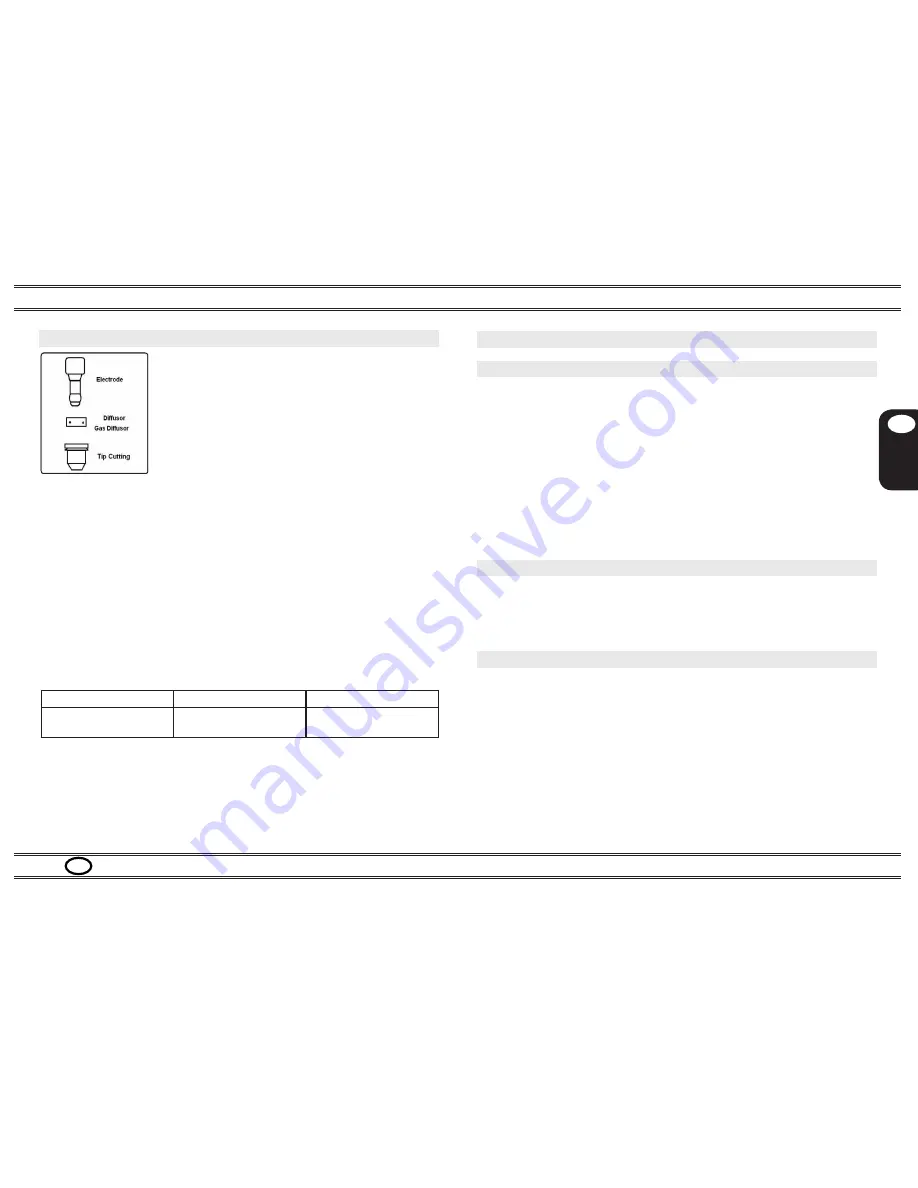
OPERATING MANUAL
PLASMA CUTTING
GB
Inglese
GB
5. Replacing consumer parts
Always shut off the machine before replacing consumer parts.
The electrode must be replaced when it has a crater in the center approximately 1
mm deep.
The diffuser must be replaced when some areas are blackened. Due to its small
size, is very important to position it correctly during assembly (see fig. 4).
The gas nozzle or tip cutting must be replaced when the hole is no longer smooth
and the cutting capacity is diminished.
The nozzle holder must be replaced when the insulating part is deteriorated.
For the best cutting performances, use the following tip cutting-nozzle holder com-
bination ( for order code see Spare part section)
Table 4: spare parts
Current/Model
From 13 to 18 Amp
From 18 to 25 Amp
Site Cut 10
Tip diameter 0,65 mmnoz-
zle holder with 2 holes
Tip diameter 0,8 mmnozzle
holder with 2 holes
Make sure that the electrode, the diffuser an the gas nozzle are mounted
correctly, and that the nozzle holder is firmly tightened
If any of this parts are missing, this will interfere with smooth operation of
the machine and, especially, jeopardize operator safety.
Picture 8 : mouting schematic
6. Cutting errors
6.1 Insufficient penetration
This error may be caused by the following:
High speed. Always make sure that the arc fully penetrates the workpiece
and is never held at a forward angle of more than 10-15°. This will avoid
incorrect consumption of the nozzle and burns to the nozzle holder.
Excessively thick workpiece This inverter cut
8
mm. Max and 1
0
mm.
severance .
Grounding clamp not in good electrical contact with the workpiece.
Worn nozzle and electrode.
Cutting current too low.
NOTE: when the arc does not penetrate, the molten metal scraps obstruct
the nozzle.
6.2 The cutting arc goes off
This error may be caused by:
Worn nozzle, electrode or swirl ring.
Air pressure too high.
Supply voltage too low.
6.3 Shorter life of consumer parts
This error may be caused by:
Oil or dirt in the arc intake.
Unnecessarily long pilot arc.
Low air pressure.
Make sure that the new electrode and nozzle to be mounted are thoroughly clean
and degreased.
Always use original spare parts to avoid damaging the torch.
•
•
•
•
•
•
•
•
•
•
•
•
PAGE 7