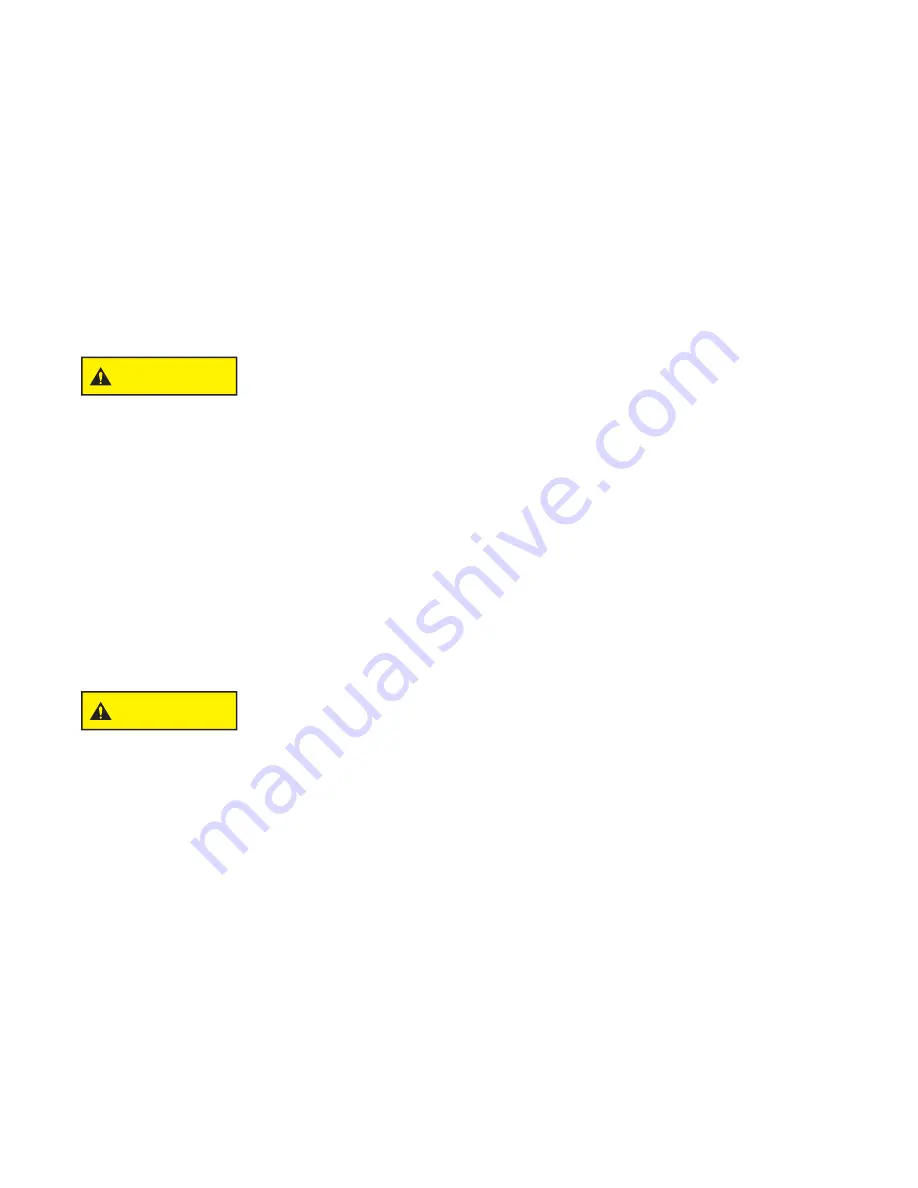
©Copyright Task Force Tips LLC 2002 - 2020
LKF-100 January 22, 2020 Rev20
19
12.0 MAINTENANCE
TFT products are designed and manufactured to be damage resistant and require minimal maintenance. However, as the primary
fi
re
fi
ghting tool upon which your life depends, it should be treated accordingly. To help prevent mechanical damage, do not drop or
throw equipment.
12.1 FIELD LUBRICATION
All Task Force Tips nozzles are factory lubricated with high quality silicone grease. This lubricant has excellent wash out resistance,
providing long term performance in
fi
re
fi
ghting nozzles. If your department has unusually hard or sandy water, the moving parts of the
nozzle may be a
ff
ected. Foam agents and water additives contain soaps and chemicals that may break down the factory lubrication.
The moving parts of the nozzle should be checked on a regular basis for smooth and free operation, and for signs of damage. IF
THE NOZZLE IS OPERATING CORRECTLY, THEN NO ADDITIONAL LUBRICANT IS NEEDED. Any nozzle that is not operating
correctly should be immediately removed from service. The nozzle can be returned to the factory at any time for a complete checkup
and relubrication with silicone grease.
The
fi
eld use of Break Free CLP (spray or liquid) lubricant will help to temporarily restore the smooth and free operation of the nozzle.
These lubricants do not have the washout resistance and long-term performance of the silicone grease. Once Break Free CLP is
applied, re-application will be needed on a regular basis until the nozzle can be returned to the factory for a complete checkup and
relubrication with silicone grease.
CAUTION
Aerosol lubricants contain solvents that can swell O-Rings if applied in excess. The swelling can
inhibit smooth operation of the moving parts. When used in moderation, as directed, the solvents
quickly evaporate without adversely swelling the O-Rings.
12.2 SERVICE TESTING
In accordance with NFPA 1962, nozzles must be tested a minimum of annually. Nozzles failing any part of this test must be removed
from service, repaired and retested upon completion of the repair.
12.3 REPAIR
Factory service is available with repair time seldom exceeding one day in our facility. Factory serviced equipment is repaired by
experienced technicians, wet tested to original speci
fi
cations, and promptly returned. Repair charges for non-warranty items are
minimal. Any returns should include a note as to the nature of the problem and whom to reach in case of questions.
Repair parts and service procedures are available for those wishing to perform their own repairs. Task Force Tips assumes no
liability for damage to equipment or injury to personnel that is a result of user service. Contact the factory or visit the web site at tft.
com for parts lists, exploded views, test procedures and troubleshooting guides. All replacement parts must be obtained from the
manufacturer to assure proper operation of the product, and to maintain approval of the device.
Performance tests shall be conducted on the equipment after a repair, or anytime a problem is reported to verify operation in
accordance with TFT test procedures. Consult factory for the procedure that corresponds to the model and serial number of the
equipment. Any equipment which fails the related test criteria should be removed from service immediately. Troubleshooting guides
are available with each test procedure or equipment can be returned to the factory for service and testing.
CAUTION
Any alterations to the product or its markings could diminish safety and constitutes a misuse of
this product.