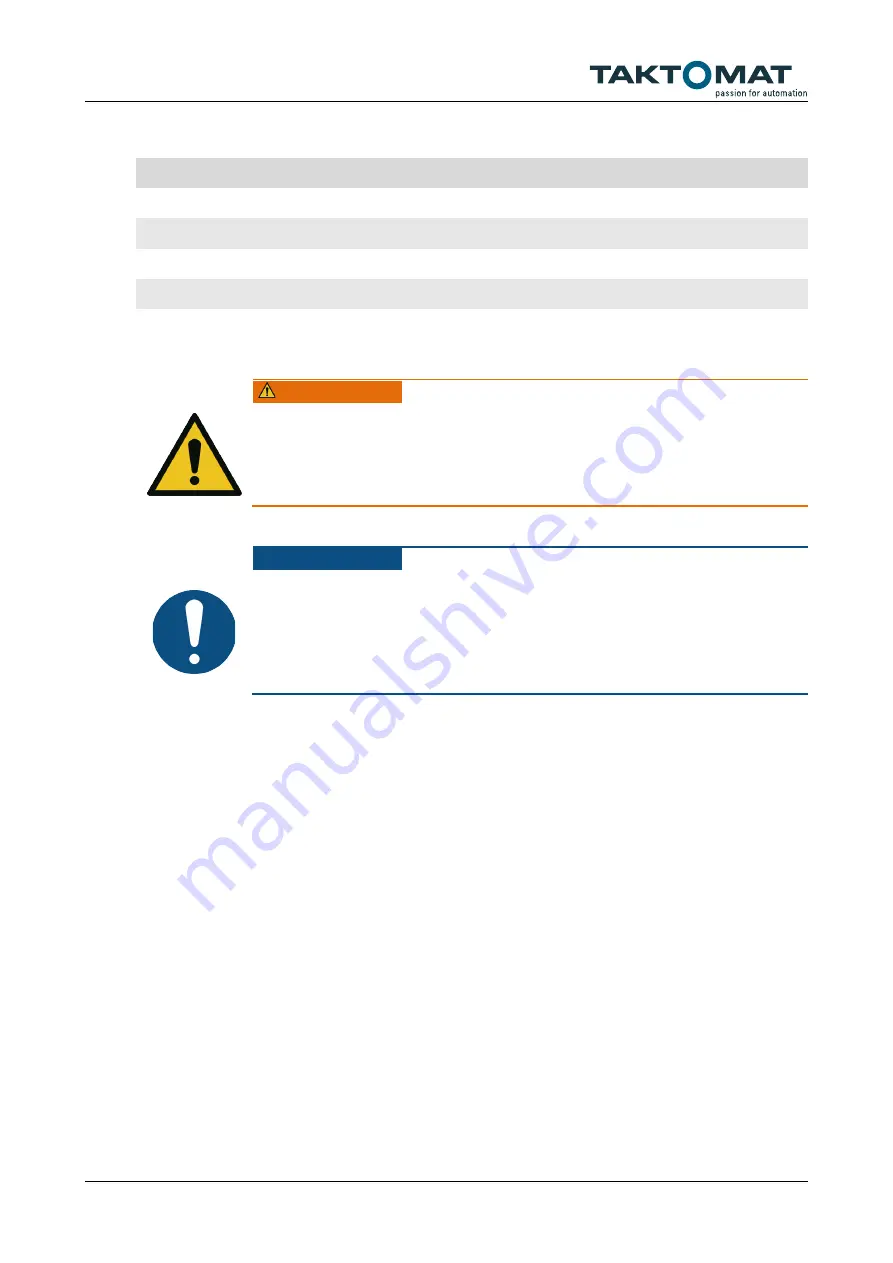
Assembly instructions
Maintenance
Version 1.0
Rotary indexer TMF
29 / 35
Overview of relubrication quantities for TMF series with grease nipple
Product
Divide the relubrication quantity between the respective number of grease nipples
TMF3000
26 g
TMF4000
34 g
TMF5000
49 g
TMF8000
128 g
7.3
Replacing the cam follower
WARNING
Unexpected start-up of movable components
Persons can be hit by moving components and seriously injured.
•
Disconnect the power and/or energy supply before the assembly work and secure against
reconnection
NOTICE
Damage to components
Insufficient protection against contamination/dirt can cause material damage.
•
Do not allow foreign bodies to get inside the mechanics
•
Cover holes to protect against penetrating dirt
•
Clean clearance holes and shafts before assembly
If clearance occurs in one or multiple stations when checking the rotary indexer, the cam followers must be replaced.
The rotary indexer must be completely disconnected from the power supply to ensure that the dismantling and maintenance
of the cam follower are carried out safely and efficiently. All external attachments that prevent access to the cam followers
must be dismantled properly.
The following tools are required to prepare for dismantling of the cam followers:
•
Double hook, slotted screwdriver
•
Retaining ring pliers for internal rings
•
Internal extractor
•
Hexagon socket wrench for hexagon head screws
The following spare parts and wearing parts are recommended:
•
Cap plug
•
Retaining ring
•
Schnorr lock washer
•
TKR Taktomat cam follower