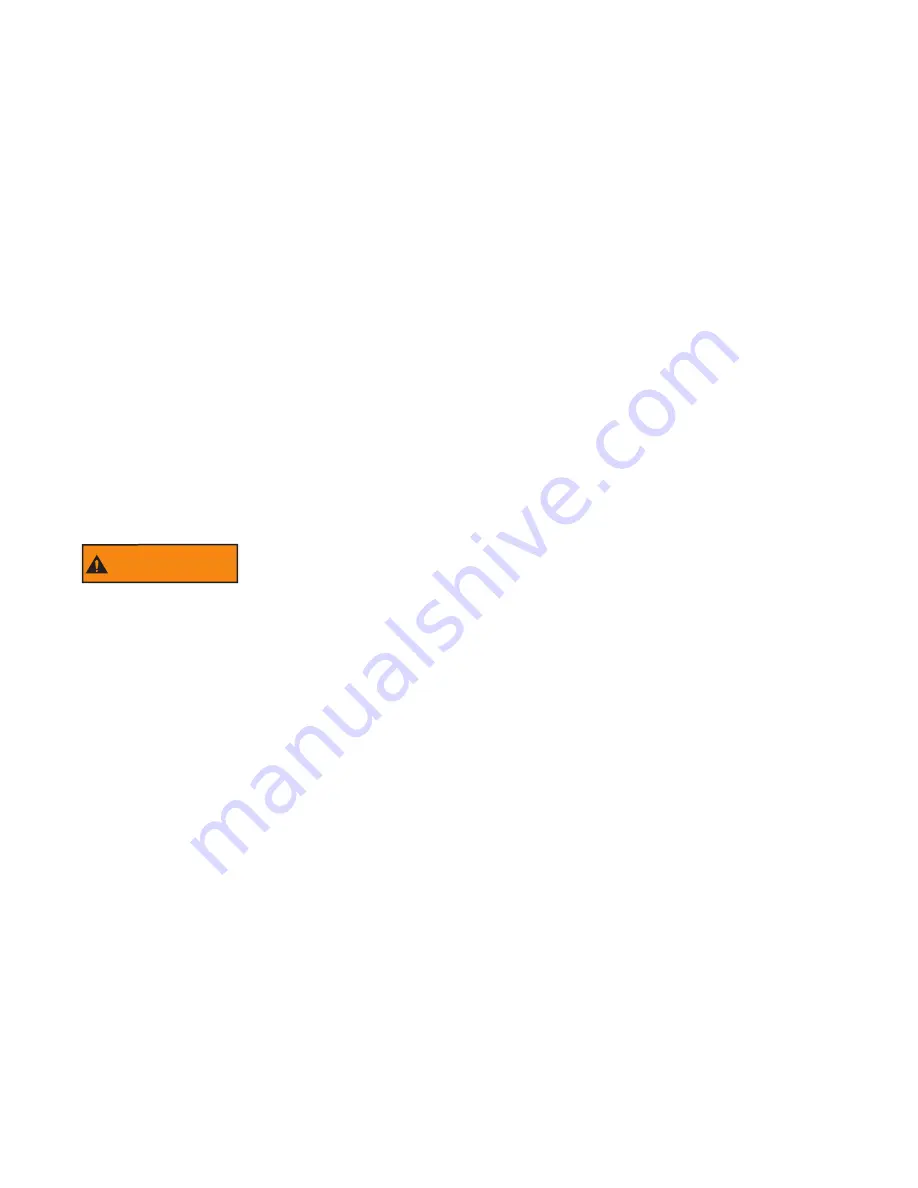
©Copyright Task Force Tips LLC 2002 - 2020
LKF-100 January 22, 2020 Rev20
9
5.2.2 FLUSH CONTROL
Small debris passes may get caught inside the nozzle. This trapped material will cause poor stream quality, shortened reach, and
reduced
fl
ow. To remove small debris, the nozzle may be
fl
ushed as follows:
• While still
fl
owing water, rotate the index ring counterclockwise (as viewed from behind the nozzle) to the Flush setting. This
will open the nozzle allowing debris to pass through.
• During
fl
ush the nozzle reaction will decrease as the pattern becomes wider and the pressure drops. The nozzle operator must
be prepared for an increase of nozzle reaction when returning the nozzle from the
fl
ush position to retain control of the nozzle.
• Rotate the index ring out of
fl
ush to continue normal operations.
WARNING
Large amounts or pieces of debris may be un
fl
ushable and can reduce the
fl
ow of the nozzle
resulting in an ine
ff
ective
fl
ow. In the event of a blockage, it may be necessary to retreat to a safe
area, uncouple the nozzle and remove debris.
5.2.3 SHUTOFF SETTING (TIP-ONLY MODELS)
On Tip Only models, the index ring has a shuto
ff
setting to stop the nozzle
fl
ow. To shut o
ff
the nozzle, rotate the index ring clockwise
(as seen from the operating position behind the nozzle) into the “OFF” position. Rotate counterclockwise into a
fl
ow setting to open
the nozzle.
5.3 PATTERN CONTROL
TFT’s nozzles have full pattern control from straight stream to wide fog. Turning the stream shaper clockwise (as seen from the
operating position behind the nozzle) moves the shaper to the straight stream position. Turning the shaper counterclockwise will
result in an increasingly wider pattern.
Since the stream trim point varies with
fl
ow, the stream should be “trimmed” after changing the
fl
ow to obtain the straightest and
farthest reaching stream. To properly trim the stream,
fi
rst open the pattern to narrow fog. Then close the stream to parallel to give
maximum reach.
Note: Turning the shaper further forward will cause stream crossover and reduce the e
ff
ective reach of the
nozzle.
The nozzle reaction is greatest when the shaper is in the straight stream position. The nozzle operator must be prepared for a change
in reaction as the pattern is changed.
Care must be taken to avoid dents or nicks in the nozzle tip because they can seriously a
ff
ect the stream reach.
5.4 QUADRACUP NOZZLES
The QuadraCup nozzle is capable of producing aspirated foam as well as conventional straight stream and wide protective fog
patterns. The QuadraCup functions just like the QuadraFog nozzle when the aspirating sleeve is in the retracted position.
To use the aspirating feature of the QuadraCup, slide the aspirating sleeve portion of the nozzle forward. Rotation of the shaper while
the sleeve is extended provides the nozzle operator control of reach and aspiration. If an immediate wide protective fog pattern is
needed, the sleeve can be retracted instantly to its regular position.
5.0 NOZZLE CONTROLS
5.1 FLOW CONTROL
Nozzle control valves must be opened slowly to eliminate unnecessary strain on the hose and couplings, and reduce pressure
surges.
Nozzles attached to an in-service hose shall be stored in the o
ff
position
5.1.1 LEVER TYPE FLOW CONTROL (BALL VALVE)
Models with a ball valve are shut o
ff
when the valve handle is fully forward. Pulling back on the handle opens the valve. TFT
recommends the use of a pistol grip for easier handling. For additional stress reduction, a hose rope or strap may also be used. This
permits more e
ff
ective use and ease of advancement, while minimizing strain and fatigue.
Note: In partially open positions, a ball
valve will cause turbulence and adversely a
ff
ect stream quality.
5.2 INDEX RING
5.2.1 FLOW SETTING
The index ring is marked with various
fl
ow settings. Turn the index ring so the desired setting lines up with the silver indicator pin. A
spring-loaded detent is provided at each
fl
ow setting. The nozzle will
fl
ow the indicated amount when the pressure at the nozzle is
100 psi (7 bar) on standard versions, or 75 psi (5 bar) on low pressure versions.