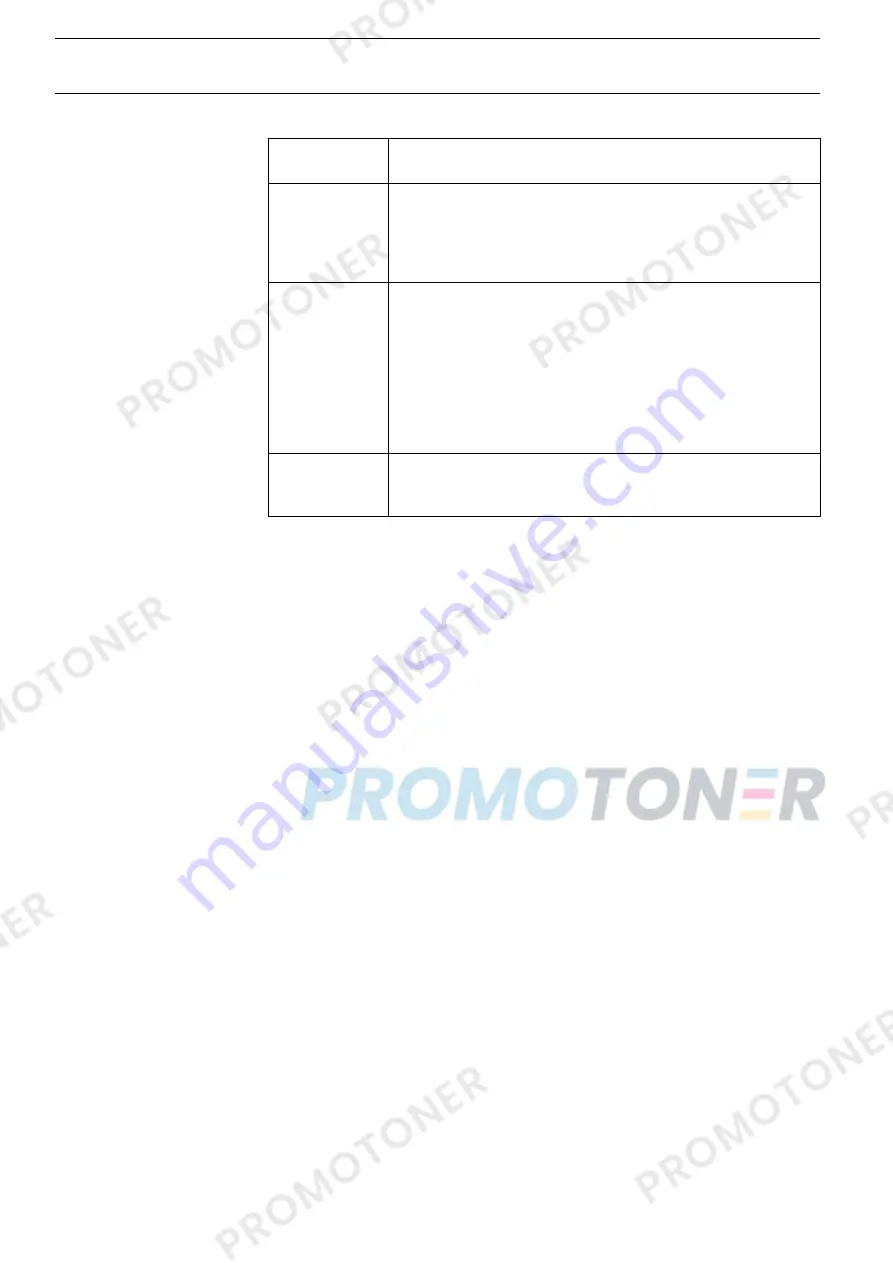
Printing paper
Recycling paper made of 100% waste paper (to DIN 19 309)
can be processed.
Set of forms
Sets of forms may be used only if the top edge is bound. The
binding edge should be as soft as possible. A wavy binding
edge may hamper the smooth feeding of these sets. Multi-part
forms have to be inserted with the glued top facing down.
Multi-part forms should be tested for suitability.
Paper quality
Light pulp paper of medium fine quality, paper bearing the
quality mark SM Post and photocopy paper are suitable for
use. Unsuitable are: satin-finisch or coated papers, imitation
art papers, and embossed papers.
Since paper as natural material reacts strongly to
environmental influences (e.g. humidity, temperature), the
place of storage should be selected carefully. We recommend
that this kind of paper should be tested extensively before
larger quantities are acquired.
Coloured
paper
Should papers with a dark reverse side be used, these should
also be tested for their functionality. Please pay attention to the
use of infrared reflecting colors, when acquiring these papers.
Paper specifications
Specifications
2-6
Summary of Contents for T2040
Page 1: ...Maintenance Manual Matrix Printer T2040 T2140...
Page 2: ......
Page 6: ......
Page 8: ......
Page 20: ......
Page 40: ......
Page 84: ...6 4 Power supply 120 V 047 832 220 240 V 047 831 Power supply Spare parts and schematics 6 8...
Page 85: ...Spare parts and schematics Power supply 6 9...
Page 89: ...Spare parts and schematics Controller 6 13...
Page 90: ...Controller Spare parts and schematics 6 14...
Page 91: ...Spare parts and schematics Controller 6 15...
Page 92: ...Controller Spare parts and schematics 6 16...
Page 93: ...Spare parts and schematics Controller 6 17...
Page 94: ...Controller Spare parts and schematics 6 18...
Page 97: ...6 6 Panel board 060 477 Clamp panel cable 054 589 Spare parts and schematics Panel board 6 21...
Page 98: ...Panel board Spare parts and schematics 6 22...
Page 101: ...Spare parts and schematics Head connection 6 25...
Page 104: ......