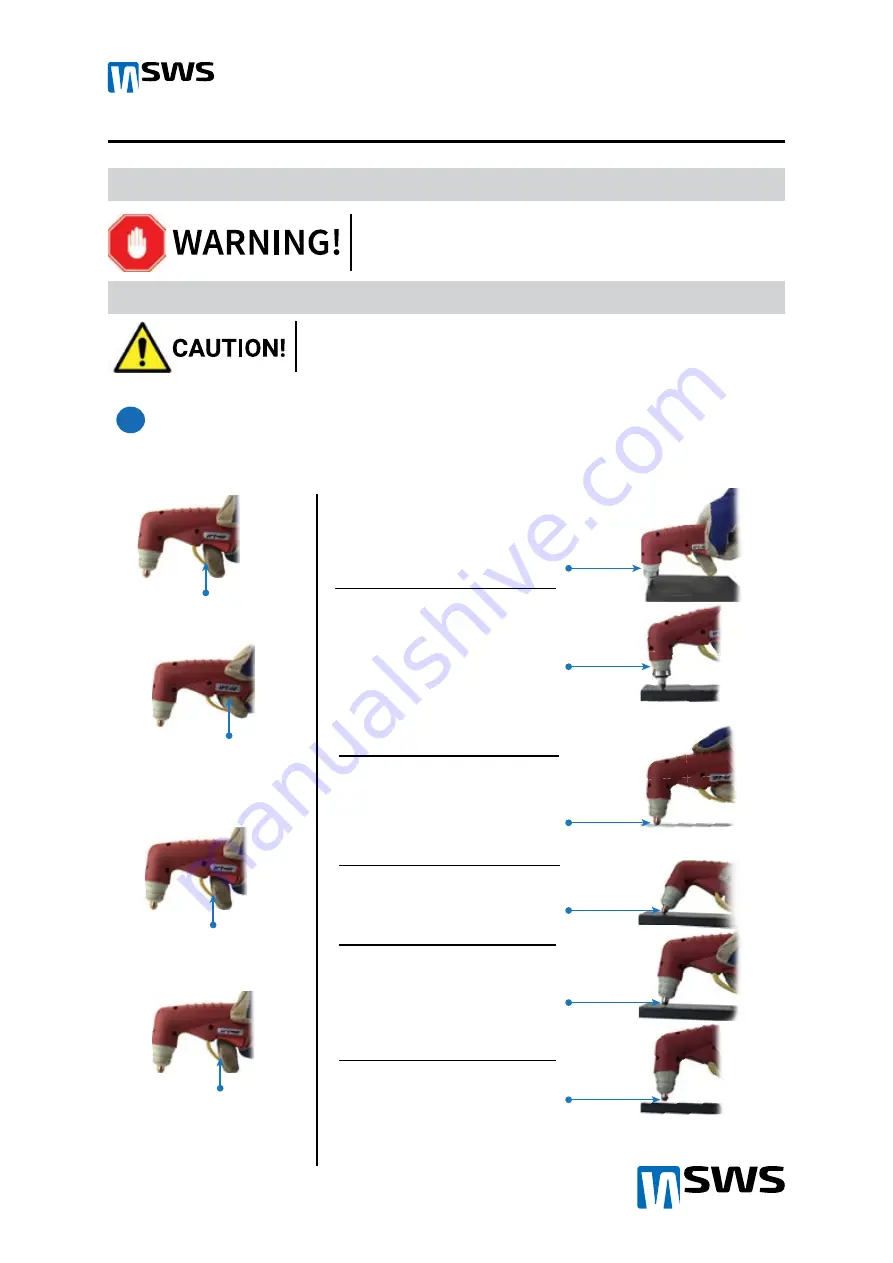
SPEEDCUT 50
SPEEDCUT 50
SPEEDCUT 50 OPERATING MANUAL
9
MACHINE OPERATION
7.0 Trigger
The pilot arc can cause serious burns - Never engage trigger
switch when torch is directed towards the eyes, face and body
of yourself and others.
Protect your eyes and body. Use an approved welding/plasma cutting
helmet at and filter lens shade #5 and wear protective clothing.
7.1 Operation
Pull trigger system will adjust air
pressure
then start pilot arc after
2 seconds.
Release trigger to stop arc and
start the cooling cycle
(15 seconds).
Pull then release trigger to stop
cooling cycle prematurely. (Will
cause premature tip wear if large
amounts of cutting have been
performed).
Push safety switch away with
finger.
Place standoff guide, drag tip, or position
torch tip 3‑9mm off the metal at 90 degrees
and pull the trigger. Once the cutting starts
begin to slowly move across the workpiece.
Adjust your speed so that sparks are coming
from the backside of the metal. If sparks are
not visible at the bottom of the metal, you are
not penetrating the metal. This can be caused
by moving too fast, insufficient amperage or
too thick of material for the rated capacity. At
the end of the cut angle, your torch past 90
degrees to completely sever the metal.
When cutting thinner materials typically
under 3mm, you can safely drag the
tip. Materials over this thickness may
prematurely wear the torch consumables.
To make a pierce cut sit the edge of
the nozzle on the metal and direct the
torch angle away from your body.
Once the material starts being
removed slightly lift and slowly
rotate the torch towards 90
degrees until you see sparks
coming from th underside of the
metal.
Once you have pierced a
hole through the material,
begin to make the cut at
90 degrees.
NOTE: Cut quality is highly dependent on setup and the cutting parameters such as alignment with
the workpiece, torch standoff, cutting speed, gas pressures, and operator ability.
i