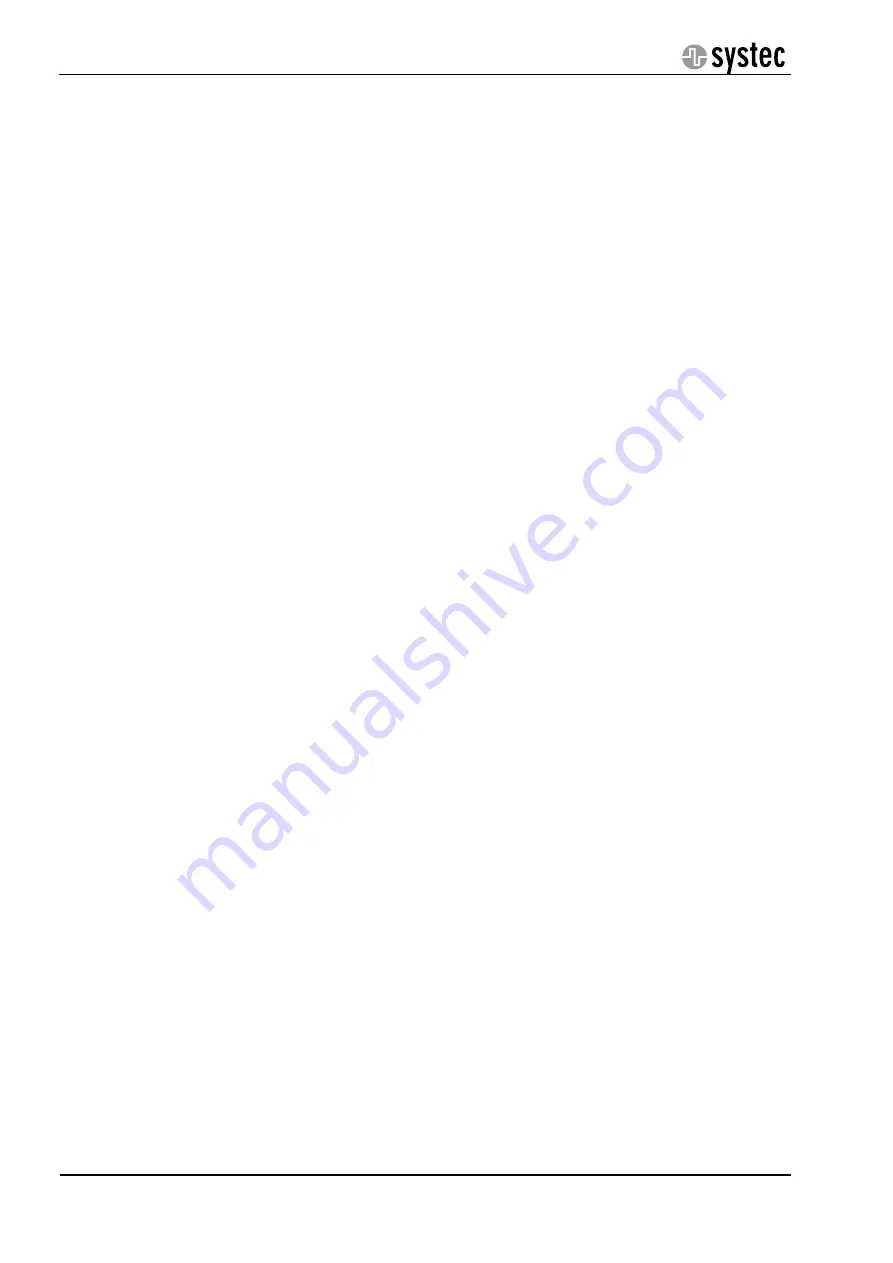
- 2 -
699-41-20.1
Systec Elektronik und Software GmbH
Nottulner Landweg 90
48161 Münster-Roxel
Germany
Telefon:
+49 / 25 34 / 80 01-70
Telefon:
+49-700-SYSTEC-DE
Telefax:
+49 / 25 34 / 80 01-77
internet:
eMail:
Maintenance for DriveSets
Docu-No.: 699-41-20.1
Latest revision date: 05 2017
Translation of the original manual
Copyright and all other rights to this document remain with Systec
GmbH. Systec does not take any responsibility for the correctness and/or
completeness of the contents. We reserve the right to make technical
changes.
You can download this document from the Systec website free of charge.
For this document, Systec GmbH grants you the simple charge-free right,
unlimited in space and time, for all known and not yet known types of
use. All rights with respect to patent grants or industrial design registration
and further rights remain unaffected.
You may duplicate this document. Distribution is only allowed with the
clear indication of the copyright held by Systec GmbH. You may not pro-
cess, modify or change this document in any other way. In order to dis-
tribute this document for commercial reasons and to make it available,
you will require prior written authorization from Systec GmbH.
© Copyright 2017: all rights reserved