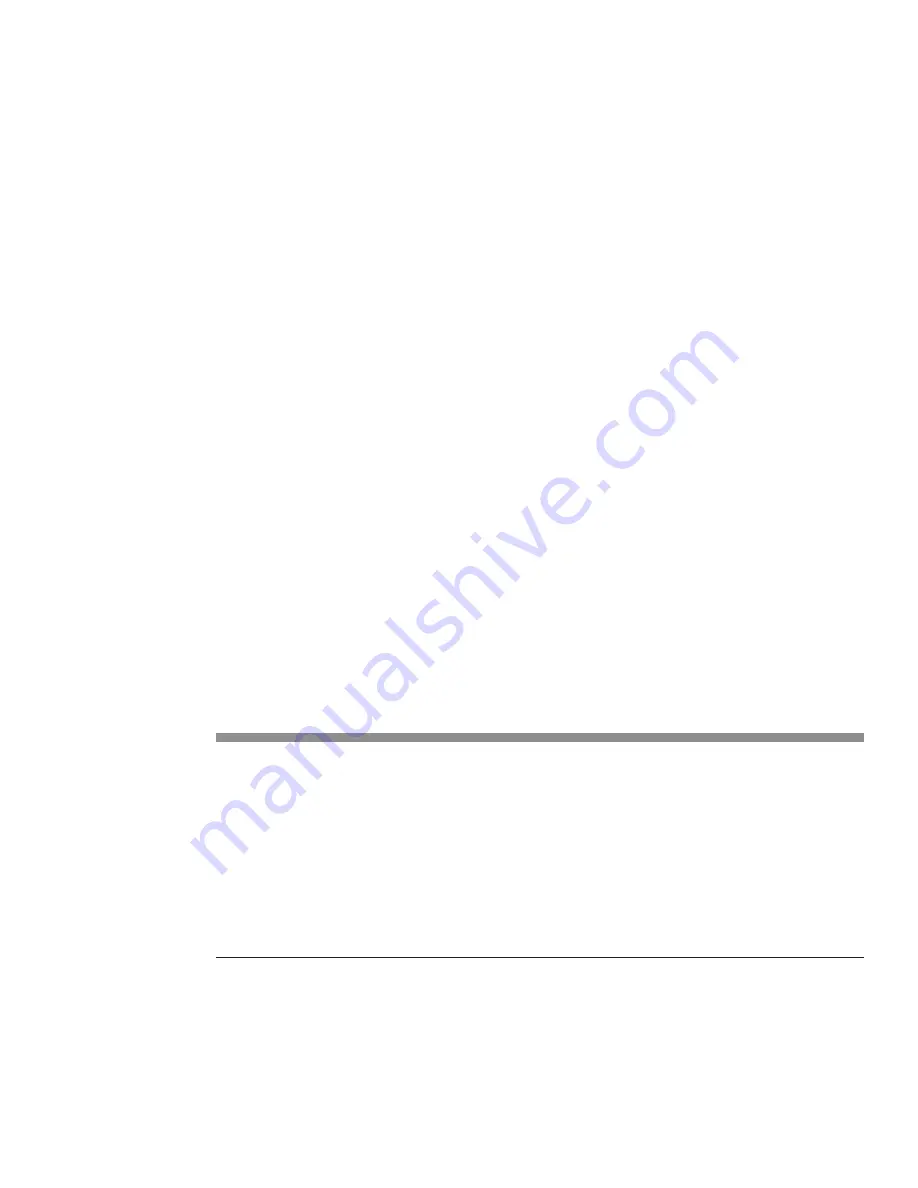
technical reference
3
5
Synrad
Firestar i401
operator’s manual
Technical overview
Note:
Optical components in the beam path must always be aligned to the actual beam path, not the
laser faceplate. Because of slight variations in laser construction, the beam path may not always
be centered in, or perpendicular to, the aperture in the faceplate.
Expander/collimators are optical devices that reduce beam divergence while at the same time increasing
beam diameter by a selectable magnification factor. Adding an expander/collimator substantially reduces
beam divergence and any variance in beam diameter caused by the changing optical path length in an XY
(“flying optics”) table application. In fixed-length delivery systems where the laser is positioned only one
meter away from the focusing optic and a small spot size is required, an expander/collimator is again the
best solution to provide the required beam expansion before reaching the focusing optic.
Focusing optics
When selecting a focusing optic, the primary consideration should be material thickness and any vertical
tolerances that occur during final part positioning rather than making a selection based only on minimum
spot size. The chosen focal length should create the smallest possible focused spot while providing the
depth of field required for the material to be processed.
Optics are fragile and must be handled carefully, preferably by the mounting ring only. Be careful to select
optics that are thick enough to withstand the maximum assist gas pressure available for the process. This is
especially important in metal cutting applications using high-pressure assist gases.
Cleanliness is another important issue affecting performance; a dirty or scratched lens will under perform
and exhibit a vastly shortened lifetime. When the laser application requires air as an assist gas, use only
breathing quality air available in cylinders from a welding supply company. Compressed shop air contains
minute particles of oil and other contaminants that will damage optical surfaces. If compressed shop air is
the only choice available, it must be filtered to the specifications shown in Table 3-1.
Table 3-1
Assist gas purity specifications
Assist Gas
Typical Purpose
Specification
Air
Cutting/Drilling
Breathing Grade
99.9996% purity or better
Air
Cutting/Drilling
Compressed
99.9950% purity or better, water-free; oil
filtered to 5 mg/m
3
or better; particulate
filtered to less than 1.0 micron
Argon
Welding
High Purity Grade
99.998% purity or better
Helium
Welding
High Purity Grade
99.997% purity or better
Nitrogen
Cutting/Drilling
High Purity Grade
99.9500% purity or better
Oxygen
Cutting/Drilling
Ultra Pure Grade
99.9998% purity or better