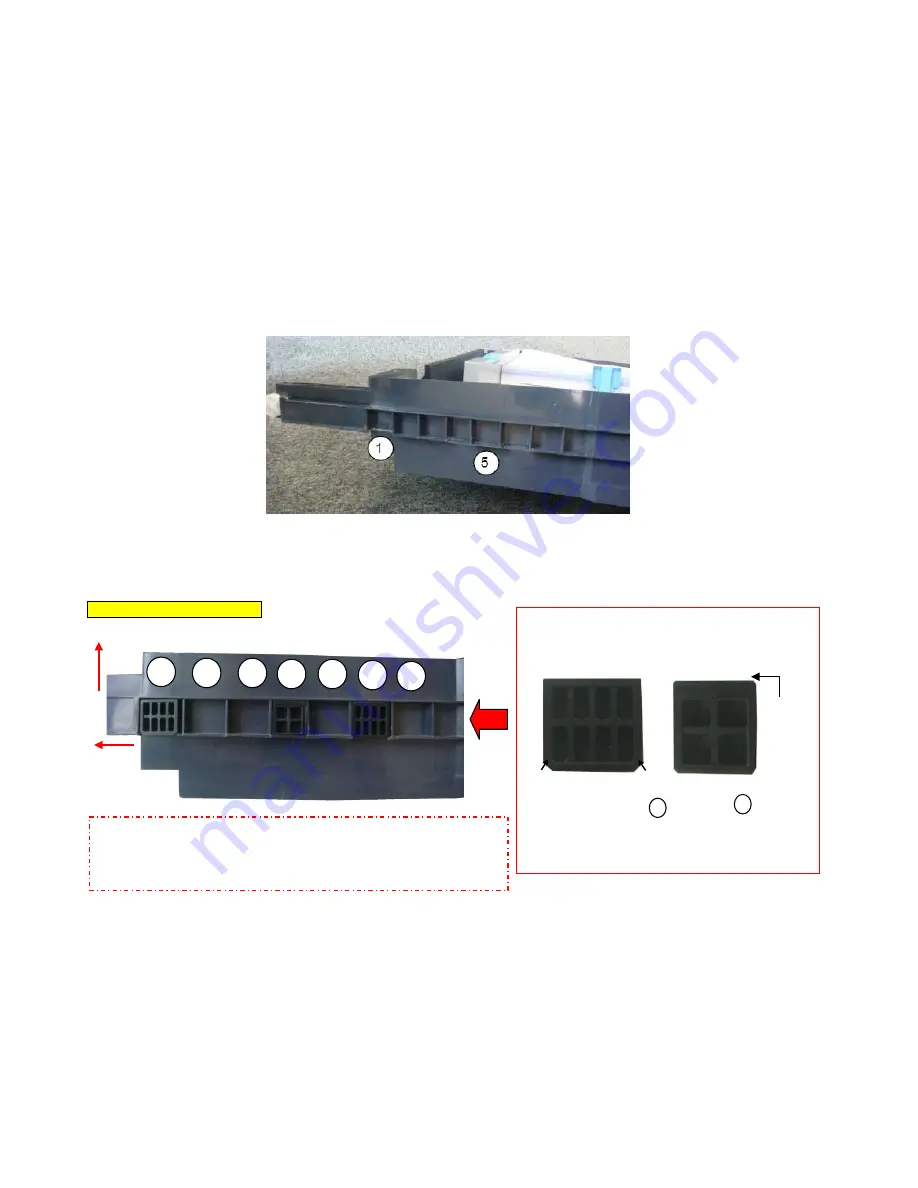
The Cassette Rails Damage (1/2)
●
Note the parts to use and the direction to install differ between before and after the damage.
①
: may contact the pulley A in the figure left and may be broken if pulled out just before full open and the downward force is
applied to the cassette.
②
: may contact the pulley B in the figure left and may be broken if repeatedly pulled out with paper fully loaded in the cassette.
※Others than 1 and 5 above may be damaged depending on the position where the cassette is pulled out
<Cassette rail damage position> 1 and 5 are mostly damaged in the figure below.
302K909680
PARTS A RAIL
CASSETTE SP
302K909690
PARTS B RAIL
CASSETTE SP
For repairing the broken rail--- apply to damaged rail
1
2
3
4
5
6
7
[Where to fit/direction]
Reinforcing parts
-- large (No2)
Reinforcing parts
-- small (No3)
Cassette rear
side
Corner cut
Flange
(Note)
The reinforcing parts can not be installed depending on
the cassette rail damage. In this case, cut the bottom of the
damaged part in the cassette rail where interferes the reinforcing
parts by using a nippers.
- Apply to other than 4
in the figure left
- Install with the corner
cut facing down
- Apply to 4 in the
figure left
- Install with the flange
facing up
Cassette upper side
Corner cut
(Cassette left side)
110
Summary of Contents for 6500i
Page 48: ... The film attached procedure J49XX J50XX J51XX J600X 3 9 48 ...
Page 52: ... Replacement procedure for the bushing J49XX J50XX J51XX J600X 7 9 52 ...
Page 57: ... The film attached procedure J6100 J6110 DF 3 6 57 ...
Page 71: ... The film attached procedure Corner Folding 3 6 71 ...
Page 73: ...Corner Folding 5 6 73 ...
Page 74: ...Corner Folding 6 6 74 ...
Page 103: ...Abnormal sound from the fuser section 3 5 For 3500i 4500i 5500i 103 ...
Page 104: ...Abnormal sound from the fuser section 4 5 For 3500i 4500i 5500i 104 ...