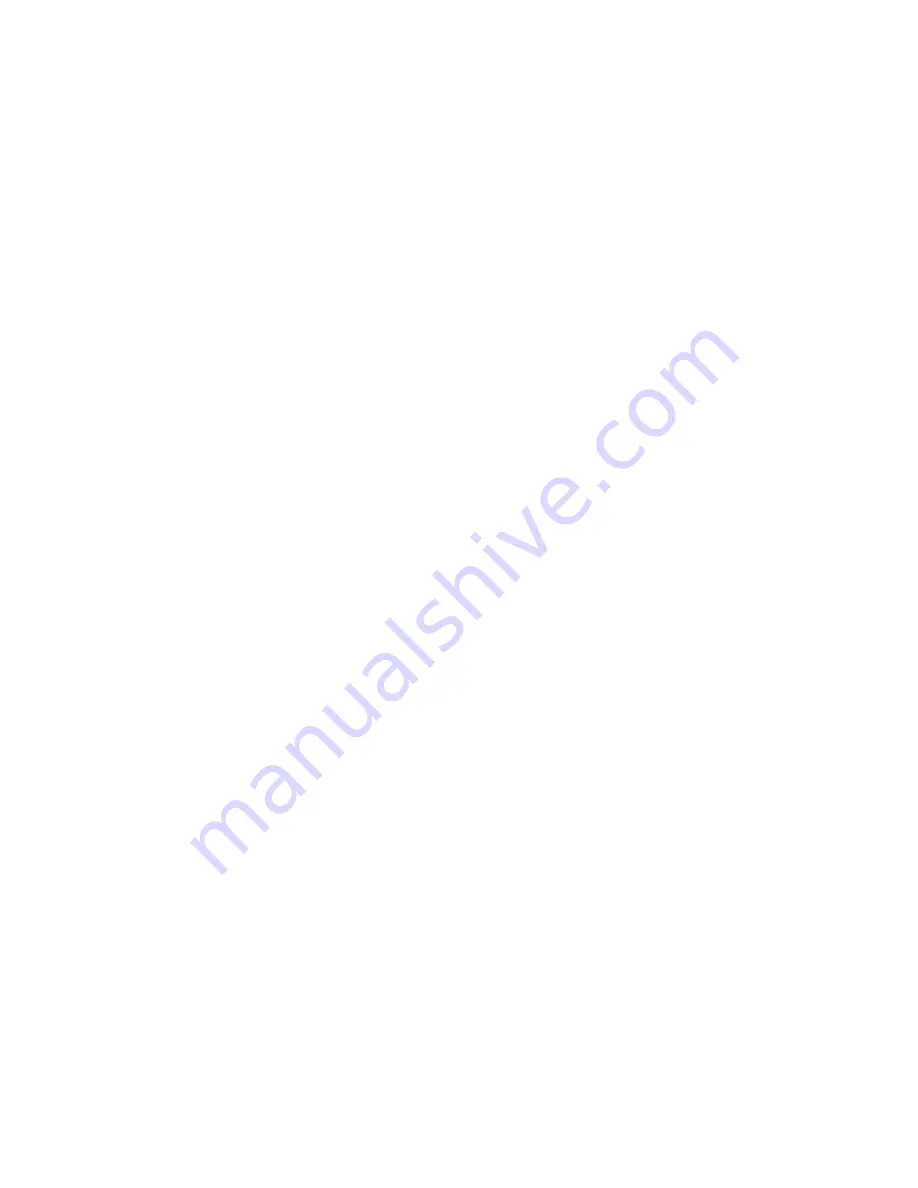
16
Tamarack Industries CONDITIONS OF SALES & LIMITED WARRANTY
All sales made by Tamarack Industries, here after ref-
ered to as Tamarack, a Division of ELJO Industries Inc.
are subject to these conditions unless otherwise agreed
in writing with a duly authorized officer of Tamarack. In
all cases of conflict between these conditions and the
requirements of the purchase order, these conditions
shall prevail.
(1) SALES POLICY:
Nothing herein shall be construed
as abridging the right of Tamarack to sell directly or indi-
rectly to: (a) Federal, State or Provincial Governments
or Agencies thereof, or to Agencies employing Federal,
State or Provincial Government aid; (b) Purchasers
who buy Tamarack's products for sale as integral or as-
sembled parts of their products; (c) Firms operating on a
national scale; (d) Any other class of purchaser to whom
Tamarack may from time to time, elect to sell.
(2) PRICES:
All prices are F.O.B. our warehouses,
freight allowance as specified on Distributor Net Price
Lists. The suggested list prices and discounts schedules
are established by Tamarack and are intended to act as
a guide for our distributors. Unless otherwise stated in
writing, prices are subject to change without notice and
will be applied as in effect at time of shipment.
(3) TERMS:
Unless otherwise agreed upon in writing by
an officer of Tamarack, all invoices become due and pay
-
able net 30 days following the date in invoice. Interest
at the maximum legal rate will be charged on all overdue
accounts. Minimum net charge per invoice is $75.00
(4) CANCELLATION AND CHANGES:
No orders or
sales may be cancelled or changed without the consent
of Tamarack. At Tamarack's option cancelled/changed
orders are subject to payment of cancellation charges
equal to all costs incurred by Tamarack up to the date
of cancellation/change.
(5) DELAYED DELIVERIES:
Tamarack shall not be
liable for any delay of merchandise for any cause what-
soever.
(6) CLAIMS:
All goods shall be deemed delivered to pur-
chaser at the time they are placed in the hands of carrier
and consigned to purchaser: loss, damage or destruc-
tion of any said merchandise is assumed by purchaser.
No claims may be made for shortages unless made in
writing within ten days from receipt of merchandise.
(7) RETURN OF GOODS:
Written permission from
Tamarack must be obtained before returning any mer-
chandise. All transportation charges must be borne by
the purchaser. Credit for returned goods will be based
on the original price paid, less 20%. Special parts or
custom-built items cannot be returned for credit.
(8) LIMITATION OF LIABILITY:
Tamarack's liability on
any claim of any kind, including negligence, for any loss
or damage arising out of, connected with, or resulting
from contract, or the performance or breach thereof, or
the design, manufacture, sale, delivery, resale, installa-
tion, technical direction of installation, inspection, repair,
operation or use of any equipment covered by or fur-
nished under contract shall in no case exceed the price
paid by the purchaser for the equipment. Tamarack also
disclaims all purchaser for the equipment. Tamarack
also disclaims all liability, whether in contract, tort, war-
ranty, or otherwise, to any party other than purchaser.
(9)
All Price Lists, Catalogues and other material shall re-
main the property of Tamarack and are subject to return
on demand. The Suggested List Prices are established
by Tamarack and are intended to act as a guide. All
shipping weights shown are approximate.
LIMITED TAMARACK WARRANTY
For one year from date of purchase, Tamarack will re-
place or repair for the original purchaser, free of charge,
any part or parts, found upon examination by any
Tamarack Authorized Service Depot or by the Tamarack
factory, to be defective in material or workmanship or
both. Equipment and accessories not manufactured
by Tamarack are warranted only to the extent of the
original manufacturer's warranty. All transportation
charges on parts submitted for replacement or repair
under this warranty must be borne by the purchaser.
For warranty service contact your nearest Tamarack
Authorized Service Depot.
THERE IS NO OTHER EXPRESS WARRANTY,
IMPLIED WARRANTIES, INCLUDING THOSE OF
MERCHANTABILITY AND FITNESS FOR A PARTICU-
LAR PURPOSE ARE LIMITED TO ONE YEAR FROM
PURCHASE AND TO THE EXTENT PERMITTED BY
LAW. LIABILITY FOR CONSEQUENTIAL DAMAGES
UNDER ANY AND ALL WARRANTIES ARE EXCLUD-
ED TO THE EXTENT EXCLUSION IS PERMITTED BY
LAW. (THIS WARRANTY IS AN ADDITION TO ANY
STATUTORY WARRANTY.)
P.O. Box 234, Station "L"
Winnipeg, Manitoba
Canada R3H 0Z5
WARRANTY VOID IF NOT REGISTERED