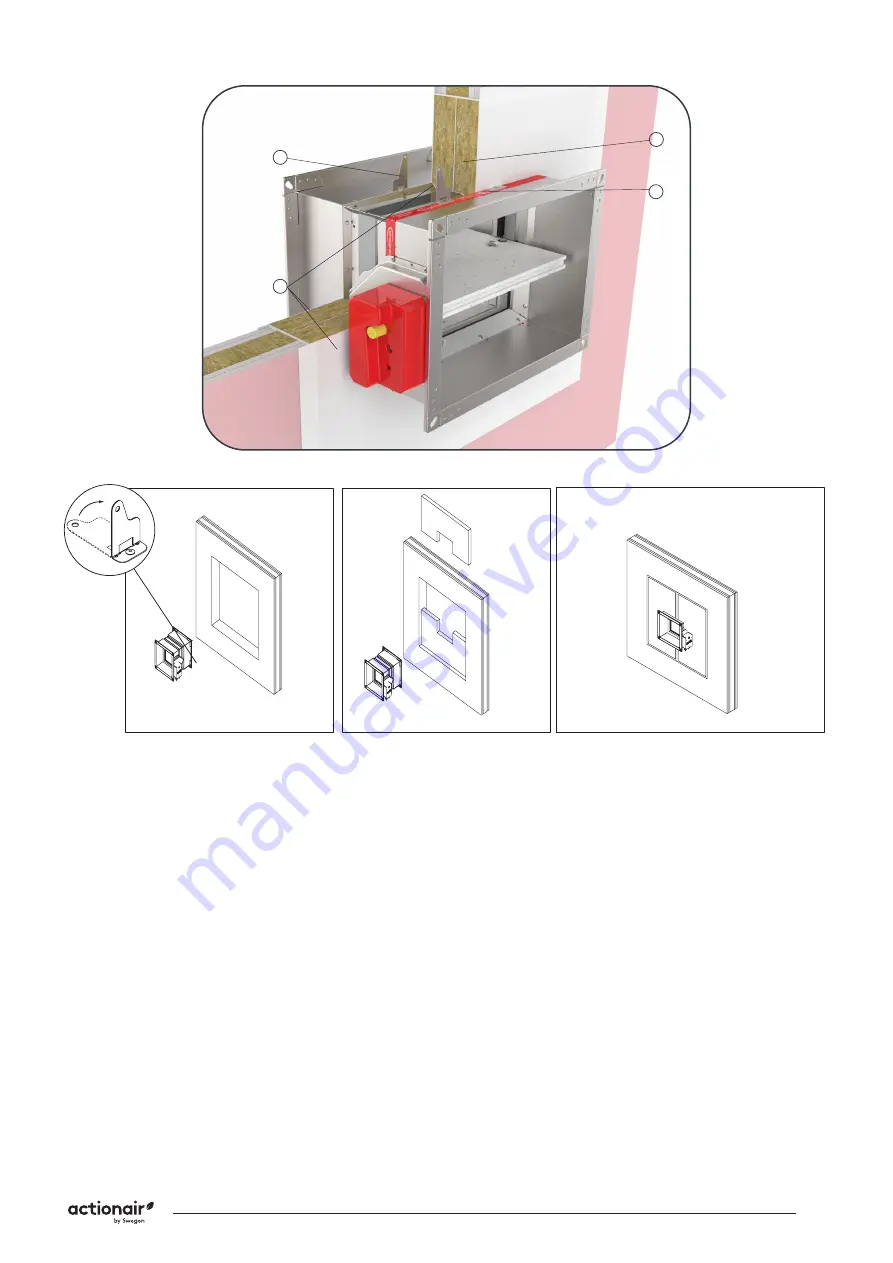
9
20210615 - L00010 Swegon reserves the right to alter specifications.
ThermShield Standard Square/Rectangular Installation Guide
Flexible wall installation
(Fire Batt)
Damper blade must be closed during installation!
The wall is composed of 2x2 plasterboard boards,
12,5mm thick, installed on a steel frame construction. The
interior of the wall is filled with mineral wool (
≥
100 kg/
m³).
Installation material: mineral wool (
≥
140 kg/m³) and fire
protection coating. The minimum thickness of the wall is
100mm.
1.
Recommended wall opening for fire damper
installation is
B(H) + 200mm, but openings from B(H) +
80…300mm can also be used. Bend the fixing bracket
(1) 90°.
2.
Insert fire damper into wall
to the wall limit mark (7) on
the damper.
3. Fill the space between casing and wall, close with two
layers of mineral wool (5)
(density 140 kg/m³ or more,
50 mm thick, coated on one side).
Seal the connections of mineral wool with intumescent
(6) fire resistant sealant. Mineral wool and damper casing
must be coated with 2mm thick fire protection coating.
Damper casing should be coated up to profile flanges.
Minimum seperation between fire dampers, either next
to each other or ceiling/wall, should be 30 mm between
them. See page 18.
**Fire Batt installations adjacent to ceiling or wall require
a suspension for the fire damper.
Test the operation of the damper blade!
Ensure that the damper is sufficiently supported!
1
5
6
7
1
2
3