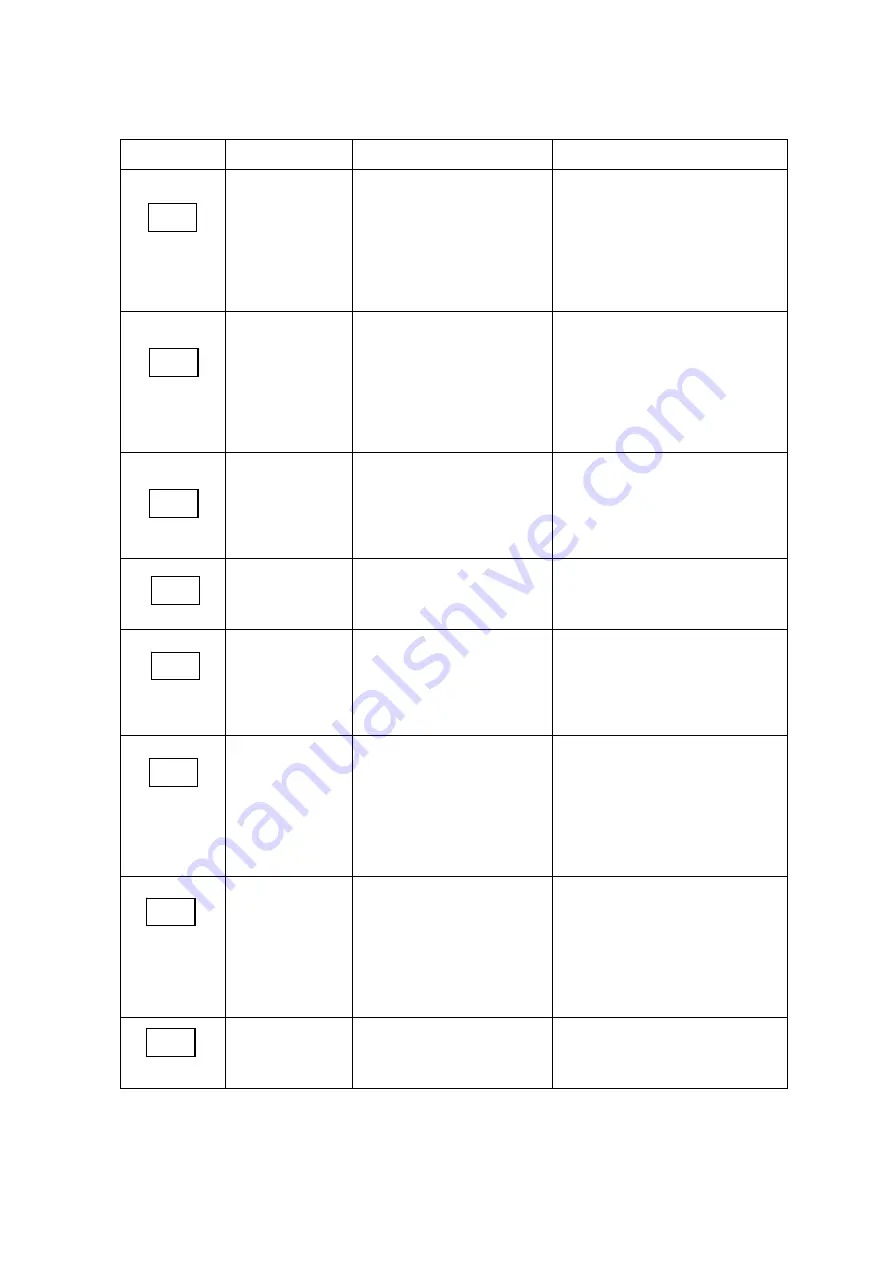
42
3.Manual Reset and Auto-Reset Operative Malfunction
INDICATION CONTENT
POSSIBLE
CAUSE
COUNTERMEASURE
Transient
over-current
starting machine
1. Motor coil short-circuit with
external casing
2. Motor connection wire
short-circuit with grounding
3. Transistor module
damaged
1. Examining motor
2. Examining wiring
3. Replace transistor module
Over-current at
acceleration
1. Acceleration time setting
too short
2. Improper V/F feature
selection
3. Applied motor capacity
exceeds inverter capacity
1.
Adjust acceleration time to
longer setting
2. Adjust to a proper V/F curve
3.
Replace and install another
inverter with appropriate
capacity
Over-current at
steady speed
1. Transient alteration of the
loading
2. Transient alteration of the
power supply
1. Examining the loading
configuration
2. Install inductor on the power
supply input side
Over-current at
deceleration
Deceleration setting too short
Adjust to use a longer
acceleration time
Over-current at
breaking
DC Breaking frequency,
breaking voltage, or
breaking time setting too
long
Adjust to reduce settings of
F_15, F_16, or F_17
Over-voltage at
operation/deceler
ation
1. Deceleration time setting
too short or inertial
loading too large
2. Power supply voltage
variation too large
1. Adjust to use a longer
deceleration time
2. Install a inductor on the power
supply input side
3. Increase the capacity of
inverter
Insufficient
voltage level at
operation
1. Power supply voltage too
low
2. Power supply voltage
variation too large
1. Improve power source quality
2. Adjust to use a longer
acceleration time
3. Increase capacity of inverter
4. Install a reactor on the power
supply input side
Heat-sink over
heated at
operation
1. Loading too heavy
2. Ambient temperature too
high or poor ventilation
1. Examining the loading
2. Increase capacity of inverter
3. Improve ventilation
OCS
OCA
OCC
OCd
OCb
OVC
LVC
OHC