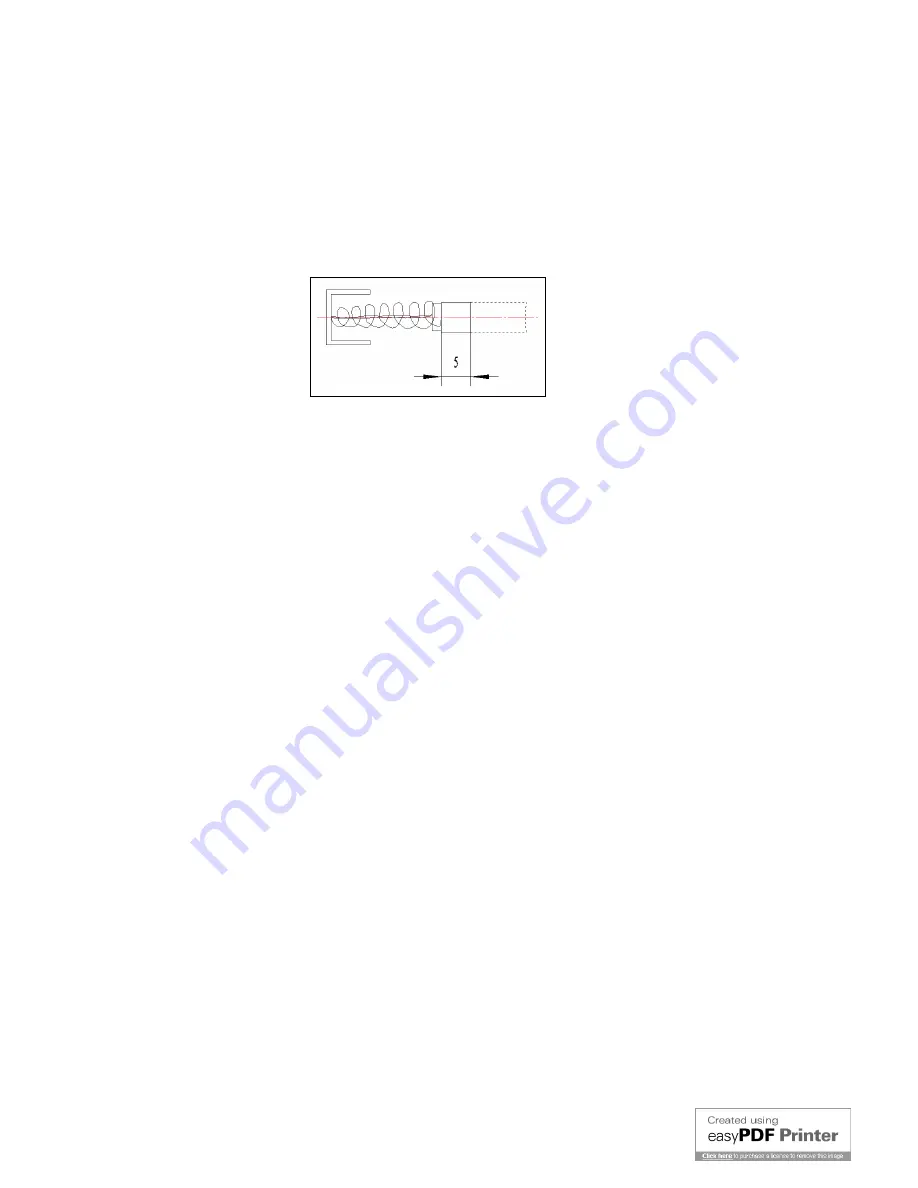
11
- Loosen brush holder (A) and gently remove brush from motor.
- Replace brushes if spring (B) is damaged.
- Replace brushes if carbon is worn.
- Replace brushes and tighten brush holder.
REPLACING THE CARBON BRUSHES
- Regularly check the carbon brushes and replace them when they are shorter than about 5mm.
Refer to Figure 9
- Replace the carbon brushes as a pair.
- Keep the carbon brushes clean, allowing them to move freely in the brush holders.
Figure 9
INSPECTION OF THE BLADES
- Keep the blades sharp. The dull blades will increase the damage of kickback. For grinding the blades with the
manual sharpening holder: firmly mount the blades on the sharpening holder and adjust so that the two blades
contact the stone at the same time.
- The limit of re-sharpening is 4 mm.
- Replace blades as a pair.
- Replace them of the same dimensions and weight or the function for planning and cutting will be affected and
even will get the machine damaged.
CLEANING & LUBRICATION
- Periodic or regular inspections are required to ensure that the machine is in proper adjustment, that all screws
are tight, that belts are in good condition, that dust has not accumulated in the electrical enclosures, and that
there are no worn or loose electrical connections.
- Always keep clean the feed roller section, table roller section, chip cover section, and other threaded sections
to prevent chips and other dirt from attaching.
- Occasionally lubricate the sliding sections.
- Never let water or oil into the inside of motor.
- Buildup of sawdust and other debris can cause your machine to plane inaccurately. Periodic cleaning is not
only recommended but mandatory for accurate planning.
- Close-fitting parts, such as the cutter head slot and gibs, should be cleaned with a cloth or brush and
non-flammable solvent, and freed from clinging foreign matter.
- Remove resin and other accumulations from feed rollers and table with a soft rag and non-flammable solvent.
- Periodically check all the chains for proper tension and adjust accordingly if required.
- The table should be kept clean and free of rust. Some users prefer a paste wax coating. Another option is
talcum powder applied with a blackboard eraser rubbed in vigorously once a week; this will fill casting pores
and form a moisture barrier. This method provides a table top that is slick and allows rust rings to be easily
wiped from the surface. Important also is the fact that talcum powder will not stain wood or mar finishes as
wax pickup does.
Summary of Contents for ST-330 TP
Page 13: ...13 PART DIAGRAM ...